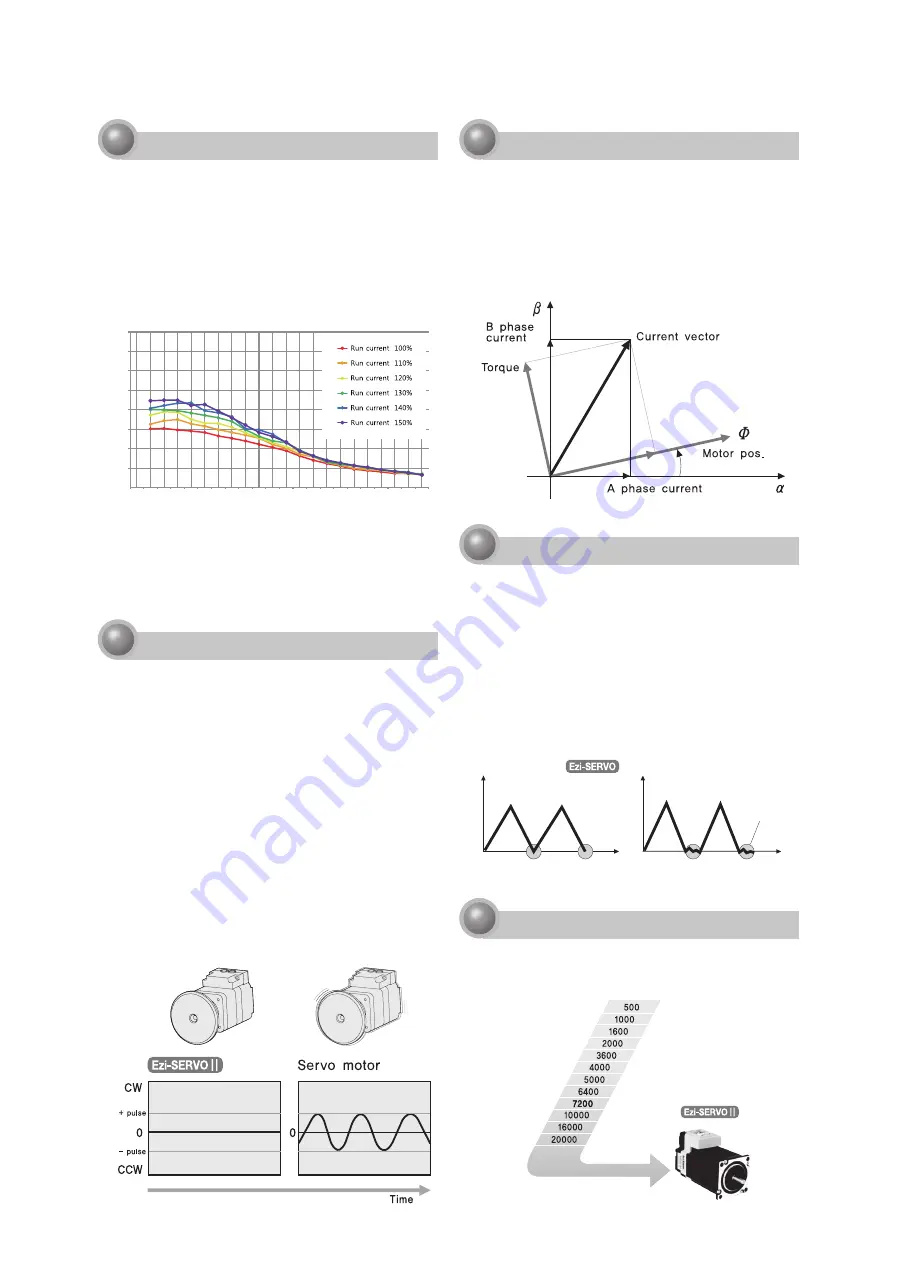
www.fastech-motions.com - 7
※ The torque at low speed is improved about 30%.
Measured Condition : Drive = Ezi-SERVOⅡ-BT-42L
Motor Voltage = 24VDC
Input Voltage = 24VDC
5
Torque Improvement
Ezi-SERVOⅡ can increase the motor current up to 150%
by setting the Run Current by parameter. Therefore
acceleration and deceleration characteristics and torque
characteristics at low speed can be increased.
Ezi-SERVOⅡ can improve the torque in the low speed
range by about 30%.
(Motor Current Setting)
Speed [rpm] × 100
Torque [mN
.
m]
800
700
600
500
400
300
200
100
0
0.1 1
2 3 4 5 6 7
8 9 10 12 14 16 18 20 22 24 26 28 30
6
No Hunting
Traditional servo motor drives overshoot their position
and try to correct by overshooting the opposite direction,
especially in high gain applications. This is called null
hunt and is especially prevalent in systems that the
break away or static friction is significantly higher than
the running friction. The cure is lowering the gain, which
affects accuracy or using Ezi-SERVOⅡ Motion Control
System. Ezi-SERVOⅡ utilizes the unique characteristics
of stepping motors and locks itself into the desired target
position, eliminating Null Hunt. This feature is especially
useful in applications such as nanotech manufacturing,
semiconductor fabrication, vision systems and ink jet
printing in which system oscillation and vibration could
be a problem.
7
Smooth and Accurate
Ezi-SERVOⅡ is a high-precision servo drive, using a
high-resolution encoder with 20,000 pulses/revolution.
Unlike a conventional Microstep drive, the on-board
high performance MCU (Micro Controller Unit) performs
vector control and filtering, producing a smooth rotational
control with minimum ripples.
8
Fast Response
Similar to conventional stepping motors, Ezi-SERVOⅡ
instantly synchronizes with command pulses providing
fast positional response. Ezi-SERVOⅡ is the optimum
choice when zero-speed stability and rapid motions
within a short distance are required. Traditional servo
motor systems have a natural delay called settling time
between the command input signals and the resultant
motion because of the constant monitoring of the current
position.
9
High Resolution
The unit of the position command can be divided
precisely. (Max. 20,000 pulses/revolution)