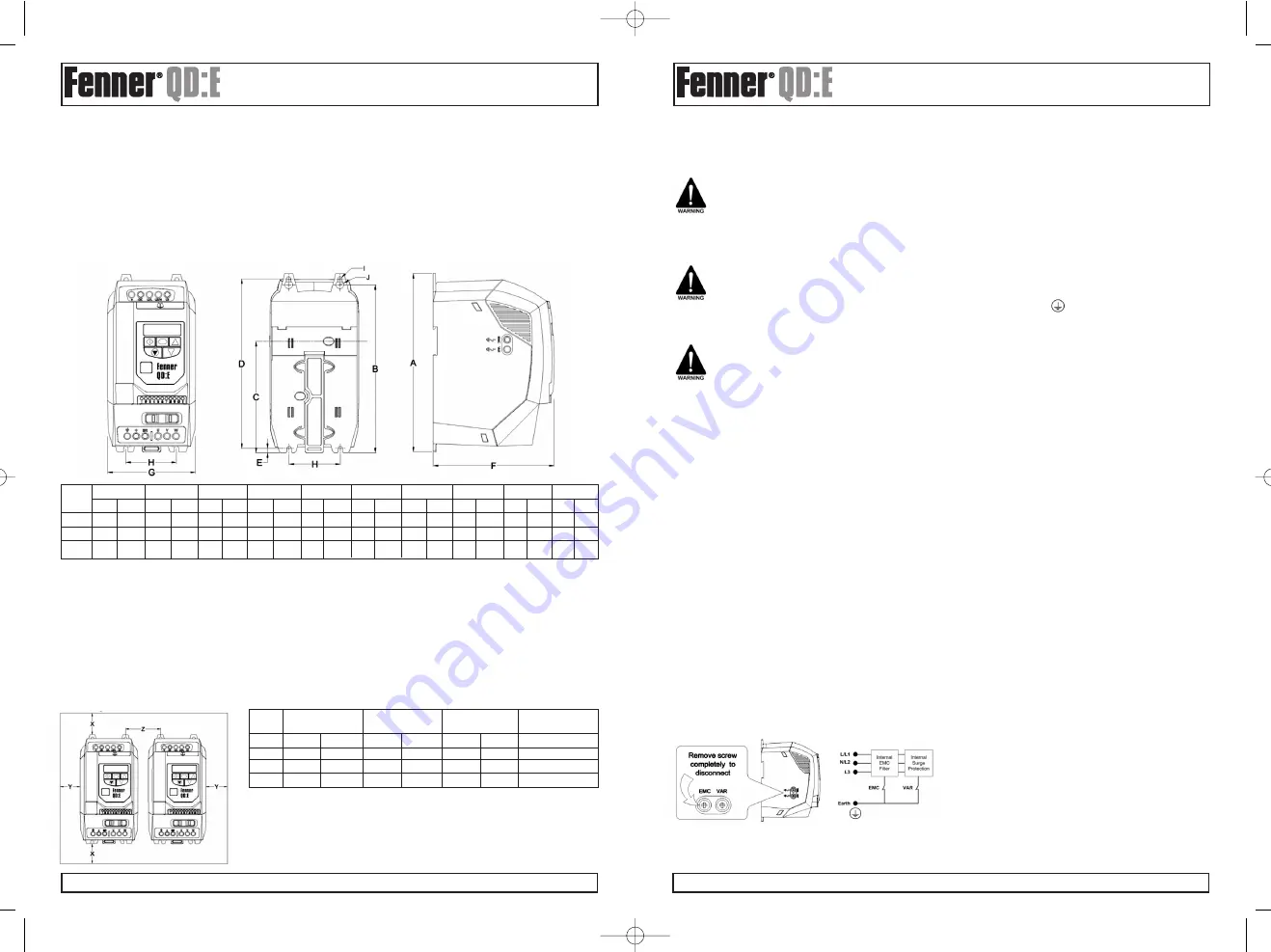
Installation & Operating Instructions
ııııııııııııııııııııııııııııııııııııııııııııııııııııııııııııııııııııııııııııııııııııııııııııııııııııııııııııııııııııııııııııııııııııııııııııııııııııııııııııııııııııııııııııııııııııııııııııııııııııııııııııııııııııııııııııııııııııı
Page 7
www.fptgroup.com
Fenner is a registered trademark of J.H. Fenner & Co. Limited
ııııııııııııııııııııııııııııııııııııııııııııııııııııııııııııııııııııııııııııııııııııııııııııııııııııııııııııııııııııııııııııııııııııııııııııııııııııııııııııııııııııııııııııııııııııııııııııııııııııııııııııııııııııııııııııııııııııı
Page 6
www.fptgroup.com
Fenner is a registered trademark of J.H. Fenner & Co. Limited
Installation & Operating Instructions
3. M
ECHANICAL
I
NSTALLATION
3.1. G
ENERAL
• Store the Fenner QD:E drive in its box until required. Storage should be clean and dry and within the temperature range –40°C to +60°C
• Install the Fenner drive on a flat, vertical, flame-resistant, vibration-free mounting within a suitable enclosure, according to
EN60529 if specific Ingress Protection ratings are required
• The drive must be installed in a pollution degree 1 or 2 environment
• Sizes 1 & 2 are DIN rail mountable, Size 3 is not DIN rail mountable.
