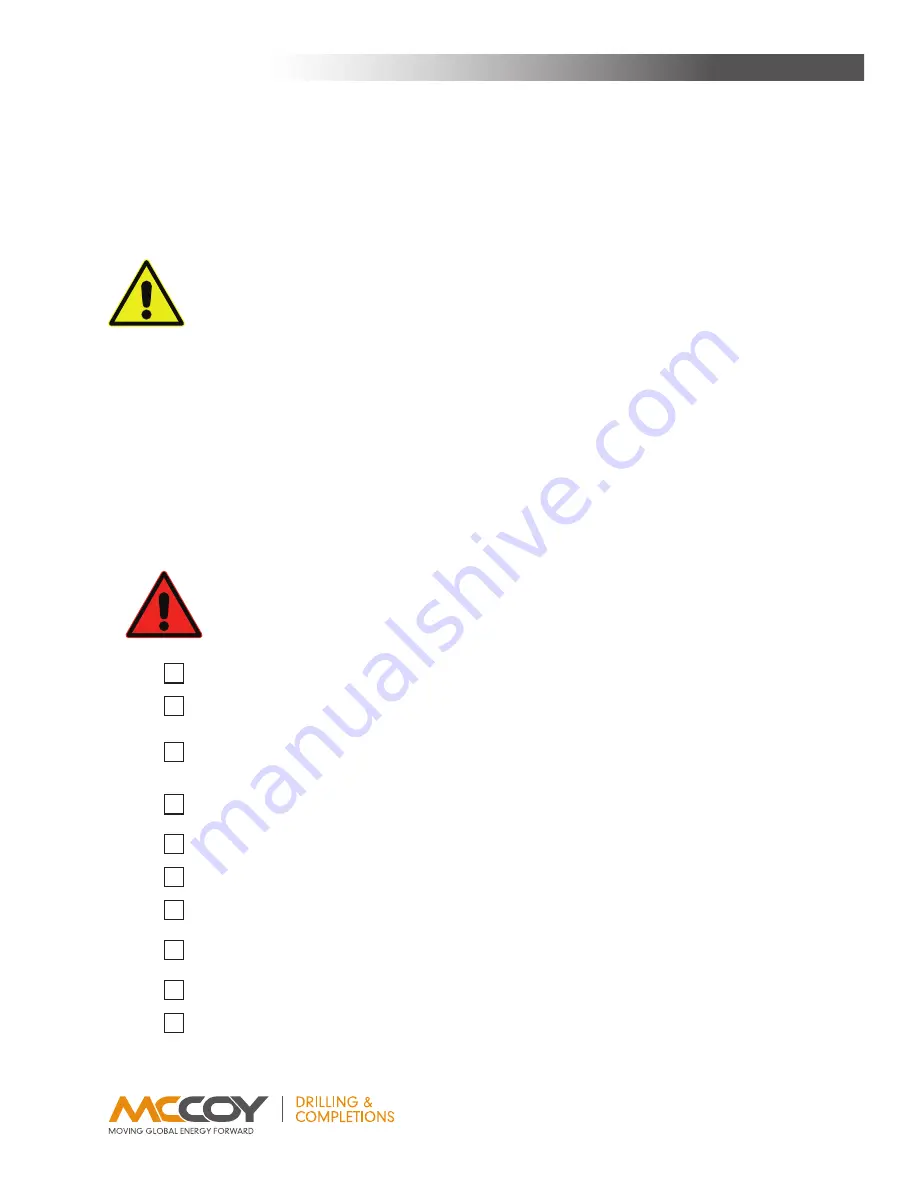
T
echnical
M
anual
hD8625 8-
5
/
8
” 35K T
ong
3.27
M
ainTenance
K.
TUBULAR CONNECTION EQUIPMENT DE-COMMISSIONING & SHIPPING PROCEDURE
Perform the following decommissioning procedures when removing tubular connection equipment from service, with the intent of short to
long-term storage. These procedures are essential for ensuring proper protection of the equipment from environmental attack, and to aid
in the quick turnaround when returning the equipment to service.
