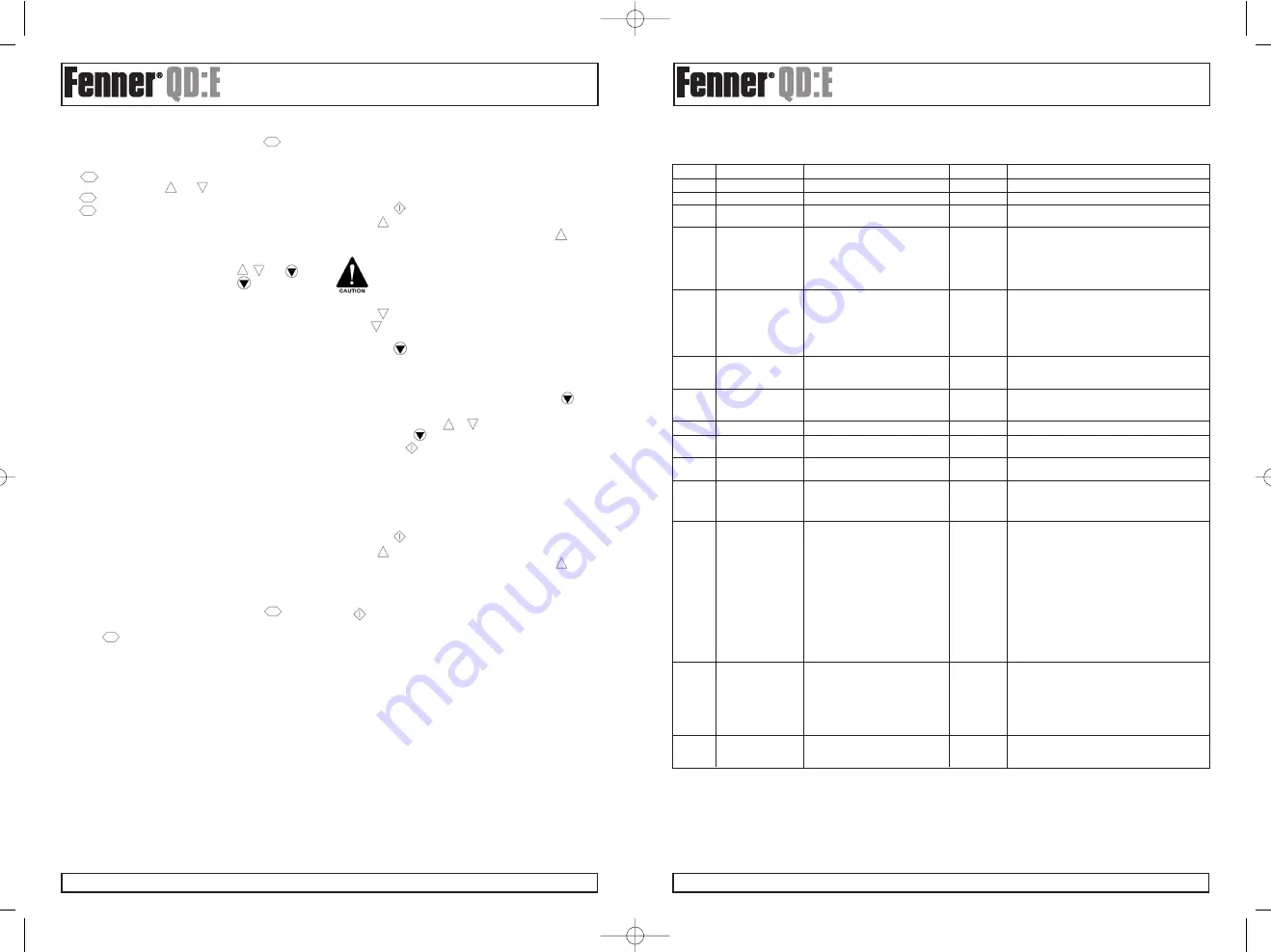
Installation & Operating Instructions
ııııııııııııııııııııııııııııııııııııııııııııııııııııııııııııııııııııııııııııııııııııııııııııııııııııııııııııııııııııııııııııııııııııııııııııııııııııııııııııııııııııııııııııııııııııııııııııııııııııııııııııııııııııııııııııııııııııı
Page 11
www.fptgroup.com
Fenner is a registered trademark of J.H. Fenner & Co. Limited
ııııııııııııııııııııııııııııııııııııııııııııııııııııııııııııııııııııııııııııııııııııııııııııııııııııııııııııııııııııııııııııııııııııııııııııııııııııııııııııııııııııııııııııııııııııııııııııııııııııııııııııııııııııııııııııııııııııı
Page 10
www.fptgroup.com
Fenner is a registered trademark of J.H. Fenner & Co. Limited
Installation & Operating Instructions
6.1.1. C
HANGING
P
ARAMETERS
To change a parameter value press and hold the key for
>1s whilst the drive displays STOP. The display changes to
P-01, indicating parameter 01. Press and release the
key to display the value of this parameter. Change to the
required value using the and keys. Press and release
the key once more to store the change. Press and hold
the key for >1s to return to real-time mode. The display
shows STOP if the drive is stopped or the real-time
information (e.g. speed) if the drive is running.
