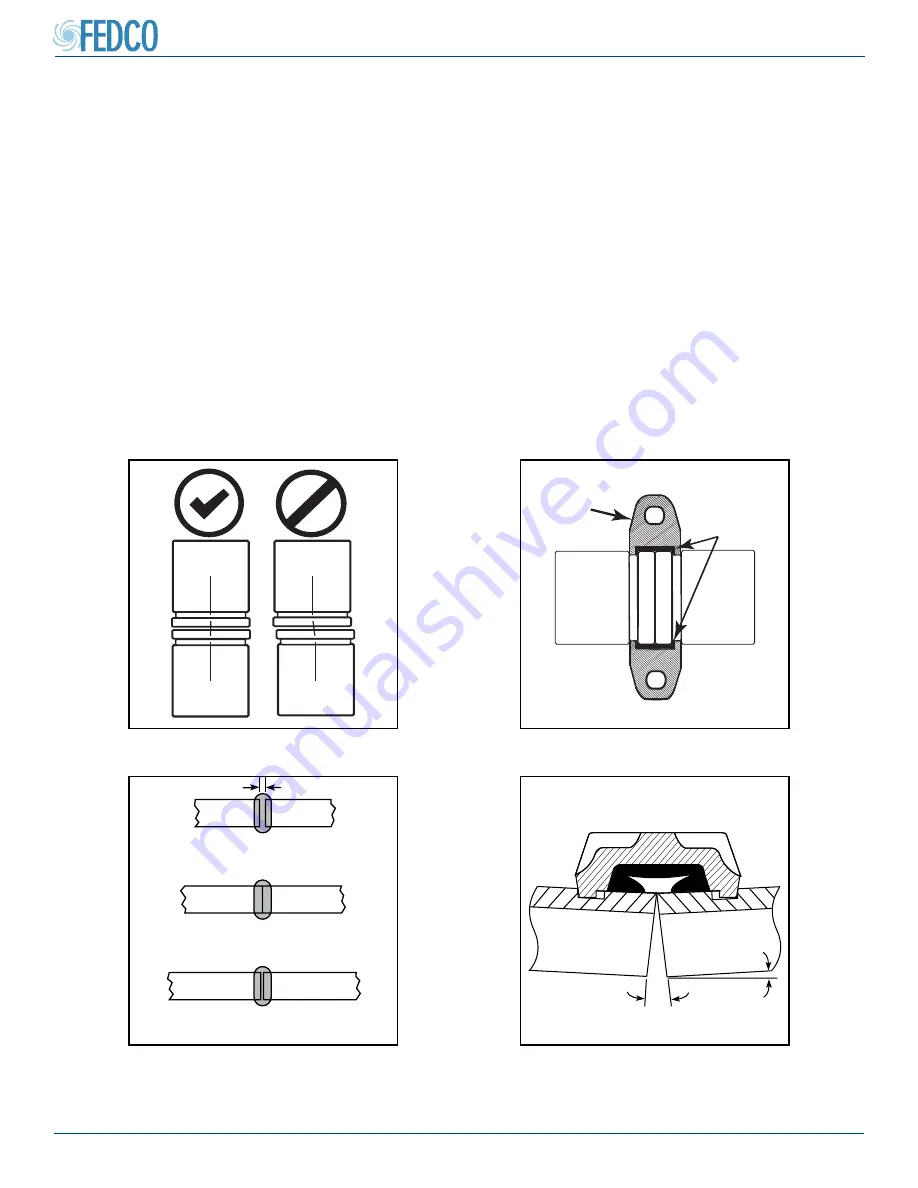
HPB
TM
Series
© Copyright 2018 Fluid Equipment Development Company | www.fedco-usa.com
-
14
-
Installation Procedures Continued
Booster Piping Connections
Piping Alignment
•
Accurate alignment and support of all piping connected to the booster is critical.
•
Any movement occurring at the inlet or discharge booster connections may cause booster
misalignment and stress over time.
•
Do not force any misaligned pipes to connect to the booster discharge or inlet.
Pipe Couplings
•
Follow all manufacturer installation and torque specifications.
•
Align all piping carefully before installing couplings.
• Make sure all seals seat correctly inside the coupling.
• If piping or seals are not aligned correctly, leaking may occur under pressure.
•
Provide for expansion or contraction of piping. Always consider best setting for pipe end gaps
for handling angular deflection and combinations of expansion and contraction. Separation
and deflection recommendations are specified on the following page.
YES
NO
Figure 12 - Proper Piping Alignment
GROOVED
COUPLING
COUPLING
SEAL
Figure 13 - Typical Grooved Coupling
FULLY APART
Expansion Only
PARTIALLY GAPPED
Expansion and Contraction
FULLY BUTTED
Contraction Only
Figure 14 - Pipe End Separation
Θ
Θ
Figure 15 -
Angular Deflections