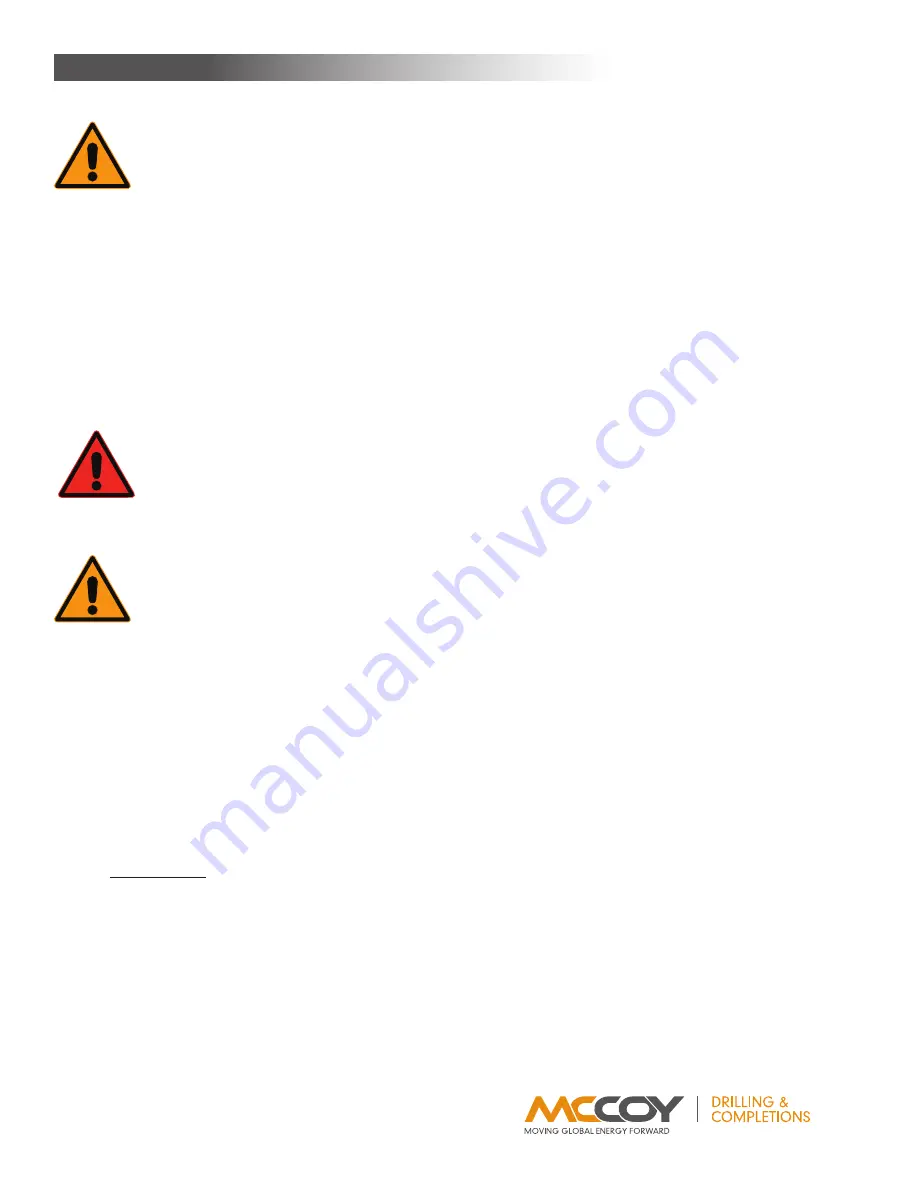
6.6
hD8625 8-
5
/
8
” 35K T
ong
T
echnical
M
anual
T
orque
M
easureMenT
C.
PERIODIC INSPECTION AND MAINTENANCE
MAINTAIN GREATER-THAN HALF FULL FLUID LEVEL IN THE HAND PUMP BOWL TO AVOID PUMPING
AIR INTO THE SYSTEM. DO NOT ALLOW THE LEVEL TO FALL BELOW ONE-HALF FULL
UN-CONTAINED SPILLAGE OF THE HYDRAULIC FLUID IN THIS SYSTEM MAY CONTRAVENE GOV-
ERNMENTAL ENVIRONMENTAL REGULATIONS, OR THE ENVIRONMENTAL REGULATIONS AND
POLICIES OF YOUR COMPANY. FARR CANADA CORP. HIGHLY RECOMMENDS PLACING YOUR
LOAD CELL IN A CONTAINMENT BASIN BEFORE PROCEEDING WITH THE BLEEDING & REFILLING
PROCESS.
d. Fill hand pump bowl with W15/16 hydraulic fluid.
e. Remove the vent plug screw and Stat-O-Seal (Items C and D on Illustration 6.A.4, or item H on Illustration 6.A.5) to allow
trapped air to escape.
f. Pump fluid into the system until no more air is seen escaping from the vent port.
g. Replace the vent plug screw and Stat-O-Seal and tighten securely.
h. Remove load cell from containment vessel and wipe clean. Reclaim the hydraulic fluid (if it is clean) or dispose of all waste
materials according to governmental or your company’s proscribed environmental protection regulations.
i.
Disconnect the hand pump from the torque gauge.
j.
Replace the brass cap on the torque gauge check valve fitting.
