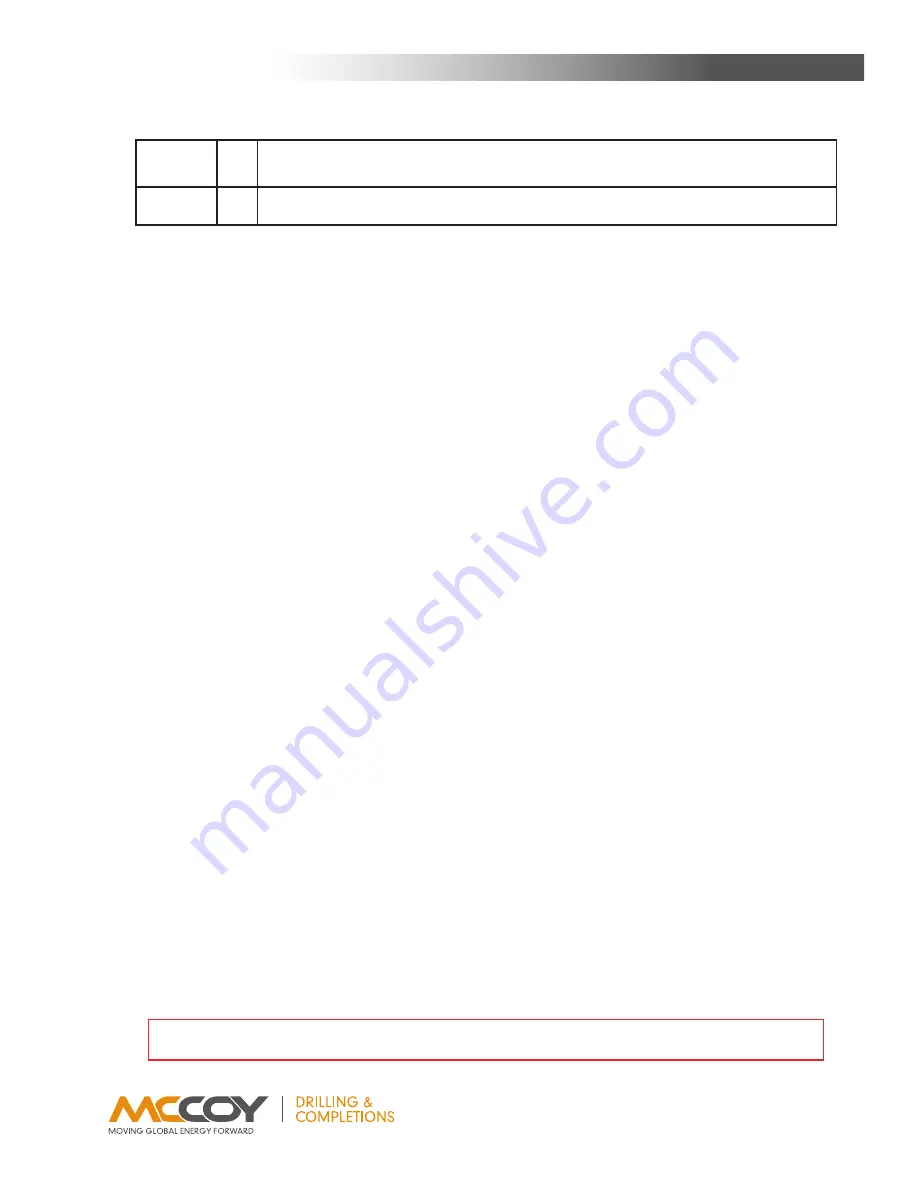
T
echnical
M
anual
hD8625 8-
5
/
8
” 35K T
ong
iii
This manual covers the following models:
NOTE:
Some illustrations used in this manual may not exactly match
your model of tong.
PATENTED & PATENTS PENDING
TONG
MODEL
REV
DESCRIPTION
80-0605-6
1
Tong is equipped with a two-speed hydraulic motor, motor valve, lift cylinder valve, rigid sling,
and safety door.
Summary of Contents for HD8625
Page 2: ......
Page 4: ...This page intentionally left blank ...
Page 6: ...This page intentionally left blank ...
Page 12: ...This page intentionally left blank ...
Page 42: ...This page intentionally left blank ...
Page 83: ...Technical Manual HD8625 8 5 8 35K Tong 5 1 Parts and Assemblies HD8625 8 5 8 35K Tong ...
Page 84: ...5 2 HD8625 8 5 8 35K Tong Technical Manual Gear Train Layout H B C D H J A K E F G ...
Page 86: ...5 4 HD8625 8 5 8 35K Tong Technical Manual Support Roller A B D J C E H D E F G ...
Page 88: ...5 6 HD8625 8 5 8 35K Tong Technical Manual Door Pivot Roller A B D J C E H D E F G ...
Page 90: ...5 8 HD8625 8 5 8 35K Tong Technical Manual Rotary Idler Assembly A B C E B D F C D G G H J F ...
Page 92: ...5 10 HD8625 8 5 8 35K Tong Technical Manual Pinion Idler Assembly A B C E L D F K G J G H ...
Page 94: ...5 12 HD8625 8 5 8 35K Tong Technical Manual Pinion Assembly A B C E A D F B D G H E C ...
Page 102: ...5 20 HD8625 8 5 8 35K Tong Technical Manual Tong Leg Weldments A C D E F H G J B ...
Page 106: ...5 24 HD8625 8 5 8 35K Tong Technical Manual Motor Motor Mount A B C D E J F G H Q K P L M N ...
Page 108: ...5 26 HD8625 8 5 8 35K Tong Technical Manual Brake Bands A B C D E F G H J ...
Page 116: ...This page intentionally left blank ...
Page 124: ...This page intentionally left blank ...
Page 133: ...Technical Manual HD8625 8 5 8 35K Tong 7 9 Hydraulic Components ...
Page 140: ...7 16 HD8625 8 5 8 35K Tong Technical Manual Hydraulic Components ...
Page 141: ...Technical Manual HD8625 8 5 8 35K Tong 7 17 Hydraulic Components ...
Page 142: ...7 18 HD8625 8 5 8 35K Tong Technical Manual Hydraulic Components ...
Page 143: ...Technical Manual HD8625 8 5 8 35K Tong 7 19 Hydraulic Components ...
Page 144: ...7 20 HD8625 8 5 8 35K Tong Technical Manual ...
Page 145: ...Technical Manual HD8625 8 5 8 35K Tong 7 21 ...
Page 146: ...7 22 HD8625 8 5 8 35K Tong Technical Manual Hydraulic Components ...
Page 147: ...Technical Manual HD8625 8 5 8 35K Tong 7 23 Hydraulic Components ...
Page 148: ...7 24 HD8625 8 5 8 35K Tong Technical Manual Hydraulic Components ...
Page 149: ...Technical Manual HD8625 8 5 8 35K Tong 7 25 Hydraulic Components ...
Page 150: ...7 26 HD8625 8 5 8 35K Tong Technical Manual Hydraulic Components ...
Page 151: ...Technical Manual HD8625 8 5 8 35K Tong 7 27 Hydraulic Components ...
Page 152: ...7 28 HD8625 8 5 8 35K Tong Technical Manual Hydraulic Components ...
Page 153: ...Technical Manual HD8625 8 5 8 35K Tong 7 29 Hydraulic Components ...
Page 154: ...7 30 HD8625 8 5 8 35K Tong Technical Manual Hydraulic Components ...