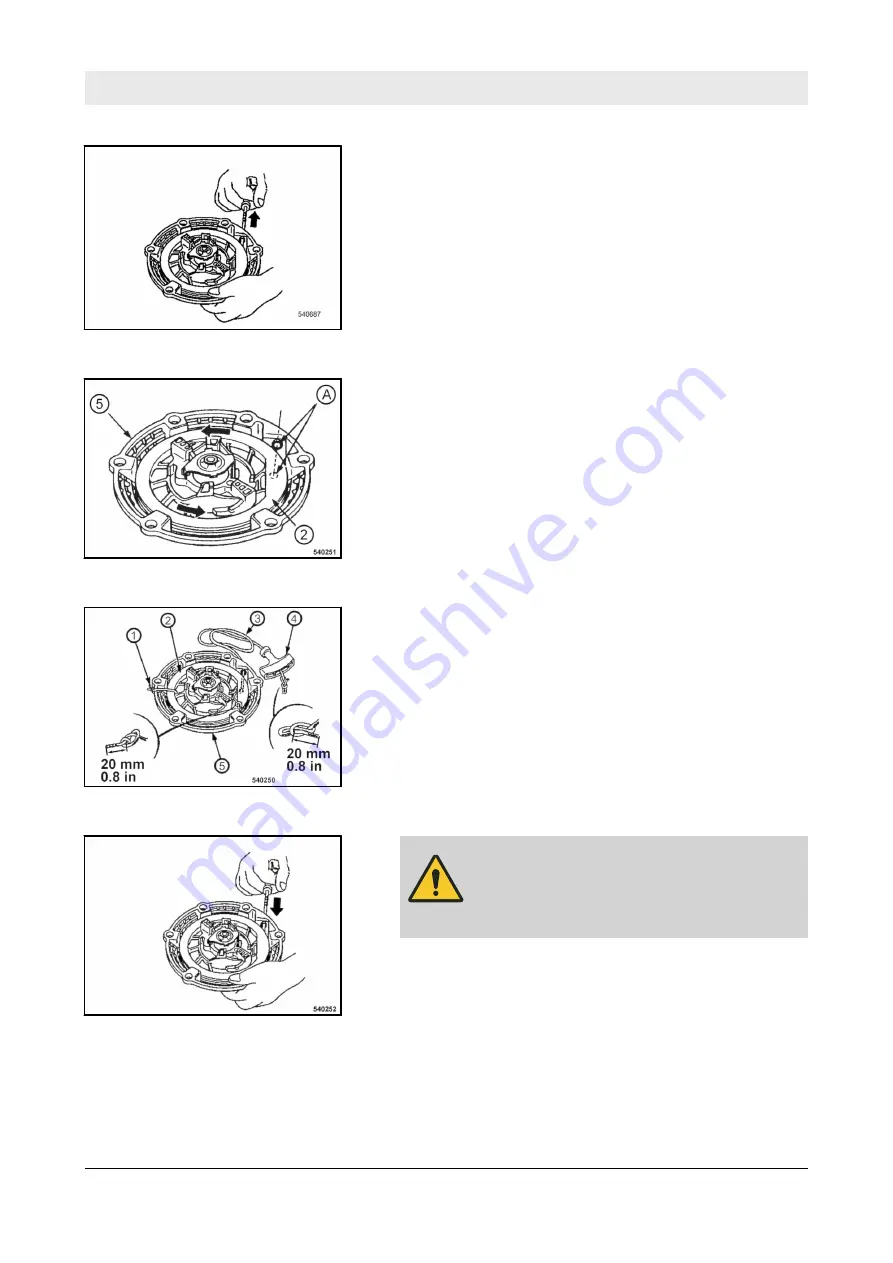
4.
Pull the starter rope with the starter handle out completely.
5.
If the starter rope has been torn or the coil has recoiled com-
pletely:
n
Before assembling the rope, turn the coil (2) 5 revolutions
in anti-clockwise direction and align the rope openings in
coil and housing (5) to one another (A).
6.
Secure the coil against winding up. For this purpose tie the
coil (2) to the housing (5) with a cable strap (1).
7.
Untie the knots of the starter rope at both ends and remove
the old starter rope.
8.
Thread in the new starter rope (3) and fix it with knots on
both ends.
9.
CAUTION!
Danger of injury caused by the starter
handle hitting against your body!
–
Do not let the starter handle hit back.
Remove the fixing of the coil and run the starter handle
slowly back to initial position.
10.
Pull the starter handle to check the function and light move-
ment of the recoil starter.
Fig. 88
Fig. 89
Fig. 90
Fig. 91
Maintenance – Annually
DFP9
87
Summary of Contents for Dynapac DFP9
Page 6: ...Table of contents DFP9 6 ...
Page 7: ...1 Introduction Introduction DFP9 7 ...
Page 11: ...2 Technical data Technical data DFP9 11 ...
Page 15: ...3 Concerning your safety Concerning your safety DFP9 15 ...
Page 39: ...4 Indicators and control elements Indicators and control elements DFP9 39 ...
Page 45: ...5 Checks prior to start up Checks prior to start up DFP9 45 ...
Page 52: ...Checks prior to start up Checking the water level topping up DFP9 52 ...
Page 53: ...6 Operation Operation DFP9 53 ...
Page 63: ...7 Loading transporting the machine Loading transporting the machine DFP9 63 ...
Page 67: ...8 Maintenance Maintenance DFP9 67 ...
Page 97: ...9 Troubleshooting Troubleshooting DFP9 97 ...
Page 103: ...10 Disposal Disposal DFP9 103 ...
Page 105: ......
Page 106: ......