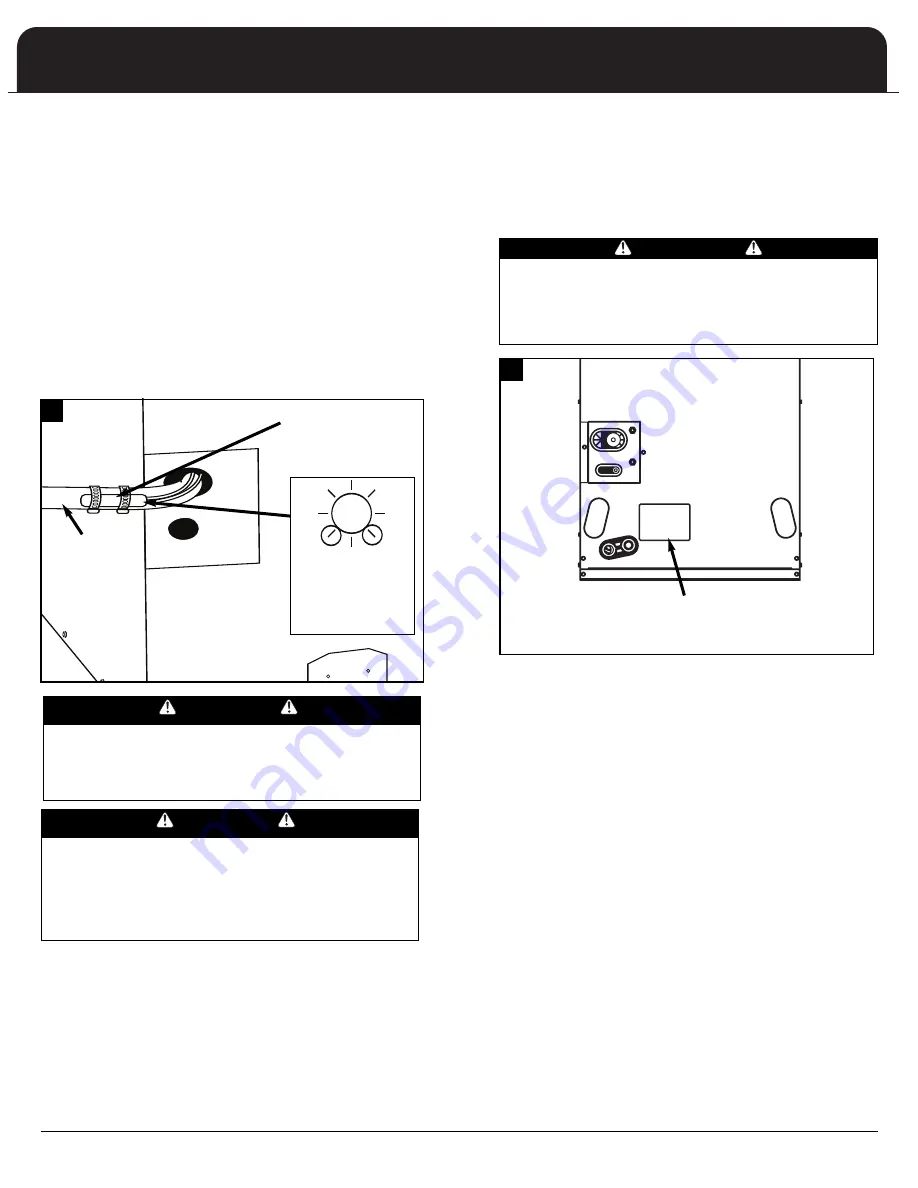
6
CAUTION
THE TXV SENSING BULB CAN BE DAMAGED BY
EXTREME HEAT FROM BRAZING. THE BULB SHOULD
BE REMOVED BEFORE PERFORMING ANY BRAZING
PROCEDURE AND NOT INSTALLED UNTIL AFTER THE
VAPOR AND LIQUID LINES ARE BRAZED AND LEAK
CHECKED.
Connect Refrigerant Piping
Use field supplied tubing of refrigerant grade. Suction tube
must be insulated. Do not use damaged, dirty, or
contaminated tubing because it may plug refrigerant flow
control device. ALWAYS evacuate the coil and field supplied
tubing before opening outdoor unit service valves.
Factory and Field-Installed Expansion Valves
1. The bulb and capillary tubing should be routed outside
of the case. Make sure the capillary tube will not contact
any sharp edges of the case. On factory installed
expansion valves, the adjustable sensing bulb is not
permanently installed onto the coils’ vapor line in order
to allow easy removal during installation.
4 o’clock
8 o’clock
Sensing bulb
attached with
clamps
Vapor line
4 o’clock
8 o’clock
Attach bulb to
vapor line at four
or eight o’clock
position
CAUTION
THE TXV VALVE CAN BE DAMAGED BY EXTREME
HEAT. PROPER PRECAUTIONS SHOULD BE TAKEN TO
AVOID OVERHEATING THE TXV VALVE AND CAUSING
DAMAGE TO THE INTERNAL COMPONENTS.
3. Attach the bulb securely with the copper strap provided.
4. Insulate the bulb thoroughly with a suitable insulation
material such as cork tape.
5. Coils with TXVs should be charged 10-12 degrees
(+ or – one degree) of sub-cooling. This supercedes any
subcooling value listed with condensing unit’s literature.
For the majority of installations no adjustment to the
TXV setting is required. However, if the measured
superheat is less than 4° or greater than 8° an
adjustment is required. The adjustment stem is at the
base of the valve under the flare nut. To increase
superheat, tighten the stem clockwise and to decrease
superheat, back-out the stem counter-clockwise. Use a
1/4
” refrigeration service wrench for this function.
NOTE:
When removing refrigerant, always use standard reclaim
procedures.
2. To assure accurate sensing and the best performance the
bulb should be placed on a horizontal section of the
vapor line at the four or eight o’clock position and at
least 6” from the coil manifold.
TXV valve can be accessed
through the valve cover-plate
on the front of the air handler.
WARNING
ALWAYS HAVE A FIRE EXTINGUISHER AVAILABLE
WHEN WORKING WITH AN OPEN FLAME.
ALWAYS USE SAFETY GLASSES, PROTECTIVE
CLOTHING, AND WORK GLOVES.
11
7
11
6