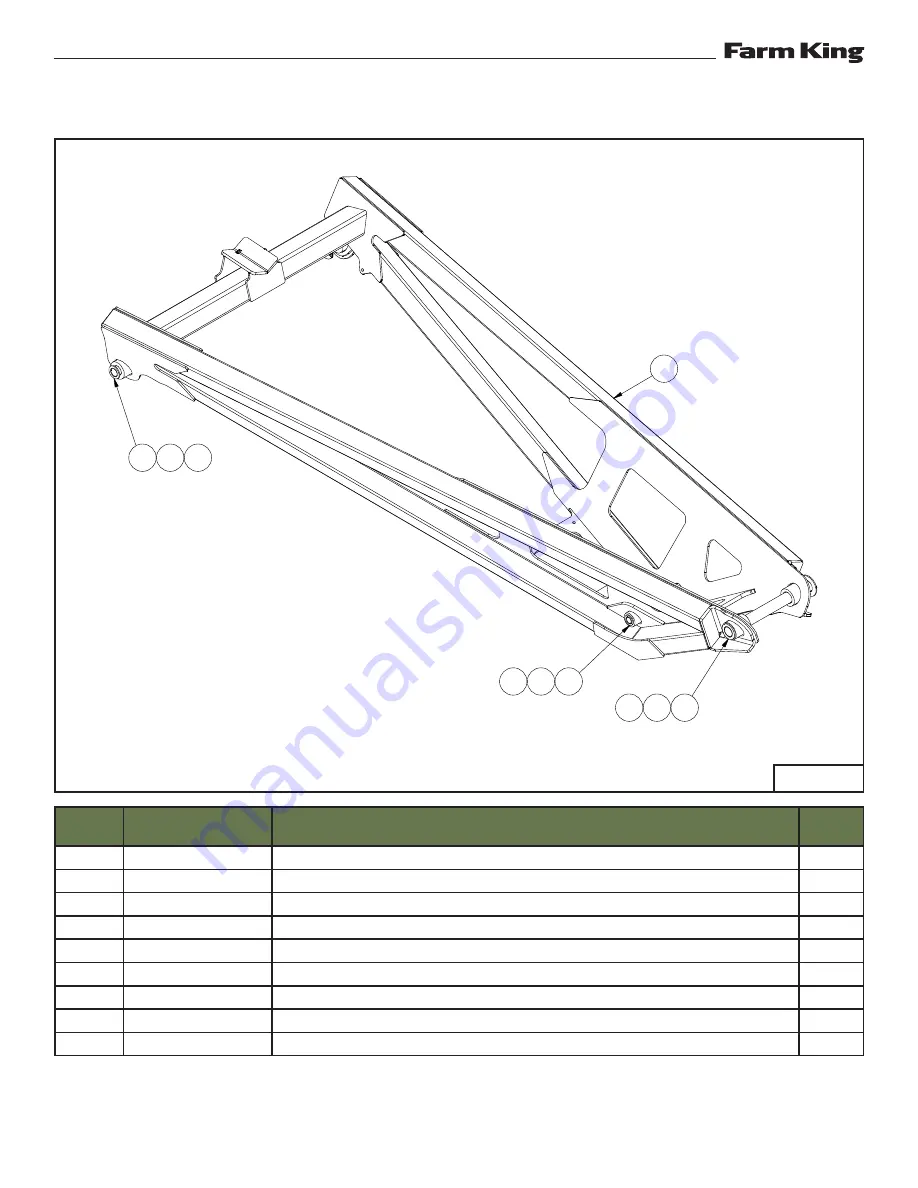
Parts Identification - 13” Conventional Auger
112
UPPER LIFT ARM - C1342, C1352
ITEM
PART NUMBER
DESCRIPTION
QTY.
1
81210
1/4" X 2" COTTER PIN (PL)
3
2
84522
1" ID SAE FLAT WASHER (PL)
1
3
960105
LIFT ARM PIVOT PIN WELDT 1.000" DIA
1
4
960110
SWIVEL PIN 1.250" DIA
2
5
960632
LIFT ARM PIVOT PIN WELDT 1.500" DIA
1
6
967135
1 1/2" RIM WASHER (10GA) (PL)
1
7
9812433
3/16" X 1 1/2" COTTER PIN
1
8
9812487
1 1/4" X 10GA NARROW RIM WASHER (PL)
2
9
F2592
WELDT-C1342/52 UPPER LIFT ARM
1
9
5
6
1
3
7
2
4
8
1
935885
Summary of Contents for 1342
Page 1: ...082020 FK422 OPERATOR AND PARTS MANUAL 13 CONVENTIONAL AUGER Models 1342 1352 1362 ...
Page 2: ......
Page 4: ... 13 Conventional Auger ii ...
Page 6: ... 13 Conventional Auger 2 ...
Page 8: ...Warranty Registration Form 13 Conventional Auger 4 ...
Page 10: ...Introduction 13 Conventional Auger 6 ...
Page 13: ...Introduction 13 Conventional Auger 9 BRIDGING TRUSS CABLE 52 FT MODEL 62 FT MODEL ...
Page 14: ...Introduction 13 Conventional Auger 10 ...
Page 16: ...Safety 13 Conventional Auger 12 ...
Page 23: ...Safety 13 Conventional Auger 19 ...
Page 84: ...Operation 13 Conventional Auger 80 ...
Page 98: ...Maintenance 13 Conventional Auger 94 ...
Page 108: ...Maintenance 13 Conventional Auger 104 ...
Page 110: ...Parts Identification 13 Conventional Auger 106 AXLE STUB W HUB 175 HUB 176 WHEEL ANDTIRE 177 ...
Page 111: ...Parts Identification 13 Conventional Auger 107 ...
Page 182: ...Parts Identification 13 Conventional Auger 178 ...
Page 184: ...Specifications 13 Conventional Auger 180 ...
Page 186: ...Specifications 13 Conventional Auger 182 HARDWARETORQUE VALUES Metric Chart ...
Page 187: ...Specifications 13 Conventional Auger 183 Imperial Chart ...
Page 190: ...Warranty 13 Conventional Auger 186 ...
Page 193: ......