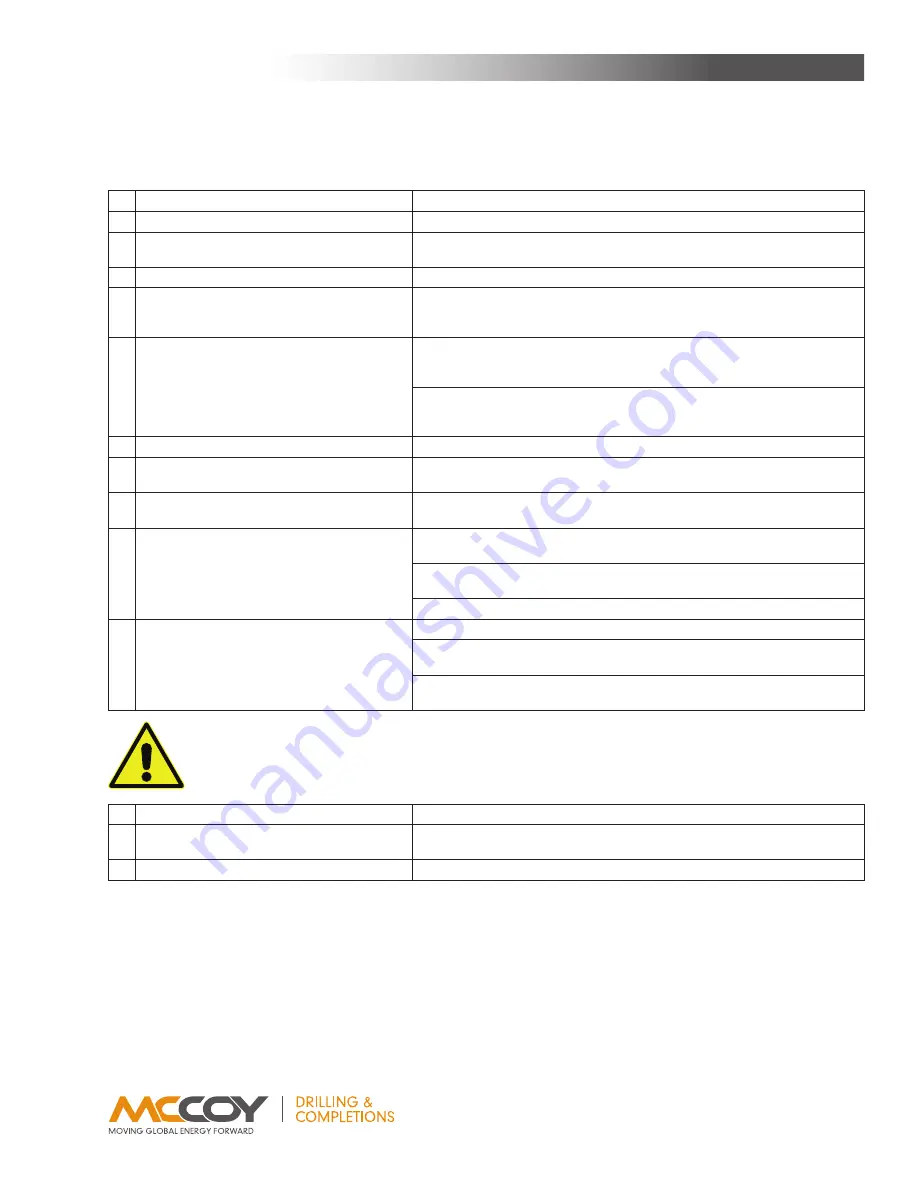
T
echnical
M
anual
hD8625 8-
5
/
8
” 35K T
ong
4.1
T
roubleshooTing
Adequate maintenance and proper fluid selection is essential for minimizing hydraulic-related failures. All troubleshooting must be performed
by a technician trained in hydraulic systems, and familiar with the equipment design, assembly and operation.
The following troubleshooting instructions are intended to be guidelines only. Any faults not solved through the use of this guide should be
referred to our engineering department for their evaluation and recommendations.
A.
TONG WILL NOT DEVELOP SUFFICIENT TORQUE
MCCOY DRILLING & COMPLETIONS GUARANTEES CALIBRATION OF A LOAD CELL/TORQUE GAUGE
ASSEMBLY FOR A PERIOD OF ONE YEAR. MCCOY SUGGESTS THAT THE LOAD CELL/TORQUE
GAUGE ASSEMBLY BE RETURNED TO THE FACTORY FOR RE-CALIBRATION ON A YEARLY BASIS.
POSSIBLE PROBLEM
SOLUTION(S)
1
Malfunctioning relief valve on tong hydraulic circuit See Section 4.B, Relief Valve Troubleshooting
2
Directional valve is leaking
Check directional valve. Neutral position should return fluid directly to the reservoir.
Replace or repair valve to ensure correct operation
3
Power unit is not producing adequate pressure
Troubleshoot power unit (see user’s manual for your particular unit)
4
Poor hydraulic pressure at the tong despite ade-
quate pressure at the power unit, or excessive
back pressure in the return line.
