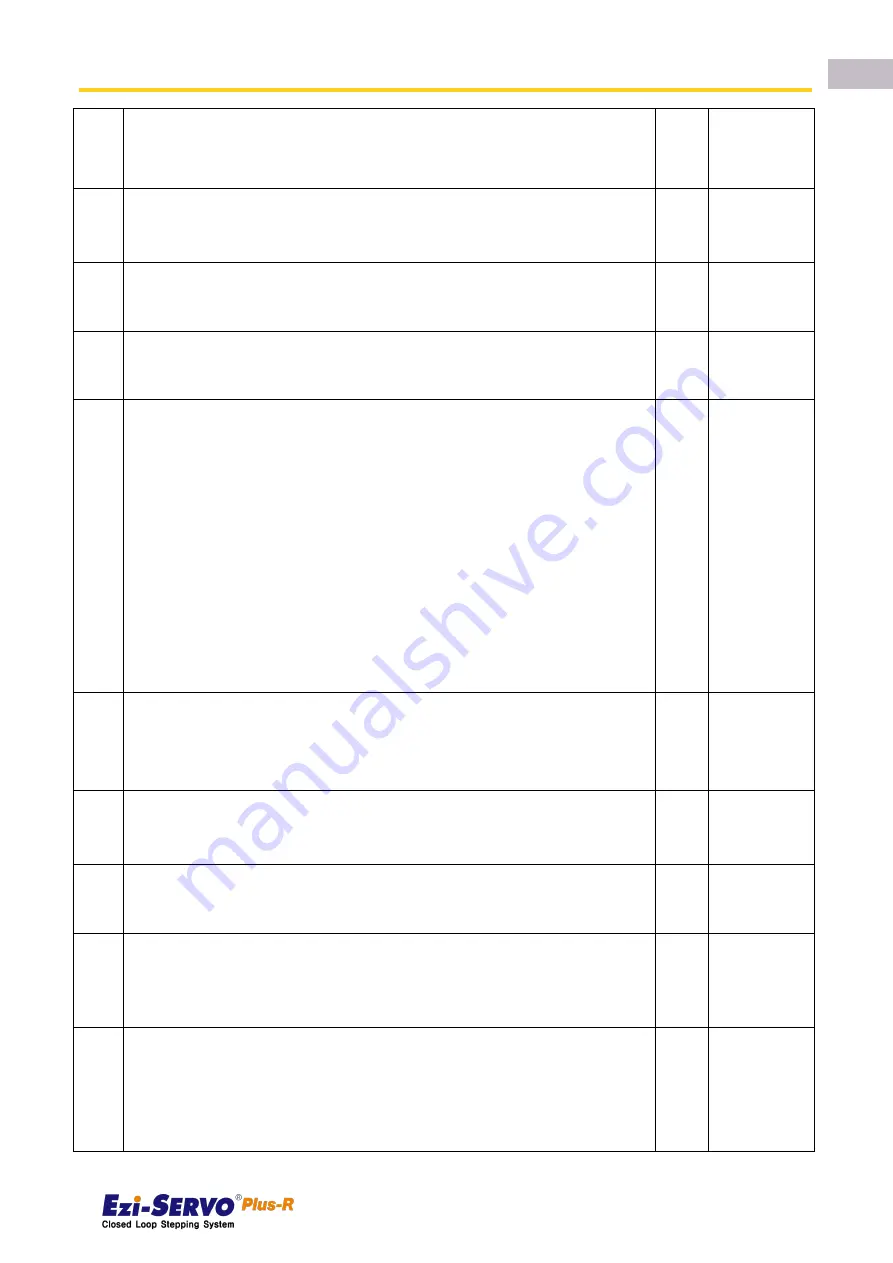
10.3. Parameter Description
97
www.fastech.co.kr
16
Limit Sensor Logic :
Sets the signal level so that the motor can recognize limit sensor’s input to ON.
♦ 0 : 0 V (Active low) ♦ 1 : 24V (Active high)
0
17
Org Speed :
In case of origin return command, this modes sets the operation speed until the motor
senses the origin sensor to [pps] unit.
[pps]
5,000
18
Org Search Speed :
In case of origin return command, The low operation speed for precise origin return
after the motor senses the origin sensor is set to [pps] unit by this mode.
