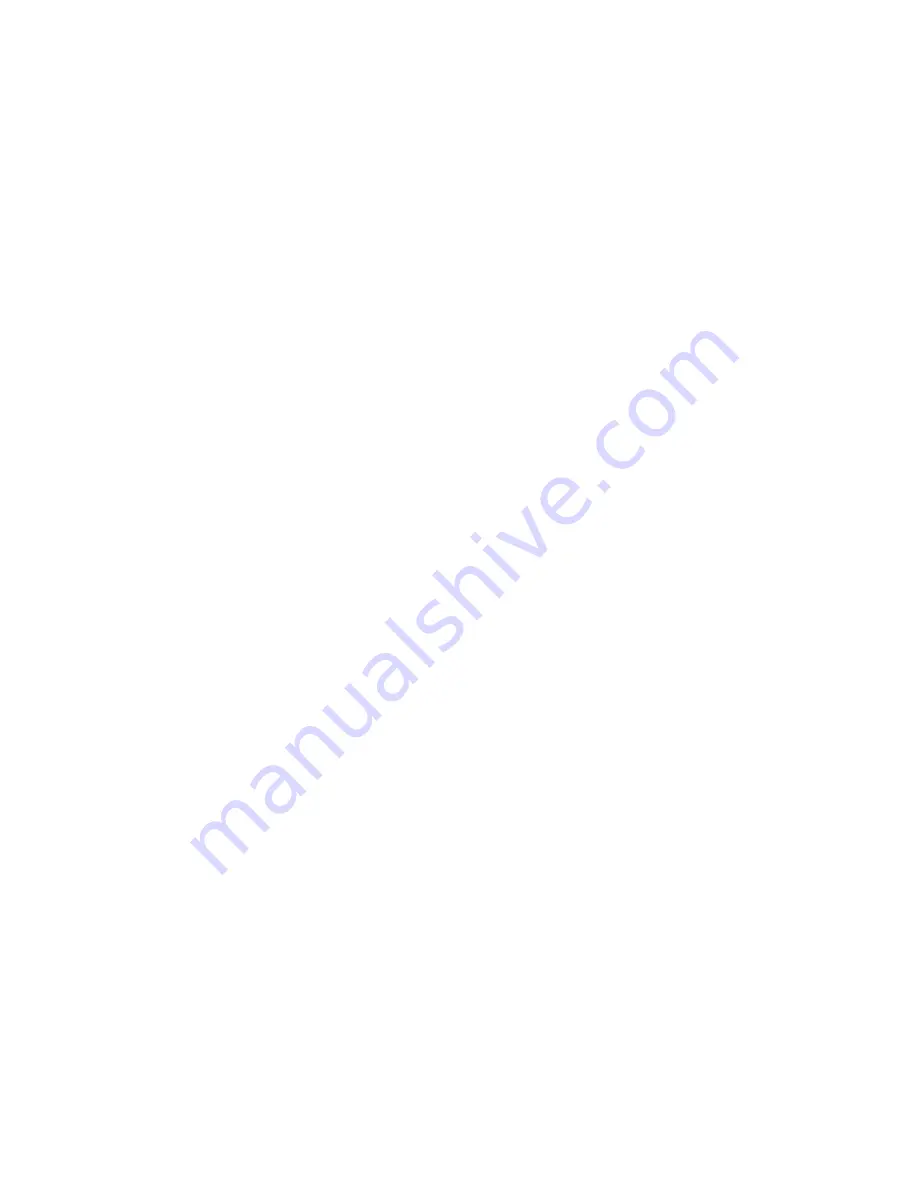
18
trical specifications of this manual. Check for a green
light on the fan start switch, indicating that the blower
pressure has been proven. On models equipped with
part-wind start, the delay timer should be set to 1 to 2
seconds.
NOTE: Pressure may not be adequate to activate the
pressure switch when testing an empty dryer.
Temporarily jump terminals 31 and 32 before proceed-
ing with burner test firing.
11. Burner test firing.
A. Set the Plenum temperature control to 150°F. The
plenum temperature should be reading approximately
ambient temperature at this time.
B. Check to see that the fuel supply hand valves are
on.
C. Preset Modulation Valve Linkage
Check to see that fuel modulating motor arm is starting
from a position near 12 o'clock and that the butterfly
valve linkage is in a nearly closed position (rotated to
the stop counter-clockwise). See Fig. 6-2.
D. Check Flame Guard Lockout
With the blower on, turn the Burner Switch to ON. The
green ENABLED light will come on when the purging
cycle is complete (approximately 15 seconds after
blower pressure has been proven). Do not operate the
safety shutoff valve at this time. In 5 to 15 seconds, the
burner LOCKOUT light will come on and the ENABLED
light will go out. Turn the burner switch OFF and reset
the flame guard lockout by pressing the RESET button
located on the Flame Safeguard control inside the ASC
control box.