6.1.2. R
ESET
F
ACTORY
D
EFAULT
S
ETTINGS
To reset factory default parameters, press , and for
>2s. The display shows P-dEF. Press the button to
acknowledge and reset the drive.
6.2. T
ERMINAL
C
ONTROL
When delivered, the Fenner drive is in the factory default
state, meaning that it is set to operate in terminal control
mode and all parameters (P-xx) have the default values as
indicated in section 7 Parameters.
1. Connect motor to drive, checking star/delta connection for
the voltage rating
2. Enter motor data from motor nameplate, P-07 = motor
rated voltage, P-08 = motor rated current, P-09 = motor
rated frequency.
3. Connect a control switch between the control terminals 1
and 2 ensuring that the contact is open (drive disabled).
4. Connect a potentiometer (1k
Ω
min to 10 k
Ω
max) between
terminals 5 and 7, and the wiper to terminal 6.
5. With the potentiometer set to zero, switch on the supply
to the drive. The display will show STOP.
6. Close the control switch, terminals 1-2. The drive is now
‘enabled’ and the output frequency/speed are controlled by
the potentiometer. The display shows zero speed in Hz (H
0.0) with the potentiometer turned to minimum.
7. Turn the potentiometer to maximum. The motor will
accelerate to 50Hz (the default value of P-01) under the
control of the accelerating ramp time P-03. The display
shows 50Hz (H 50.0) at max speed.
8. To display motor current (A), briefly press the
(Navigate) key.
9. Press again to return to speed display.
10. To stop the motor, either turn the potentiometer back to
zero or disable the drive by opening the control switch
(terminals 1-2).
If the enable/disable switch is opened the drive will decelerate
to stop at which time the display will show STOP. If the
potentiometer is turned to zero with the enable/disable closed
the display will show H 0.0 (0.0Hz), if left like this for 20
seconds the drive will go into standby mode, display shows
Stndby, waiting for a speed reference signal.
6.3. K
EYPAD
C
ONTROL
To allow the Fenner drive to be controlled from the keypad in a
forward direction only, set P-12 =1:
1. Connect Motor as for terminal control above.
2. Enable the drive by closing the switch between control
terminals 1 & 2. The display will show STOP.
3. Press the key. The display shows H 0.0.
4. Press to increase speed.
5. The drive will run forward, increasing speed until is
released.
The rate of acceleration is controlled by the setting of
P-03, check this before starting.
6. Press to decrease speed. The drive will decrease speed
until is released. The rate of deceleration is limited by
the setting in P-04
7. Press the key. The drive will decelerate to rest at the
rate set in P-04.
8. The display will finally show STOP at which point the drive
is disabled
9. To preset a target speed prior to enable, press the key
whilst the drive is stopped. The display will show the
target speed, use the & keys to adjust as required
then press the key to return the display to STOP.
10. Pressing the key will start the drive accelerating to the
target speed.
To allow the Fenner drive to be controlled from the keypad in a
forward and reverse direction, set P-12 =2:
11. Operation is the same as when P-12=1 for start, stop and
changing speed.