[pps]
1,000
19
Org Acc Dec Time :
In case of origin return command, the acceleration/deceleration section time of the
operation start/stop segment is set to [msec] unit by this mode.
[msec]
50
20
Org Method :
The user can select origin return command types.
♦ 0 : The motor moves up to the origin sensor spot by ‘Org Speed’ and then
executes precise origin return at the low value of ‘Org Search Speed’.
♦ 1 : The motor moves up to the origin sensor spot by ‘Org Speed’ and then
executes Z-pulse origin return at the lo
w value of ‘Org Search Speed’.
♦ 2 : The motor moves up to the limit sensor spot by ‘Org Speed’ and then
immediately stops.
♦ 3 : The motor moves up to the wall by ‘Org Torque Ratio’ and then immediately
stops.
♦ 4 : The motor moves up to the wall by ‘Org Torque Ratio’ and then executes Z-
pulse origin return at the low value of ‘Org Search Speed’.
♦ 5 : To set origin in current mechanical position..
For more information, refer to
‘7.4 Origin Return’
.
0
21
Org Dir :
In case of origin return, this mode sets the revolution direction of the motor.
♦ 0 : moves the motor clockwise.
♦ 1 : moves the motor counterclockwise.
0
22
Org Offset :
After origin return is completed, the motor moves additionally as this setting value and
then stops. ‘Command Pos/Actual Pos’ is set to ‘0’.
[pulse]
0
23
Org Position Set :
After origin return is completed, ‘Command Pos/Actual Pos’value is set to this setting
value.
[pulse]
0
24
Org Sensor Logic :
Sets the origin sensor signal level so that the motor can recognize origin
sensor’s
input to ON.
♦ 0 : 0 V (low) ♦ 1 : 24V (high)
0
25
Position Loop Gain :
After the motor stops, this mode controls the motor’s response by a load attached to
the motor. The user can control this value by the motor’s load and so get the motor’s
performance that responds fast and stably. Set this mode as follows.
1)
Set the value to ‘0’.
2)
Increase the value until the motor’s response is stabilized.
4
Summary of Contents for Ezi-servo plus-R
Page 1: ...www fastech co kr User Manual Text Ver 3...
Page 10: ...2 1 Driver Specification www fastech co kr 10 2 1 2 Ezi SERVO Plus R MINI...
Page 11: ...2 1 Driver Specification 11 www fastech co kr 2 1 3 Ezi SERVO ALL 28 series...
Page 12: ...2 1 Driver Specification www fastech co kr 12 2 1 4 Ezi SERVO ALL 42 56 series...
Page 13: ...2 1 Driver Specification 13 www fastech co kr 2 1 5 Ezi SERVO ALL 60 60 ABS series...
Page 17: ...3 2 Motor Dimension 17 www fastech co kr 3 2 Motor Dimension...
Page 18: ...3 2 Motor Dimension www fastech co kr 18...
Page 19: ...3 2 Motor Dimension 19 www fastech co kr...
Page 20: ...3 3 Motor Torque www fastech co kr 20 3 3 Motor Torque 3 3 1 Ezi SERVO Plus R...
Page 23: ...4 1 Part Numbering 23 www fastech co kr 3 Ezi SERVO ALL series...
Page 28: ...4 3 External Wiring Diagram www fastech co kr 28 4 3 2 Ezi SERVO Plus R 86mm...
Page 29: ...4 3 External Wiring Diagram 29 www fastech co kr 4 3 3 Ezi SERVO Plus R MINI...
Page 30: ...4 3 External Wiring Diagram www fastech co kr 30 4 3 4 Ezi SERVO ALL 28 series...
Page 31: ...4 3 External Wiring Diagram 31 www fastech co kr 4 3 5 Ezi SERVO ALL 42 56 series...
Page 32: ...4 3 External Wiring Diagram www fastech co kr 32 4 3 6 Ezi SERVO ALL 60 series...
Page 33: ...4 3 External Wiring Diagram 33 www fastech co kr 4 3 7 Ezi SERVO ALL 60 ABS...
Page 44: ...5 3 Ezi SERVO ALL 28 www fastech co kr 44 5 Network ID Setting 6 Connector Specifications...
Page 51: ...5 5 Ezi SERVO ALL 60 60 ABS series 51 www fastech co kr 8 Connector Specifications...