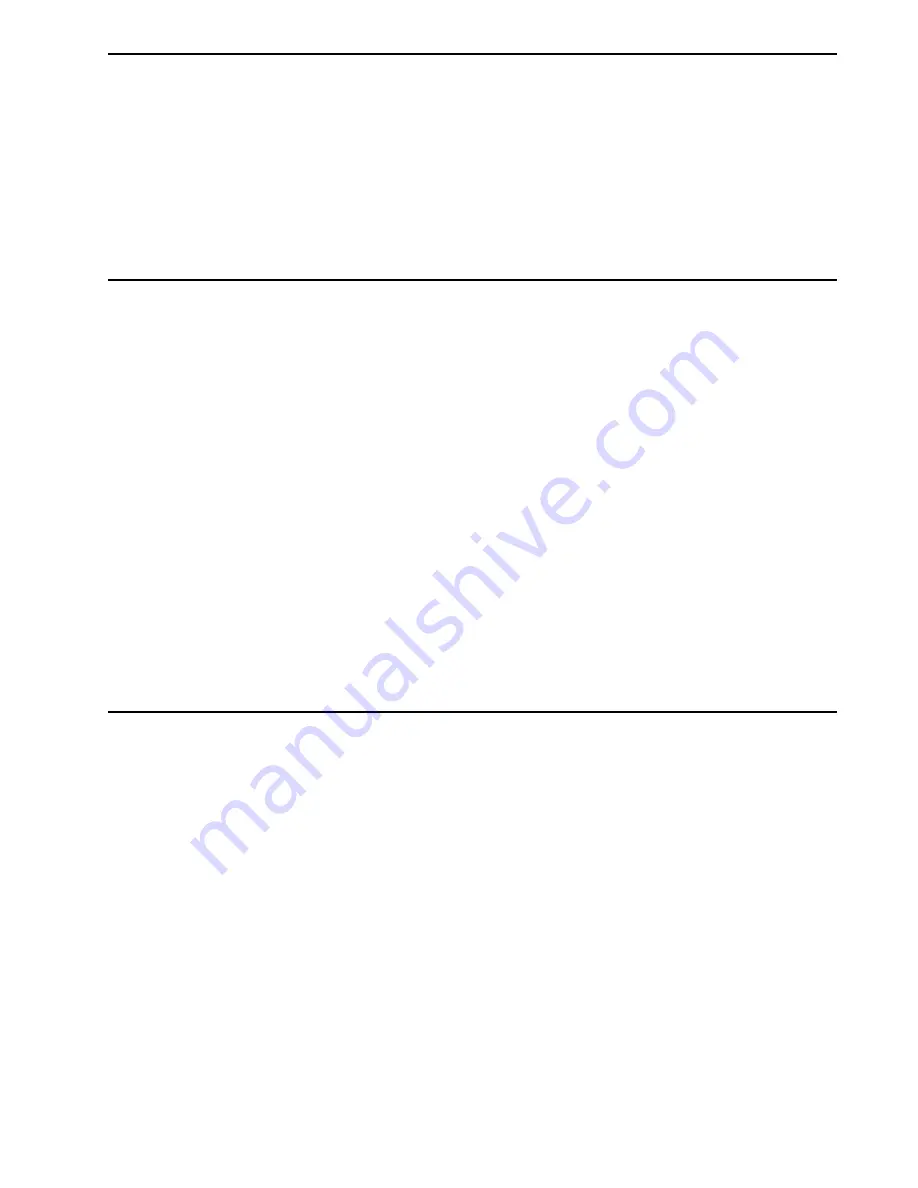
61
1. Grain moisture discharged too wet:
Reduce % Unload Rate setting
2. Grain moisture discharged too dry:
Increase % Unload Rate setting
3. Grain moisture discharged inconsistent:
Check that plenum temperatures are being held consistent
Check for changes in incoming grain moisture. If changes are occurring, manual % Unload
Rate setting must be adjusted accordingly. You may wish to change to Auto Moisture control mode.
Check for intermittently plugged grain columns.
Check fill auger for proper operation and that an adequate grain supply is available to main-
tain grain seal.
