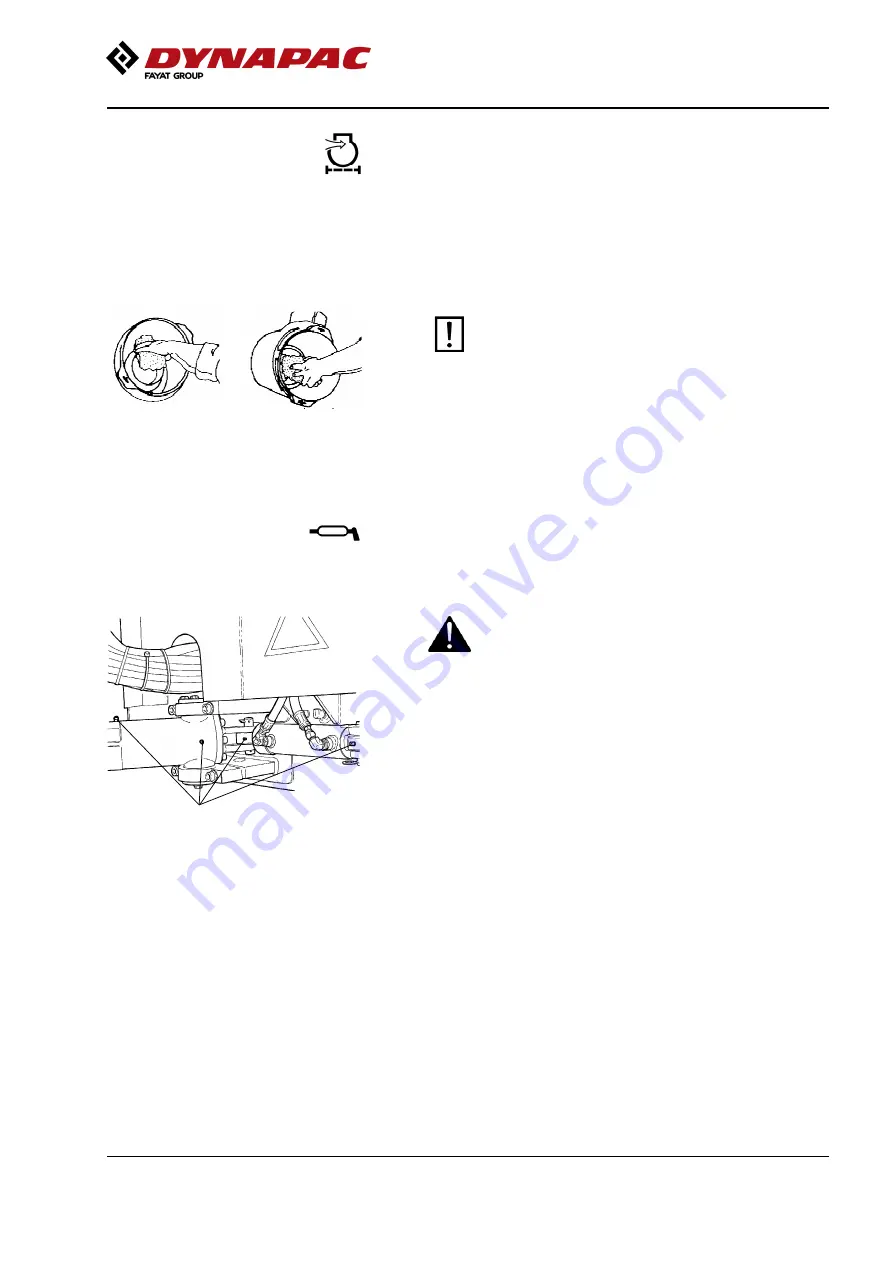
Maintenance - 50h
4812162101_D.pdf
2021-12-14
Air cleaner
- Cleaning
Wipe clean the inside of the cover (2) and the filter
housing (5). See the previous illustration.
Wipe clean on both sides of the outlet
pipe.
Outer edge of outlet
pipe.
Inner edge of
outlet pipe.
Wipe also both surfaces for the outlet pipe; see
adjacent figure.
Check that the hose clamps between the filter
housing and the suction hose are tight and that
the hoses are intact. Inspect the entire hose
system, all the way to the engine.
Check that the hose clamps between the filter
housing and the suction hose are tight and that
the hoses are intact. Inspect the entire hose
system, all the way to the engine.
Steering cylinder and steering joint -
Lubrication
Fig. Main filter
1. Grease nipples
1
Do not allow anyone to remain in the vicinity of the
steering joint when the engine is running. Danger
of crush injury when the steering is operated.
Activate the parking brake before lubricating.
Do not allow anyone to remain in the vicinity of the
steering joint when the engine is running. Danger
of crush injury when the steering is operated.
Activate the parking brake before lubricating.
Turn the steering wheel fully to the left. All four grease
nipples (1) can now be accessed from the right side of
the machine.
Wipe the grease nipples (1). Grease each nipple with
five strokes of the hand-operated grease gun. Make
sure that grease penetrates into the bearing. If grease
does not penetrate the bearings, it may be necessary
to relieve the articulation joint with a jack while
repeating the greasing process.
87
Summary of Contents for DYNAPAC CC1300C
Page 2: ......
Page 10: ...e 4812162101_D pdf 2021 12 14...
Page 14: ...Introduction 4812162101_D pdf 2021 12 14 4...
Page 22: ...Special instructions 4812162101_D pdf 2021 12 14 12...
Page 30: ...Technical specifications 4812162101_D pdf 2021 12 14 20...
Page 34: ...Machine description 4812162101_D pdf 2021 12 14 24...
Page 48: ...Machine description 4812162101_D pdf 2021 12 14 38...
Page 72: ...Operating instructions Summary 4812162101_D pdf 2021 12 14 62...
Page 83: ...Maintenance Maintenance schedule 4812162101_D pdf 2021 12 14 Service Checklist 73...
Page 84: ...Maintenance Maintenance schedule 4812162101_D pdf 2021 12 14 74...
Page 102: ...Maintenance measures 250 h 4812162101_D pdf 2021 12 14 92...
Page 120: ...Maintenance 1000h 4812162101_D pdf 2021 12 14 110...
Page 134: ...Dynapac Compaction Equipment AB Box 504 SE 371 23 Karlskrona Sweden www dynapac com...