Store all o-rings, seals, packings, gaskets, etc. in strong moisture proof, airtight containers. Ensure that these items are not crushed,
nicked, or otherwise damaged.
Do not perform any further actions or maintenance while the tong is connected to any hydraulic power supply. Farr recommends that all
hydraulic lines are fully disconnected, and residual hydraulic pressure is bled off. Ensure adequate containment is in place to prevent
environmental contamination from residual hydraulic fluid.
1.
Perform an initial wash of the tool in order to remove the majority of dirt and grease build-up. Ensure adequate containment is
in place to prevent environmental contamination from residual hydraulic fluid and dirty grease.
2.
Remove the access panel on the side of the tong directly adjacent to the shifter mechanism.
3.
Clean the interior of the tong thoroughly, using either water (do not use a pressure washer), or an appropriate solvent-based
grease-cutting cleaner such as Varsol. Ensure adequate containment is in place to prevent environmental contamination from
residual hydraulic fluid, dirty grease, and cleaning agents. Make a note if any metal shavings or metal pieces are flushed out of
the gear train cavity - if shavings or metal pieces are seen the tong must be overhauled before it is returned to service.
4.
Clean the exterior of the tool thoroughly, using either water (do not use a pressure washer), or an appropriate solvent-based
grease-cutting cleaner such as Varsol. Ensure adequate containment is in place to prevent environmental contamination from
residual hydraulic fluid, dirty grease, and cleaning agents.
5.
Inspect all fasteners and fastener safety wires. Replace any missing fasteners - use Grade 8 bolts only. Re-torque all external
fasteners to SAE specifications.
6.
Inspect backing pin(s). If cracked, broken, or bent it (they) must be replaced.
7.
Repair or replace any damaged or missing external body parts, such as torque gauge mounts, hydraulic supports, safety door
protectors, etc.
8.
Inspect all paint - locations in which the paint has been damaged must be repaired prior to storage. Prepare areas to be painted
to ensure they are free of grease, dirt, or solvent. Touch up using a solvent-based acrylic paint - “McCoy Grey” is paint number
RAL7015. Allow sufficient time for paint to dry before proceeding.
9.
Perform a liberal lubrication of the equipment - refer to Maintenance section of manual to determine lubrication points. Gener-
ously fill the gear train housing with grease through the access panel, and also through the opening in the rotary gear.
10.
Connect the equipment to a hydraulic power unit. Ensure all lines are fully made up to prevent equipment damage from exces-
sive back pressure. Do not neglect to connect the motor drain.
HYDRAULIC PRESSURES AS HIGH AS OPERATING PRESSURE MAY REMAIN TRAPPED IN SMALL
AREAS OF THE EQUIPMENT. ENSURE ALL MAINTENANCE IS CARRIED OUT BY A QUALIFIED
SERVICE TECHNICIAN, AND THAT ADEQUATE PERSONAL PROTECTIVE EQUIPMENT IS USED TO
GUARD AGAINST PRESSURE-INDUCED INJURIES
D
ePressurIzatIon
P
roCeDure
I
n
P
reParatIon
f
or
s
torage
:
1) Rotate the tong so that the opening in the rotary gear faces the gear train (towards the rear of the tong). Ensure tong and backup
doors (if equipped) are closed. Fully extend the lift cylinder (if equipped). If mounted in a frame, retract the float cylinders (if equipped).
2) De-energize the power unit.
3) Repeatedly actuate the tong motor control valve lever IN BOTH DIRECTIONS to dissipate any residual pressure in the valve and
motor.
4) Remove the hydraulic SUPPLY line from the equipment.
5) Repeatedly actuate the remaining control valve levers IN BOTH DIRECTIONS to dissipate any residual pressure in the remainder of
the hydraulic control system.
7) Disconnect the hydraulic RETURN line from the equipment.
8) Disconnect remaining hoses such as case drains, or lines connected to the turns counter.