1. Grain moisture discharged too wet:
Increase moisture control temperature set point.
2. Grain moisture discharged too dry:
Decrease moisture control temperature set point.
If discharge rate is running at or near 100%, it may be necessary to reduce plenum tem-
peratures to allow moisture control more freedom to work.
3. Grain moisture discharged inconsistent:
Check that plenum temperatures are being held consistent.
Check for plugged grain columns (empty column to correct).
If large variations in incoming moisture are occurring, the control can only minimize
changes in discharge moisture. Some variation must be accepted.
Check fill auger for proper operation and that an adequate grain supply is available to
maintain grain seal.
4. Moisture controller temperature is not stable:
Be sure to allow 2/3 grain pass before starting into Auto control. See operation sections.
Starting Auto Control when grain temperature and Set Point temperature are not nearly equal will
greatly increase the time required to stabilize on set point.
Be sure to pause 5 to 6 seconds in the Off position when switching from Manual to Auto
control to allow controller to reset properly.
Check that the Auto control Unload Rate starts at the same rate as was used in manual
control when first switch to AUTO. If not, suspect problems with the Auto Range Module.
Be patient, grain drying is a slow process. 1-3 hours for a grain pass is not uncommon.
1. Check plenum temperature. Use thermometer inserted at rear of dryer plenum. Plenum tempera-
ture should be near plenum controller set point. Be aware that when drying at temperatures below
those listed in the drying tables, decreased drying capacity will be experienced.
2. Check plenum airflow rate:
Using a static pressure gage calibrated in (inches of water column), check static pressure
in drying plenum. 2.0-2.5 INWC is a typical reading for shelled corn. Consult factory for other grains
or conditions.
Check that all airflow louvers are adjusted properly. See Operations section of manual.
Check that the dryer's perforated walls are clean inside and outside.
Check fill auger for proper operation and that an adequate grain supply is available to
maintain grain seal.
3. Check discharge rate calibration:
Check that the SCR motor control has been properly calibrated. Check motor armature
voltage at maximum and minimum speed as outlined in service section of manual.
Count meter roll RPMs to confirm SCR motor speed is correct and that the proper meter
roll drive parts have been installed. See SCR Meter roll drive chart for proper RPM.
Check for plugged or reduced flow in each column
Weigh a timed discharge from the dryer if discharge rate is still in question.
4. Calibrate Moisture tester:
Be sure moisture tester being used has been calibrated to a certified tester. Check tester
with both wet and dry samples of grain for accuracy. Note that few testers are accurate with very high
moisture grains or when testing hot grain. If required, allow hot grain to cool in an unventilated con-
M O I S T U R E C O N T R O L ( M A N U A L O P E R A T I O N )
M O I S T U R E C O N T R O L ( A U T O M A T I C O P E R A T I O N )
D R Y E R D O E S N O T P E R F O R M T O R A T E D C A P A C I T Y
Summary of Contents for C-2130B
Page 22: ...20...
Page 36: ...34 Fig 6 3 LP vaporizer assembly Fig 6 4 ASC control panel...
Page 49: ...Fig 8 1 Power circuit 220V 3 PH for C 2130B C 2140B C 2160B only 47 4B0280A TIF...
Page 50: ...48 Fig 8 2 Power cirucit 220V Part wind start for C 2175B C 21100 models only 4B0280C TIF...
Page 51: ...49 Fig 8 3 Power circuit 440V 3 PH for all C 2100B models 4B0280B TIF...
Page 52: ...Fig 8 4 Control circuit all models except part wind start p 1 of 3 50 4B0280D TIF...
Page 53: ...Fig 8 4 Control circuit all models except part wind start p 2 of 3 51 4B0280E TIF...
Page 55: ...Fig 8 5 Control circuit part wind start models only p 1 of 3 53 4B0280H TIF...
Page 56: ...Fig 8 5 Control circuit part wind start models only p 2 of 3 54 4B0280I TIF...
Page 58: ...Fig 8 6 Safety circuit portion of control circuit all models 56 4B0280G TIF...
Page 65: ......