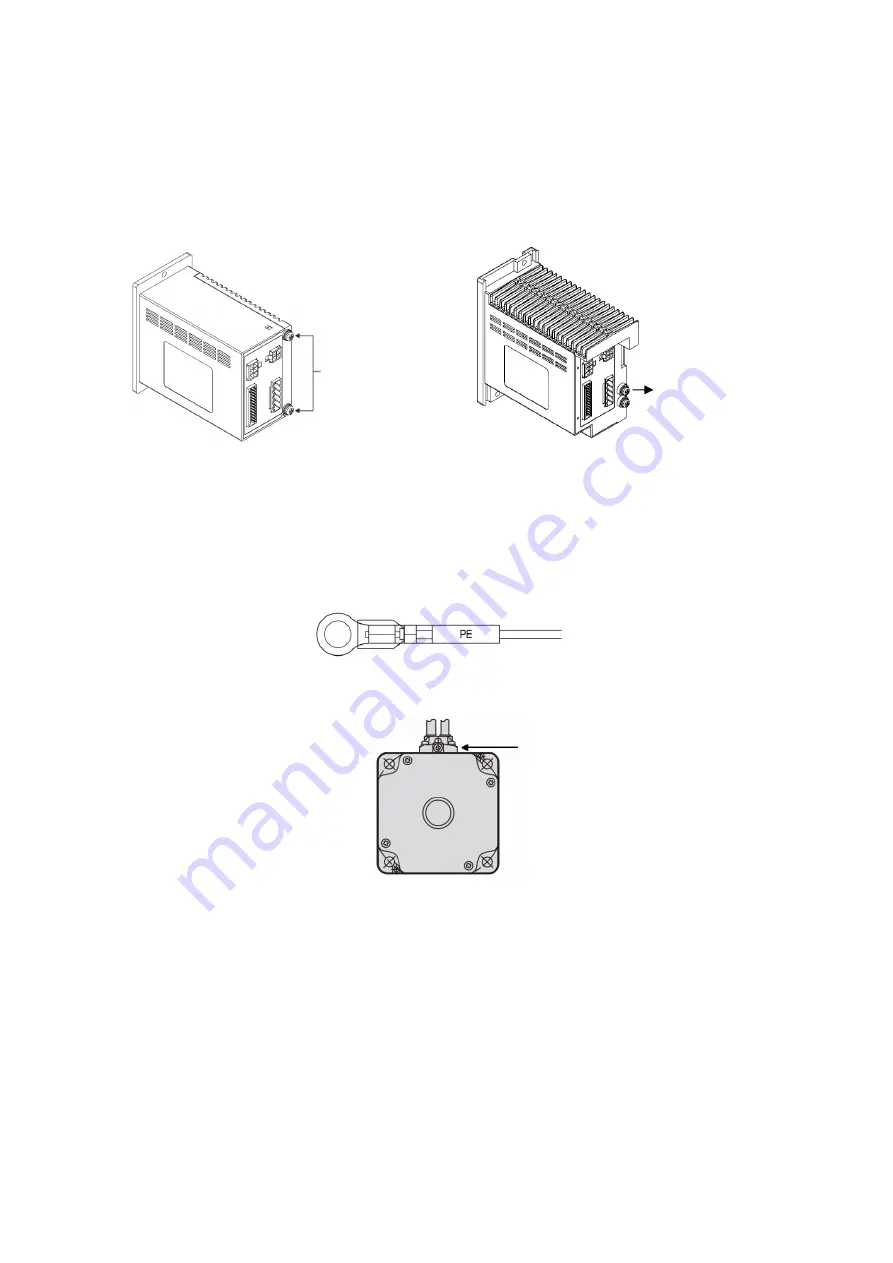
-49-
•
Ground connection of drive
The drive has two ground terminals. Ground one of terminals to near drive. You can connect any
ground terminal. The ground termina without ground is reserved terminal.
Connect the motor to
ground or use the motor as required. Do not use the ground wire as a welder or a power unit.
•
Ground connection of motor
Ground terminal
- Use crimp style terminal : Ring crimp style terminal with insulation
- Teminal screw size : M4
Motor ground connection
200W, 400W motor can ground directly on the motor.
7.3.4 Connecting the I/O signals
I/O signal connects to CN4.
•
Connecting the lead wire
- Lead wire size : AWG26 ~ 20
(0.14 ~ 0.5 𝑚𝑚
2
)
- Length of lead wire stripping : 8mm
- Connect with crimp style terminal
Direct ground
connect to the motor
Ground one of
terminals to drive
Ground one of
terminals to drive
Drive of 30W, 60W, 120W
Drive of 200W, 400W
Summary of Contents for Ezi-SPEED ESD-120-C
Page 1: ......
Page 9: ...9 2 Characteristics 2 1 Part number...
Page 15: ...15 3 2 Dimensions 30W 60W 120W Drive 200W 400W Drive...
Page 18: ...18 ESM 90 H 120 ESM 104 H 200 ESM 104 H 400...
Page 19: ...19 4 3 Characteristics of motor torque 30W 60W 120W...
Page 20: ...20 200W 400W...
Page 63: ...63 8 2 Setting and 7 segments display 1 Monitor mode...
Page 64: ...64 2 Input Output setting mode...
Page 65: ...65 3 Parameter setting mode 1page...
Page 66: ...66 3 Parameter setting mode 2page...
Page 67: ...67 3 Parameter setting mode 3page...
Page 68: ...68 3 Parameter setting mode 4page...
Page 69: ...69 4 NVM saving mode...