IN ORDER TO MAINTAIN THE INTEGRITY OF INSTALLED SEALS, MCCOY RECOMMENDS THAT THE
MAXIMUM STORAGE INTERVAL NOT EXCEED ONE YEAR. AT LEAST ONCE PER YEAR ALL TUBULAR
CONNECTION IN LONG-TERM STORAGE SHOULD BE RECOMMISSIONED AS PER SECTION 3.M. IF
FURTHER STORAGE IS REQUIRED, THE EQUIPMENT SHOULD THEN BE PUT THROUGH ANOTHER
DE-COMMISSIONING PROCEDURE.
Summary of Contents for HD8625
Page 2: ......
Page 4: ...This page intentionally left blank ...
Page 6: ...This page intentionally left blank ...
Page 12: ...This page intentionally left blank ...
Page 42: ...This page intentionally left blank ...
Page 83: ...Technical Manual HD8625 8 5 8 35K Tong 5 1 Parts and Assemblies HD8625 8 5 8 35K Tong ...
Page 84: ...5 2 HD8625 8 5 8 35K Tong Technical Manual Gear Train Layout H B C D H J A K E F G ...
Page 86: ...5 4 HD8625 8 5 8 35K Tong Technical Manual Support Roller A B D J C E H D E F G ...
Page 88: ...5 6 HD8625 8 5 8 35K Tong Technical Manual Door Pivot Roller A B D J C E H D E F G ...
Page 90: ...5 8 HD8625 8 5 8 35K Tong Technical Manual Rotary Idler Assembly A B C E B D F C D G G H J F ...
Page 92: ...5 10 HD8625 8 5 8 35K Tong Technical Manual Pinion Idler Assembly A B C E L D F K G J G H ...
Page 94: ...5 12 HD8625 8 5 8 35K Tong Technical Manual Pinion Assembly A B C E A D F B D G H E C ...
Page 102: ...5 20 HD8625 8 5 8 35K Tong Technical Manual Tong Leg Weldments A C D E F H G J B ...
Page 106: ...5 24 HD8625 8 5 8 35K Tong Technical Manual Motor Motor Mount A B C D E J F G H Q K P L M N ...
Page 108: ...5 26 HD8625 8 5 8 35K Tong Technical Manual Brake Bands A B C D E F G H J ...
Page 116: ...This page intentionally left blank ...
Page 124: ...This page intentionally left blank ...
Page 133: ...Technical Manual HD8625 8 5 8 35K Tong 7 9 Hydraulic Components ...
Page 140: ...7 16 HD8625 8 5 8 35K Tong Technical Manual Hydraulic Components ...
Page 141: ...Technical Manual HD8625 8 5 8 35K Tong 7 17 Hydraulic Components ...
Page 142: ...7 18 HD8625 8 5 8 35K Tong Technical Manual Hydraulic Components ...
Page 143: ...Technical Manual HD8625 8 5 8 35K Tong 7 19 Hydraulic Components ...
Page 144: ...7 20 HD8625 8 5 8 35K Tong Technical Manual ...
Page 145: ...Technical Manual HD8625 8 5 8 35K Tong 7 21 ...
Page 146: ...7 22 HD8625 8 5 8 35K Tong Technical Manual Hydraulic Components ...
Page 147: ...Technical Manual HD8625 8 5 8 35K Tong 7 23 Hydraulic Components ...
Page 148: ...7 24 HD8625 8 5 8 35K Tong Technical Manual Hydraulic Components ...
Page 149: ...Technical Manual HD8625 8 5 8 35K Tong 7 25 Hydraulic Components ...
Page 150: ...7 26 HD8625 8 5 8 35K Tong Technical Manual Hydraulic Components ...
Page 151: ...Technical Manual HD8625 8 5 8 35K Tong 7 27 Hydraulic Components ...
Page 152: ...7 28 HD8625 8 5 8 35K Tong Technical Manual Hydraulic Components ...
Page 153: ...Technical Manual HD8625 8 5 8 35K Tong 7 29 Hydraulic Components ...
Page 154: ...7 30 HD8625 8 5 8 35K Tong Technical Manual Hydraulic Components ...