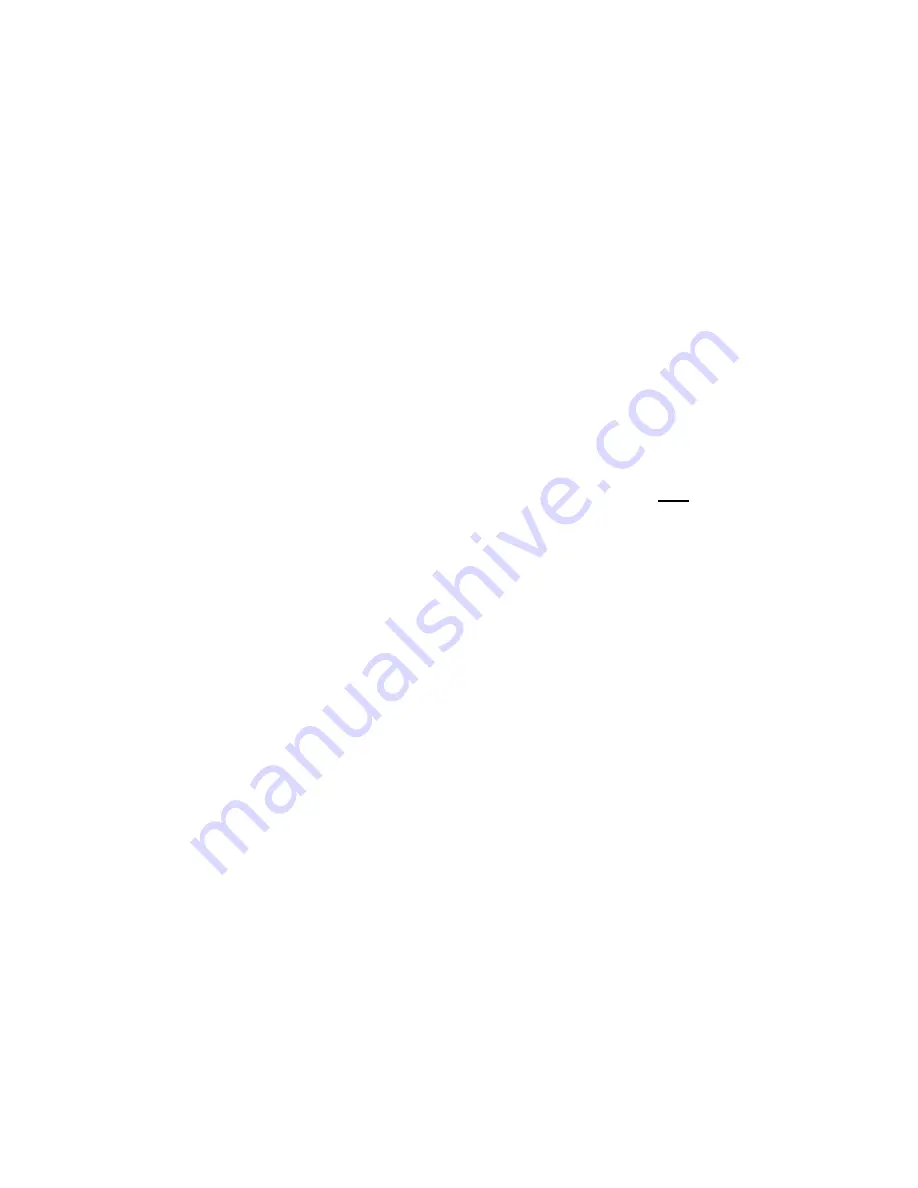
ANNUAL MAINTENANCE
1. DRAIN AND REPLACE OIL
at least once a year or 200 operating hours, whichever comes first.
Allow unit to run for five minutes before draining to warm up the oil. Remove six screws that hold
on the back panel. The drain plug is on the end of the oil tank. After draining and replacing plug,
fill through the breather cap hole on top of the unit to within 1” of the top. (approx. 1-1/2 gallons)
Use a quality hydraulic oil with an
ISO VG-46
weight rating for general year round use. Use a
heavier
ISO VG-68
weight rating for continuous hot weather operation.
2.
PRESSURE WASH MACHINE
inside and out. Remove the front and rear cover plates to access
the inside area of the machine. Using compressed air, blow dry the inside and outside
components after washing.
3.
INSPECT MACHINE FOR OIL LEAKS
by turning on and running machine for a minimum of 15
minutes. During this time, cycle the bender a minimum of 10 times. If your machine has a cutter,
cycle the cutter a minimum of 10 times as well. Turn off machine and with the front and rear cover
plates still removed, use a flash light to look for any signs of hydraulic fluid leaking. Check the
entire rotary actuator that moves the bender. Check the cutter hydraulic cylinder (if so equipped).
Inspect around the chrome piston rod, and the rear body seal. Check all hydraulic lines and
fittings. Oil can travel great distances so it is important to try to find the true source of the leak so
that it can be repaired.
4. LUBRICATE ALL THREADED FASTENERS
and inspect all wearable components. Remove the
bending post bolt, the bending support roller bolt, the cutter adjustable bar support bolt (if so
equipped) and lubricate them liberally with a good quality anti-seize. Use lithium grease and
lubricate the end bearings of the table rollers. Spray LPS rust inhibitor on all exposed metal parts
to protect them from corrosion.
5. REASSEMBLE MACHINE AND TEST
for proper operation and performance. To test the
hydraulic system set-up machine to bend a
1” bar around the 6” die. Set the bend adjuster to 180
degrees
. Time the machine to bend a 1” bar 180 degrees. It should take a maximum of 18 to 20
seconds to co
mplete this bend. Set up the cutter (if so equipped) to cut a 1” bar. Time the
machine to cut a 1” bar. It should take a maximum of 5 seconds to complete this cut. If after these
tests you find your machine taking longer than the times shown above, this is an indication that
your hydraulic pump is showing signs of wear and may need to be replaced.
****
The
FASCUT
factory has very knowledgeable people on staff answering your phone calls.
They are trained in all facets of our machines operation and are very good at helping you
determine exactly what is wrong with your machine. The factory stocks every component of all our
machines and can assist you and ship any part to you immediately with easy instructions for you
to repair your machine on-site.
MADE IN THE U.S.A
.
We are proud to be able to offer you outstanding customer service to go along with the quality
machines that
FASCUT
has produced for over 30 years.
Summary of Contents for 19547
Page 14: ...Page is blank ...
Page 16: ...Rotary Bending Components Breakdown A ...
Page 18: ...Rotary Hydraulic Actuator Breakdown AA ...
Page 20: ...Cutter Head and Hydraulic Cylinder Breakdown B ...
Page 22: ......
Page 24: ......
Page 26: ......
Page 28: ......
Page 30: ......
Page 32: ...Electrical Components Breakdown E ...