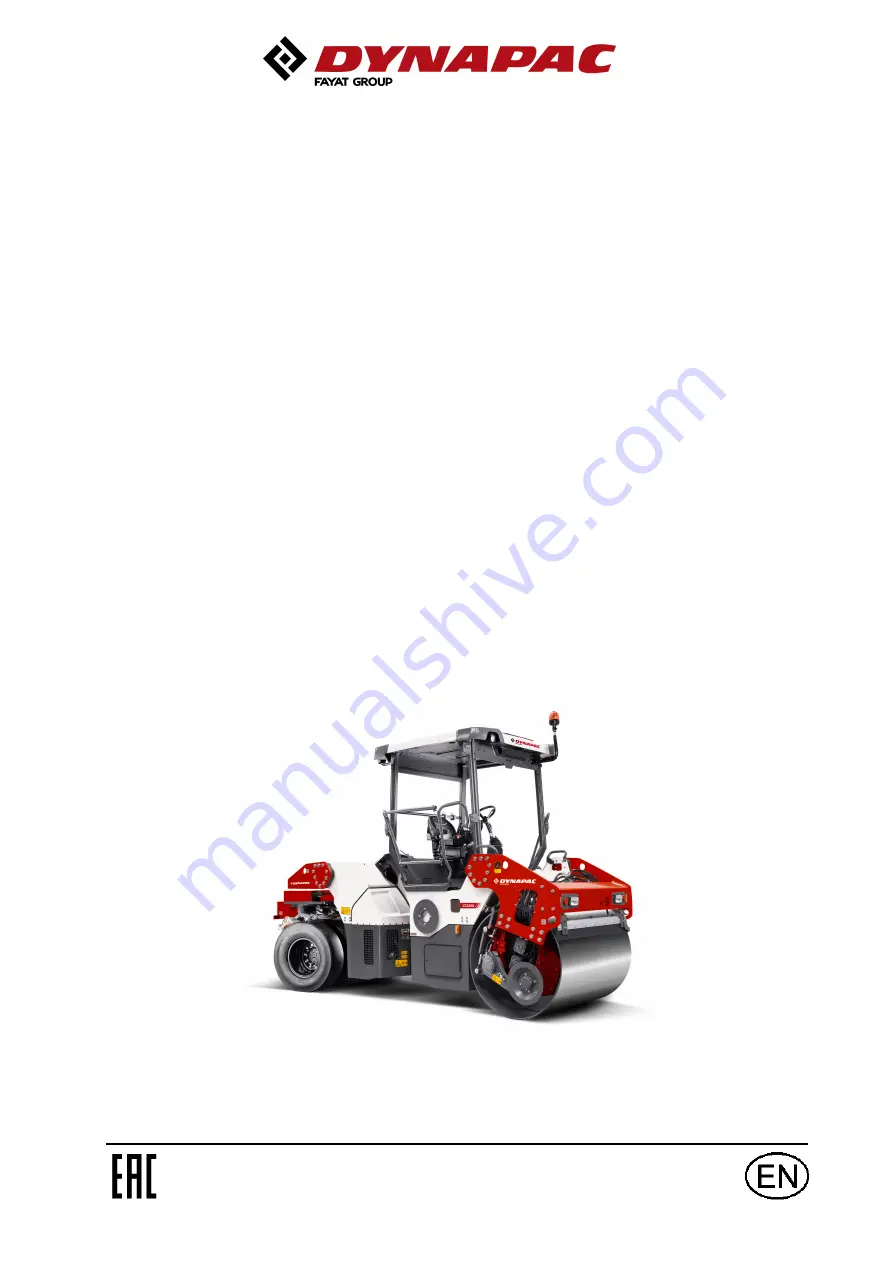
Instruction manual
Instruction manual
Operating & Maintenance
Operating & Maintenance
4812159901_D.pdf
4812159901_D.pdf
Vibratory roller
Vibratory roller
CC234C/334C
CC234C/334C
CC2300C/3300C
CC2300C/3300C
Engine
Engine
Cummins QSB 3.3 (IIIA/T3)
Cummins QSB 3.3 (IIIA/T3)
Deutz TCD 3.6 L04 (IIIB/T4i), (IIIB/T4f)
Deutz TCD 3.6 L04 (IIIB/T4i), (IIIB/T4f)
Deutz TCD 3.6 L04 (stage V)
Deutz TCD 3.6 L04 (stage V)
Serial number
Serial number
10000314xxA010759 -
10000314xxA010759 -
10000318xxA011450 -
10000318xxA011450 -
10000339xxA011447 - 16402
10000339xxA011447 - 16402
10000343xxA013149 - 20105
10000343xxA013149 - 20105
10000426xxA......... -
10000426xxA......... -
10000430xxA034417 -
10000430xxA034417 -
10000459xxA030825 -
10000459xxA030825 -
10000463xxA035662 -
10000463xxA035662 -
Translation of original instruction
Translation of original instruction
Reservation for changes
Reservation for changes
Printed in Sweden
Printed in Sweden
Summary of Contents for DYNAPAC CC234C
Page 2: ......
Page 13: ...4812159901_D pdf 2023 01 25 1...
Page 14: ...4812159901_D pdf 2023 01 25 2...
Page 18: ...Introduction 4812159901_D pdf 2023 01 25 6...
Page 28: ...Special instructions 4812159901_D pdf 2023 01 25 16...
Page 74: ...Machine description 4812159901_D pdf 2023 01 25 62...
Page 94: ...Operation 4812159901_D pdf 2023 01 25 82...
Page 108: ...Preventive maintenance 4812159901_D pdf 2023 01 25 96...
Page 128: ...Maintenance 10h 4812159901_D pdf 2023 01 25 116...
Page 132: ...Maintenance 50h 4812159901_D pdf 2023 01 25 120...
Page 146: ...Maintenance measures 500 h 4812159901_D pdf 2023 01 25 134...
Page 173: ......
Page 174: ...Dynapac Compaction Equipment AB Box 504 SE 371 23 Karlskrona Sweden www dynapac com...