• Ensure that all terminals are tightened to the appropriate torque setting
3.2. M
ECHANICAL DIMENSIONS AND MOUNTING
Drive
A B
C D
E
F G
H I
J
Size
mm in mm in mm
in mm
in mm in mm in mm in mm in mm in mm in
1 173 6.81 160 6.30 109 4.29 162
6.38 5.0 0.20 123 4.84 82 3.23 50 1.97 5.5 0.22 10
0.39
2 221 8.70 207 8.15 137 5.39 209 8.23 5.3 0.21 150 5.91 109 4.29 63 2.48 5.5 0.22 10 0.39
3 261 10.28 246 9.69 -
- 247 9.72 6.0 0.24 175 6.89 131 5.16 80 3.15 5.5 0.22 10 0.39
Control Terminal Torque Settings of 0.5 Nm (4.5 lb-in)
Power Terminal Torque Settings of 1 Nm (9 lb-in)
3.3. E
NCLOSURE MOUNTING
For applications that require a higher IP rating than the IP20 offered by the standard drive, the drive must be mounted in a
metallic enclosure. The following guidelines should be observed for these applications:
• Enclosures should be made from a thermally conductive material.
• When vented enclosures are used, there should be venting above the drive and below the drive to ensure good air
circulation. Air should be drawn in below the drive and expelled above the drive.
• If the external environment contains contamination particles (e.g. dust), a suitable particle filter should be fitted to the vents
and forced ventilation implemented. The filter must be serviced / cleaned appropriately.
• High moisture, salt or chemical content environments should use a suitably sealed (non-vented) enclosure.
Drive
X Y
Z
Recommended
Size Above/Below
Either
Side
Between
airflow
mm in mm in mm in CFM
(ft
3
/min)
1 50
1.97
50
1.97
33
1.30
11
2 75
2.95
50
1.97
46
1.81
11
3 100
3.94 50
1.97 52
2.05
26
Note: Dimension Z assumes that the drives are mounted side-by-side with no
clearance.
Typical drive heat losses are 3% of operating load conditions.
Above are guidelines only and the operating ambient temperature of the drive
MUST be maintained at all times.
4. P
OWER
W
IRING
4.1. G
ROUNDING THE
D
RIVE
This manual is intended as a guide for proper
installation. ERIKS Industrial Services Ltd cannot
assume responsibility for the compliance or the non-
compliance to any code, national, local or otherwise,
for the proper installation of this drive or associated
equipment. A hazard of personal injury and/or
equipment exists if codes are ignored during
installation.
This drive contains high voltage capacitors that take
time to discharge after removal of main supply.
Before working on the drive, ensure isolation of main
supply from line inputs. Wait ten (10) minutes for
capacitors to discharge to safe voltage levels. Failure
to observe this precaution could result in severe
bodily injury or loss of life.
Only qualified electrical personnel familiar with the
construction and operation of this equipment and the
hazards involved should install, adjust, operate, or
service this equipment. Read and understand this
manual and other applicable manuals in their entirety
before proceeding. Failure to observe this precaution
could result in severe bodily injury or loss of life.
Use the dedicated ground terminal to ground the
drive. Do not use mounting screws/bolts or chassis
screws for grounding
4.1.1. G
ROUNDING
G
UIDELINES
The ground terminal of each Fenner drive should be
individually connected DIRECTLY to the site ground busbar.
Fenner drive ground connections should not loop from one
drive to another, or to, or from any other equipment. Ground
loop impedance must confirm to local industrial safety
regulations. To meet UL regulations, UL approved ring crimp
terminals should be used for all ground wiring connections.
The drive Safety Ground must be connected to system
ground. Ground impedance must conform to the requirements
of national and local industrial safety regulations and/or
electrical codes. The integrity of all ground connections should
be checked periodically.
Ground Fault Monitoring
If a system ground fault monitor is to be used, only Type B
devices should be used to avoid nuisance tripping.
Drives with an EMC filter have an inherently higher leakage
current to Ground (Earth). For applications where tripping
occurs the EMC filter can be disconnected by removing the
EMC screw on the side of the product.
The Fenner QD product range has input supply voltage
surge suppression components fitted to protect the drive
from line voltage transients, typically originating from
lightening strikes or switching of high power equipment
on the same supply.
When carrying out a HiPot (Flash) test on an installation in
which the drive is built, the voltage surge suppression
components may cause the test to fail. To accommodate
this type of system HiPot test, the voltage surge
suppression components can be disconnected by
removing the VAR screw. After completing the HiPot test,
the screw should be replaced and the HiPot test repeated.
The test should then fail, indicating that the voltage surge
suppression components are once again in circuit.
Safety Ground
This is the safety ground for the drive that is required by
code. One of these points must be connected to adjacent
building steel (girder, joist), a floor ground rod, or bus bar.
Grounding points must comply with national and local
industrial safety regulations and/or electrical codes.
Motor Ground
The motor ground must be connected to one of the
ground terminals on the drive.
Shield Termination (Cable Screen)
The safety ground terminal provides a grounding point for the
motor cable shield. The motor cable shield connected to this
terminal (drive end) should also be connected to the motor
frame (motor end). Use a shield terminating or EMI clamp to
connect the shield to the safety ground terminal. When shielded
cable is used for control and signal wiring, the shield should be
grounded at the source end only, not at the drive end.
4.2. W
IRING
P
RECAUTIONS
Connect drive according to section 4.3 Connection Diagram,
ensuring that motor terminal box connections are correct.
There are two connections in general: Star and Delta. It is
essential to ensure that the motor is connected in accordance
with the voltage at which it will be operated. For more
information, refer to section 4.5 Motor Terminal Box
Connections. For recommended cabling and wiring sizing,
refer to section 10.2 Rating tables. It is recommended that the
power cabling should be 3-core or 4-core PVC-insulated
screened cable, laid in accordance with local industrial
regulations and codes of practice.
NOTE
Fenner QDE User Guide 9/5/08 9:23 AM Page 7