Restrictions exist in line between power unit and tong. Inspect integrity of self-seal-
ing couplings to ensure they are allowing full fluid flow. Check to ensure no other
restrictions exist (contaminated catch screens or filters, for example)
5
Fluid viscosity is not appropriate (too high or too
low)
Ensure hydraulic fluid being used is the viscosity recommended by McCoy Drilling &
Completions. Power unit pump may not prime if fluid is too heavy, and the hydraulic
system will overheat if fluid is too light. Replace with proper viscosity fluid
Hydraulic fluid viscosity is affected by environmental conditions. Ensure the fluid
being used is suitable for high or low temperatures. Replace with proper viscosity
fluid for the operating conditions if necessary
6
Worn or damaged tong motor causing slippage
Replace or repair worn or damaged motor
7
Damaged bearings or gears causing excessive
drag
Replace or repair worn or damaged gears or bearings
8
Jaws slipping on pipe
Ensure jaw dies are not worn to the point that they cannot grip. Ensure the correct
sized jaws are in use
9
Torque gauge is indicating incorrectly
Incorrect gauge is being used. Ensure gauge is the proper range, and has been
properly calibrated for the arm length of the equipment in use
Gauge has been damaged. Check gauge operation and calibration on independent
system
Gauge has mistakenly been married to an incorrect load cell
10
Load cell is measuring incorrectly
Incorrect load cell is being used
Air is trapped in torque measuring circuit (load cell, hydraulic line, or gauge. Refer
to torque measurement troubleshooting in Section 6 of this manual
Load cell has been damaged. Replace load cell, or return to McCoy for repair and
re-calibration
POSSIBLE PROBLEM
SOLUTION(S)
11
Incorrect motor speed selected (applies to 2-speed
motors only)
Maximum torque can only be developed when LOW motor speed (maximum hy-
draulic displacement) is selected.
12
Incorrect tong gear selected
Maximum torque can only be developed when LOW motor gear is selected
Summary of Contents for HD8625
Page 2: ......
Page 4: ...This page intentionally left blank ...
Page 6: ...This page intentionally left blank ...
Page 12: ...This page intentionally left blank ...
Page 42: ...This page intentionally left blank ...
Page 83: ...Technical Manual HD8625 8 5 8 35K Tong 5 1 Parts and Assemblies HD8625 8 5 8 35K Tong ...
Page 84: ...5 2 HD8625 8 5 8 35K Tong Technical Manual Gear Train Layout H B C D H J A K E F G ...
Page 86: ...5 4 HD8625 8 5 8 35K Tong Technical Manual Support Roller A B D J C E H D E F G ...
Page 88: ...5 6 HD8625 8 5 8 35K Tong Technical Manual Door Pivot Roller A B D J C E H D E F G ...
Page 90: ...5 8 HD8625 8 5 8 35K Tong Technical Manual Rotary Idler Assembly A B C E B D F C D G G H J F ...
Page 92: ...5 10 HD8625 8 5 8 35K Tong Technical Manual Pinion Idler Assembly A B C E L D F K G J G H ...
Page 94: ...5 12 HD8625 8 5 8 35K Tong Technical Manual Pinion Assembly A B C E A D F B D G H E C ...
Page 102: ...5 20 HD8625 8 5 8 35K Tong Technical Manual Tong Leg Weldments A C D E F H G J B ...
Page 106: ...5 24 HD8625 8 5 8 35K Tong Technical Manual Motor Motor Mount A B C D E J F G H Q K P L M N ...
Page 108: ...5 26 HD8625 8 5 8 35K Tong Technical Manual Brake Bands A B C D E F G H J ...
Page 116: ...This page intentionally left blank ...
Page 124: ...This page intentionally left blank ...
Page 133: ...Technical Manual HD8625 8 5 8 35K Tong 7 9 Hydraulic Components ...
Page 140: ...7 16 HD8625 8 5 8 35K Tong Technical Manual Hydraulic Components ...
Page 141: ...Technical Manual HD8625 8 5 8 35K Tong 7 17 Hydraulic Components ...
Page 142: ...7 18 HD8625 8 5 8 35K Tong Technical Manual Hydraulic Components ...
Page 143: ...Technical Manual HD8625 8 5 8 35K Tong 7 19 Hydraulic Components ...
Page 144: ...7 20 HD8625 8 5 8 35K Tong Technical Manual ...
Page 145: ...Technical Manual HD8625 8 5 8 35K Tong 7 21 ...
Page 146: ...7 22 HD8625 8 5 8 35K Tong Technical Manual Hydraulic Components ...
Page 147: ...Technical Manual HD8625 8 5 8 35K Tong 7 23 Hydraulic Components ...
Page 148: ...7 24 HD8625 8 5 8 35K Tong Technical Manual Hydraulic Components ...
Page 149: ...Technical Manual HD8625 8 5 8 35K Tong 7 25 Hydraulic Components ...
Page 150: ...7 26 HD8625 8 5 8 35K Tong Technical Manual Hydraulic Components ...
Page 151: ...Technical Manual HD8625 8 5 8 35K Tong 7 27 Hydraulic Components ...
Page 152: ...7 28 HD8625 8 5 8 35K Tong Technical Manual Hydraulic Components ...
Page 153: ...Technical Manual HD8625 8 5 8 35K Tong 7 29 Hydraulic Components ...
Page 154: ...7 30 HD8625 8 5 8 35K Tong Technical Manual Hydraulic Components ...