E. Ignite Burner
Turn the burner switch ON. When the green ENABLED
light is observed, open the Main/Safety Gas Shutoff
valve. Ignition should occur, the fuel modulator motor
will begin opening the butterfly valve, fuel pressure
should be observed on the pressure gage downstream
of the butterfly valve, and the plenum temperature
should begin to rise.
F. Set Regulator
Observe the pressure on the gage mounted on the
Main/Safety Gas Shutoff valve upstream of the butter-
fly valve. This pressure should be regulated to the
pressures shown in Table 2-1, Fuel Specifications. Set
the regulator to the proper pressure.
NOTE: The regulator pressures specified in the charts
are for maximum BTU rates required. Under drying
conditions with moderate ambient temperatures, lower
than normal drying temperature, or on dryers equipped
with air recirculation, lower regulator settings may be
used.
G. Adjust Low Fire
The plenum temperature controller should stabilize on
the set point temperature after a short time of opera-
tion. Decrease the plenum set point to 100°F to cause
the controller to go to minimum fire position. Adjust the
linkage (rod length) on the butterfly valve to obtain a
1/2 to 1 PSI burner pressure and observe the fire
through the hole in the center of the rear access door.
The fire should appear evenly spread within the burner
baffles.
H. Check High Fire
Increase the plenum temperature controller to 150°F.
The controller should stabilize on the set point after a
short time. While the temperature is climbing, the mod-
ulation motor should drive the butterfly valve to an open
position. At this time, the regulated pressure gage
should be reading nearly the same pressure as the
burner pressure gage. If the burner gage is consider-
ably lower, the butterfly valve is not open enough and
the effective arm length on the modulator motor should
be increased. Make this adjustment when operating in
low fire. Reset low fire adjustment as well.
I. Check Ignition
Turn the burner switch to OFF and allow the modula-
tion motor to return to low fire. Turn the burner switch
ON and open the Main/Safety Gas Shutoff valve.
Verify that the low fire adjustment allows burner to
ignite quickly and reliably. Slightly increase minimum
gas pressure if ignition is slow.
J. Check Burner Control Circuit Shutdown
Turn the unload auger ON and set the Unloading
Switch to Manual. With the burner still operating, turn
fuel supply hand valve OFF. After the burner has
burned down the fuel in the lines, the flame guard con-
trol should go into lockout. This should cause the
unload auger OPERATING light to go off. Within three
minutes, the dryer safety circuit should cause a com-
plete dryer shutdown. Be sure to reset the burner
flame safeguard and open the fuel valves if dryer is to
be refired.
12. Check moisture control operation
A. Set all switches to the positions shown in step num-
ber 1.
B. Start the dryer control circuit, turn the unload auger
to ON, and set the Unloading Switch to MAN position.
Adjust the UNLOADING RATE to 30%.
C. The moisture controller should be reading approx-
imately the same as ambient temperature unless there
is still residual heat in the dryer from previous burner
operation. Set the Moisture Controller to match the
measured temperature displayed.
D. Set the Unloading Switch to AUTO, pausing a few
seconds in the OFF position. The unloading rate
should begin at the previously adjusted manual unload-
ing rate.
E. Increase the moisture controller set point approxi-
mately 30°F above the current measured temperature.
The unloading rate should drop to approximately 2/3 of
the manual unload rate, or 20%.
F. Decrease the moisture controller set point approxi-
mately 95°F below the measured temperature. The
unloading rate will increase to approximately twice the
manual unloading rate, or 60%.
Summary of Contents for C-2130B
Page 22: ...20...
Page 36: ...34 Fig 6 3 LP vaporizer assembly Fig 6 4 ASC control panel...
Page 49: ...Fig 8 1 Power circuit 220V 3 PH for C 2130B C 2140B C 2160B only 47 4B0280A TIF...
Page 50: ...48 Fig 8 2 Power cirucit 220V Part wind start for C 2175B C 21100 models only 4B0280C TIF...
Page 51: ...49 Fig 8 3 Power circuit 440V 3 PH for all C 2100B models 4B0280B TIF...
Page 52: ...Fig 8 4 Control circuit all models except part wind start p 1 of 3 50 4B0280D TIF...
Page 53: ...Fig 8 4 Control circuit all models except part wind start p 2 of 3 51 4B0280E TIF...
Page 55: ...Fig 8 5 Control circuit part wind start models only p 1 of 3 53 4B0280H TIF...
Page 56: ...Fig 8 5 Control circuit part wind start models only p 2 of 3 54 4B0280I TIF...
Page 58: ...Fig 8 6 Safety circuit portion of control circuit all models 56 4B0280G TIF...
Page 65: ......