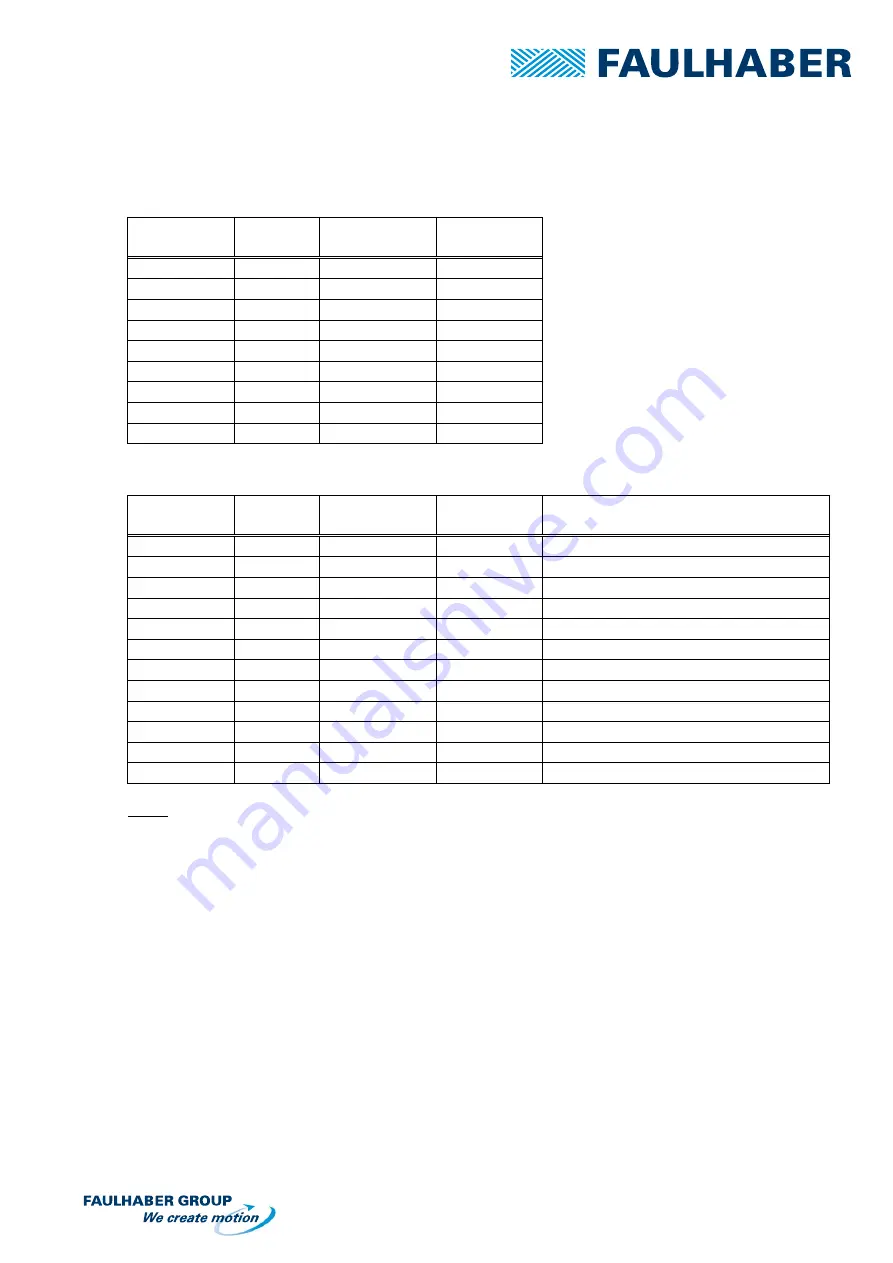
User manual AD CM M
Page 7 of 20
1.4
Suitable PRECISTEP Motors
The driver of the series AD CM M_S is specifically suitable for motors with windings designed for constant
current control.
Motor Type
Winding
Current setting
(switch position)
Voltage setting
(recommended)
AM0820 V-3-18 3
16
V
AM1020 A-0,25-8 5
12
V
ADM1220(S) V2
6
10
V
ADM1220(S) V3
4
15.5
V
AM1524 A-0,25-12,5 5
18.5
V
AM1524 A-0,45-3,6 9
10
V
AM1524 V-6-35 3
27
V
AM2224(-R3) AV-4,8
10
14.5
V
AM2224(-R3) AV-18
5
27
V
For other stepper motors, the current control mode is possible but not optimal.
Motor Type
Winding
Current setting
(switch position)
Voltage setting
(recommended)
Notes
ADM0620
V3
1
10 V
33% torque reduction
ADM0620
V6
-
-
Definitely not recommended for current mode
AM0820
V-5-56
1
17 V
38% torque reduction
AM0820
A-0,225-7
4
10 V
12% torque reduction
AM1020
V-3-16
3
14.5 V
17% torque reduction
AM1020
V-6-65
1
19.5 V
45% torque reduction
AM1020
V-12-250
-
-
Definitely not recommended for current mode
ADM1220(S)
V6
1
14.5 V
45% torque reduction
ADM1220(S)
V12
-
-
Definitely not recommended for current mode
AM1524
V-12-150
-
-
Definitely not recommended for current mode
AM2224(-R3)
AV-0,9
15 (max)
10 V
35% torque reduction
AM2224(-R3)
AV-12-75
-
-
Definitely not recommended for current mode
Notes
•
The settings of the second table use a lower current than the nominal current recommended in the
datasheet (that is why torque is reduced in most cases). It is possible to set a higher current but the
temperature may rise very quickly causing irreversible damages to the motor.
•
It is often possible to set the current to a close matching value by using the boost function. The idea is
then to set the current to a lower value and increase it up to 135% by using the PIN7 of the COMMAND
connector (see section 2.3.1 for more information). However, this solution is not direct and requires
controlling externally the boost function.
•
Also, when the current setting is not appropriated to the winding, please note that some motors may
offer a reduced operational speed because of their high back-EMF.
•
Generally speaking, the higher the voltage of the supply is, the more torque the motor will develop at
high speed.