3.
Reference Checking Your Torque Measurement System
The following steps define a process for determining if your torque measurement system is correctly measuring and indicating within
an expected range. This procedure is best suited for performing in a shop or location removed from the drill floor, within range of a
crane. This is a reference check and not a calibration. Calibrations must be performed at an authorized calibration facility.
Tension Load Cell
a. Locate a known weight in the range of approximately 500 to 1000 lbs (227 to 455 kg), and move the weight next to the tong
and backup assembly.
b. Remove the tension load cell from the tong, but do not disconnect from the torque gauge.
c. Suspend the load cell, piston side up, from a crane capable of supporting the known weight in Step 3a.
d. Connect the rod side of the load cell to the known weight, and use the crane to hoist the weight from the surface to be sus-
pended freely.
Continued on next page...
1. Inspection
The torque measurement system supplied with your equipment is designed and built to provide years of trouble-free service with
minimum maintenance. Periodic inspections of the load cell, hydraulic lines and fittings are recommended in order to keep the system
in top operating condition. A thorough inspection should be made at each rig-up.
2.
Fluid Recharge
Recharge hydraulic system with W15/16 fluid through the check valve on the torque indicating gauge. Recharging must only be
performed when there is no load on the load cell. Refer to the illustrations on pages 6.3 & 6.4 for guidance if required.
a. Place the torque indicating gauge higher than the load cell. Remove the brass 1/4” cap from the fitting on the check valve on
the top of the gauge.
b. Connect the hand pump to the check valve fitting.
c. Elevate the load cell so it is higher than the torque gauge and hand pump.
ONLY QUALIFIED, DESIGNATED PERSONNEL ARE PERMITTED TO PERFORM MAINTENANCE ON THE
TORQUE MEASUREMENT SYSTEM.
Summary of Contents for HD8625
Page 2: ......
Page 4: ...This page intentionally left blank ...
Page 6: ...This page intentionally left blank ...
Page 12: ...This page intentionally left blank ...
Page 42: ...This page intentionally left blank ...
Page 83: ...Technical Manual HD8625 8 5 8 35K Tong 5 1 Parts and Assemblies HD8625 8 5 8 35K Tong ...
Page 84: ...5 2 HD8625 8 5 8 35K Tong Technical Manual Gear Train Layout H B C D H J A K E F G ...
Page 86: ...5 4 HD8625 8 5 8 35K Tong Technical Manual Support Roller A B D J C E H D E F G ...
Page 88: ...5 6 HD8625 8 5 8 35K Tong Technical Manual Door Pivot Roller A B D J C E H D E F G ...
Page 90: ...5 8 HD8625 8 5 8 35K Tong Technical Manual Rotary Idler Assembly A B C E B D F C D G G H J F ...
Page 92: ...5 10 HD8625 8 5 8 35K Tong Technical Manual Pinion Idler Assembly A B C E L D F K G J G H ...
Page 94: ...5 12 HD8625 8 5 8 35K Tong Technical Manual Pinion Assembly A B C E A D F B D G H E C ...
Page 102: ...5 20 HD8625 8 5 8 35K Tong Technical Manual Tong Leg Weldments A C D E F H G J B ...
Page 106: ...5 24 HD8625 8 5 8 35K Tong Technical Manual Motor Motor Mount A B C D E J F G H Q K P L M N ...
Page 108: ...5 26 HD8625 8 5 8 35K Tong Technical Manual Brake Bands A B C D E F G H J ...
Page 116: ...This page intentionally left blank ...
Page 124: ...This page intentionally left blank ...
Page 133: ...Technical Manual HD8625 8 5 8 35K Tong 7 9 Hydraulic Components ...
Page 140: ...7 16 HD8625 8 5 8 35K Tong Technical Manual Hydraulic Components ...
Page 141: ...Technical Manual HD8625 8 5 8 35K Tong 7 17 Hydraulic Components ...
Page 142: ...7 18 HD8625 8 5 8 35K Tong Technical Manual Hydraulic Components ...
Page 143: ...Technical Manual HD8625 8 5 8 35K Tong 7 19 Hydraulic Components ...
Page 144: ...7 20 HD8625 8 5 8 35K Tong Technical Manual ...
Page 145: ...Technical Manual HD8625 8 5 8 35K Tong 7 21 ...
Page 146: ...7 22 HD8625 8 5 8 35K Tong Technical Manual Hydraulic Components ...
Page 147: ...Technical Manual HD8625 8 5 8 35K Tong 7 23 Hydraulic Components ...
Page 148: ...7 24 HD8625 8 5 8 35K Tong Technical Manual Hydraulic Components ...
Page 149: ...Technical Manual HD8625 8 5 8 35K Tong 7 25 Hydraulic Components ...
Page 150: ...7 26 HD8625 8 5 8 35K Tong Technical Manual Hydraulic Components ...
Page 151: ...Technical Manual HD8625 8 5 8 35K Tong 7 27 Hydraulic Components ...
Page 152: ...7 28 HD8625 8 5 8 35K Tong Technical Manual Hydraulic Components ...
Page 153: ...Technical Manual HD8625 8 5 8 35K Tong 7 29 Hydraulic Components ...
Page 154: ...7 30 HD8625 8 5 8 35K Tong Technical Manual Hydraulic Components ...