12. Press the key. The display changes to H 0.0.
13. Press to increase speed
14. The drive will run forward, increasing speed until is
released. Acceleration is limited by the setting in P-03. The
maximum speed is the speed set in P-01.
15. To reverse the direction of rotation of the motor, press the
key again.
7. P
ARAMETERS
7.1. S
TANDARD PARAMETERS
Default parameter values for Horse Power rated drives are shown in brackets
Standby mode is enabled automatically when the drive is at zero speed for > 20 seconds
NOTE
Par.
Description
Range
Default
Explanation
P-01
Maximum speed
P-02 to 5*P-09 (max 500Hz)
50Hz (60Hz)
Maximum speed limit – Hz or rpm. See P-10
P-02
Minimum speed
0 to P-01 (max 500Hz)
0Hz
Minimum speed limit – Hz or rpm. See P-10
P-03
Acceleration ramp
0 to 600s
5s
Acceleration ramp time from 0 to base speed
time
(P-09) in seconds
Deceleration ramp time from base speed (P-09) to
standstill in seconds.
P-04
Deceleration ramp
0 to 600s
5s
When P-04=0, the deceleration ramp is set by P-24.
time
Setting P-04=0 also activates dynamic ramp control,
where the ramp may be extended automatically to
prevent an O-Volt trip.
If the supply is lost and P-05=0 then the drive will
0 : Ramp stop
try to continue running by reducing the speed of
P-05
Stop mode select
(brown-out ride-through)
0
the load using the load as a generator.
1 : Coast to stop
If P-05 = 2, the drive will ramp to stop using the
2 : Ramp to stop (fast stop)
P-24 decel ramp with dynamic brake control when
mains supply lost.
0: Disabled
When enabled, automatically reduces applied
P-06
Energy Optimiser
1: Enabled
0
motor voltage on light load. Minimum value is
50% of nominal.
0, 20V to 250V
230V
Rated (nameplate) voltage of the motor (Volts).
P-07
Motor rated voltage
0, 20V to 500V
400V (460V)
Value limited to 250V for low voltage drives.
Setting to zero disables voltage compensation
P-08
Motor rated current
25% -100% of drive rated current
Drive rating
Rated (nameplate) current of the motor (Amps).
P-09
Motor rated
25Hz to 500Hz
50Hz (60Hz)
Rated (nameplate) frequency of the motor.
frequency
P-10
Motor rated speed
0 to 30 000 rpm
0
When non-zero, all speed related parameters are
displayed in rpm
Size 1: 0.0 to 20.0%
Applies an adjustable boost to the Fenner drive voltage
P-11
Voltage boost
Size 2: 0.0 to 15.0%
Motor power
output at low speed to assist with starting ‘sticky’
Size 3: 0.0 to 10.0%
dependent
loads. For continuous applications at low speed use
of max output voltage.
a forced ventilated motor.
Primary Control Mode of the drive.
0. Terminal control
0.Terminal control
1. Uni-directional keypad control. Keypad START
1. Keypad control – fwd only
button does not reverse direction.
Terminal / Keypad /
2. Keypad control - fwd and rev
2. Bi-directional keypad control. Keypad START
MODBUS / PI
3. MODBUS network control with
button toggles between forward and reverse.
P-12
Drive Control
internal accel / decel ramps
0
3. Control via Modbus RTU (RS485) comms
Mode Selection
4. MODBUS network control withl
interface using the internal accel / decel ramps
accel / decel ramp adjustment
4. Control via Modbus RTU (RS485) comms
5. User PI control
nterface with accel / decel ramps updated via
6. User PI control with analog input
Modbus
1 summation
5. User PI control with external feedback signal
6. User PI control with external feedback signal and
summation with analog input 1
Previous 4 trips stored in order of occurrence, with
the most recent first.
Press UP or DOWN to step through all four.
P-13
Trip log
Last four trips stored
Read only
The most recent trip is always displayed first.
UV trip is only stored once.
Further fault event logging functions are available
through parameter group zero.
Set to “101” (default) for extended menu access.
P-14
Extended menu
Code 0 to 9 999
0
Change code in P-39 to prevent unauthorised
access
access to the Extended Parameter Set
Fenner QDE User Guide 9/5/08 9:23 AM Page 11