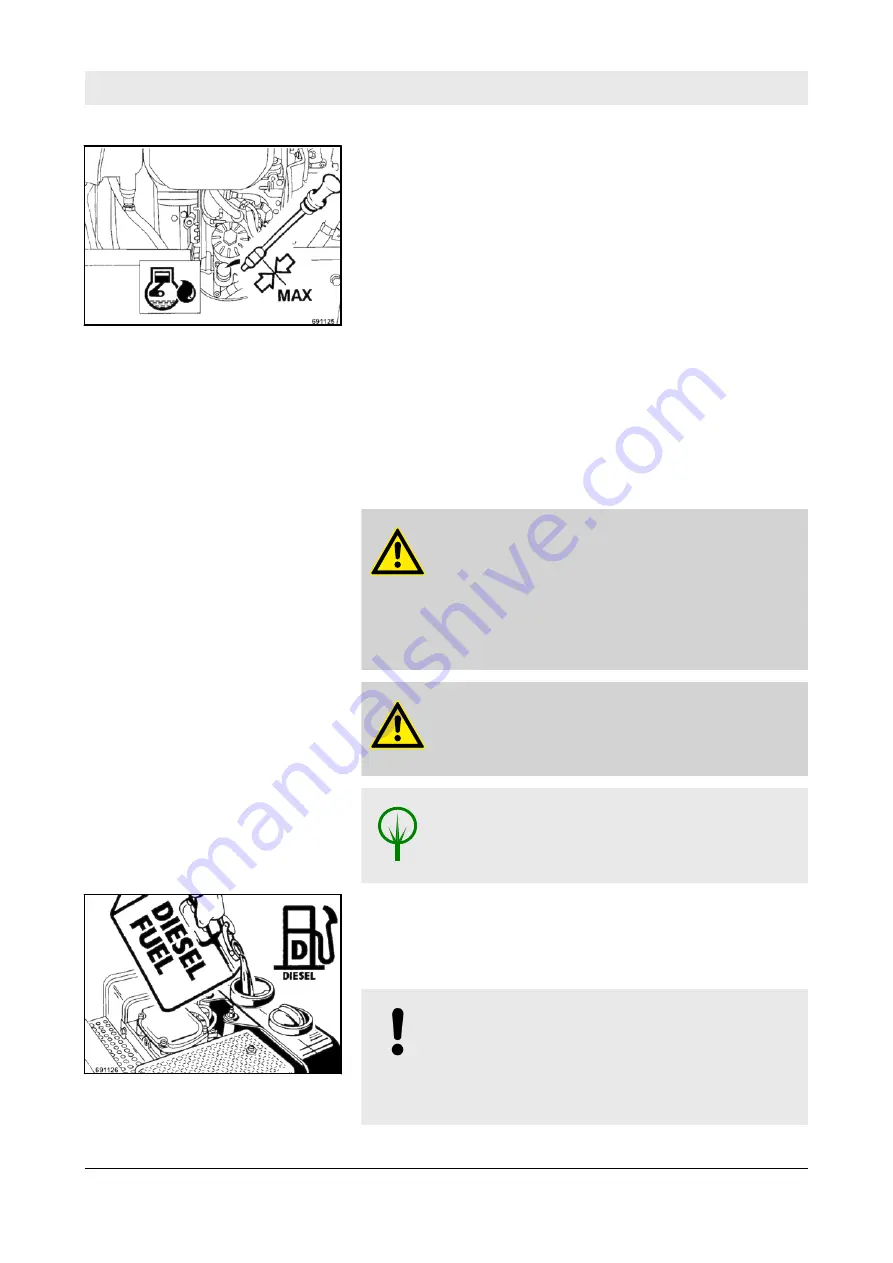
Shut down the engine.
Open the rear rubber cover.
Fig. 44 out, wipe it off with a lint-free,
clean cloth and reinsert it until it bottoms.
Pull out the oil dipstick again and read the oil level.
The oil level should reach the upper mark on the dipstick. If
the oil level is too low top up oil immediately.
After a running time of approx. one minute shut the engine
down, wait until all oil has run back into the oil sump, check
the oil level.
6.6.3 Check the fuel level
WARNING!
Fire hazard!
When working on the fuel system do not use open
fire, do not smoke, do not spill any fuel.
Do not refuel in closed rooms.
Shut down the engine.
WARNING!
Health hazard!
Do not inhale any fuel fumes.
ENVIRONMENT!
Catch running out fuel, do not let it seep into the
ground.
Clean the area around the filler opening.
Open the filler cap on the fuel tank and check the fuel level
visually.
NOTICE!
Contaminated fuel can cause malfunction or even
damage of the engine.
For quality and quantity of fuel refer to the "table of
fuels and lubricants".
Fig. 44
Fig. 45
Maintenance – Daily maintenance
BPR 70/70 D
57
Go to
Discount-Equipment.com
to
order your parts