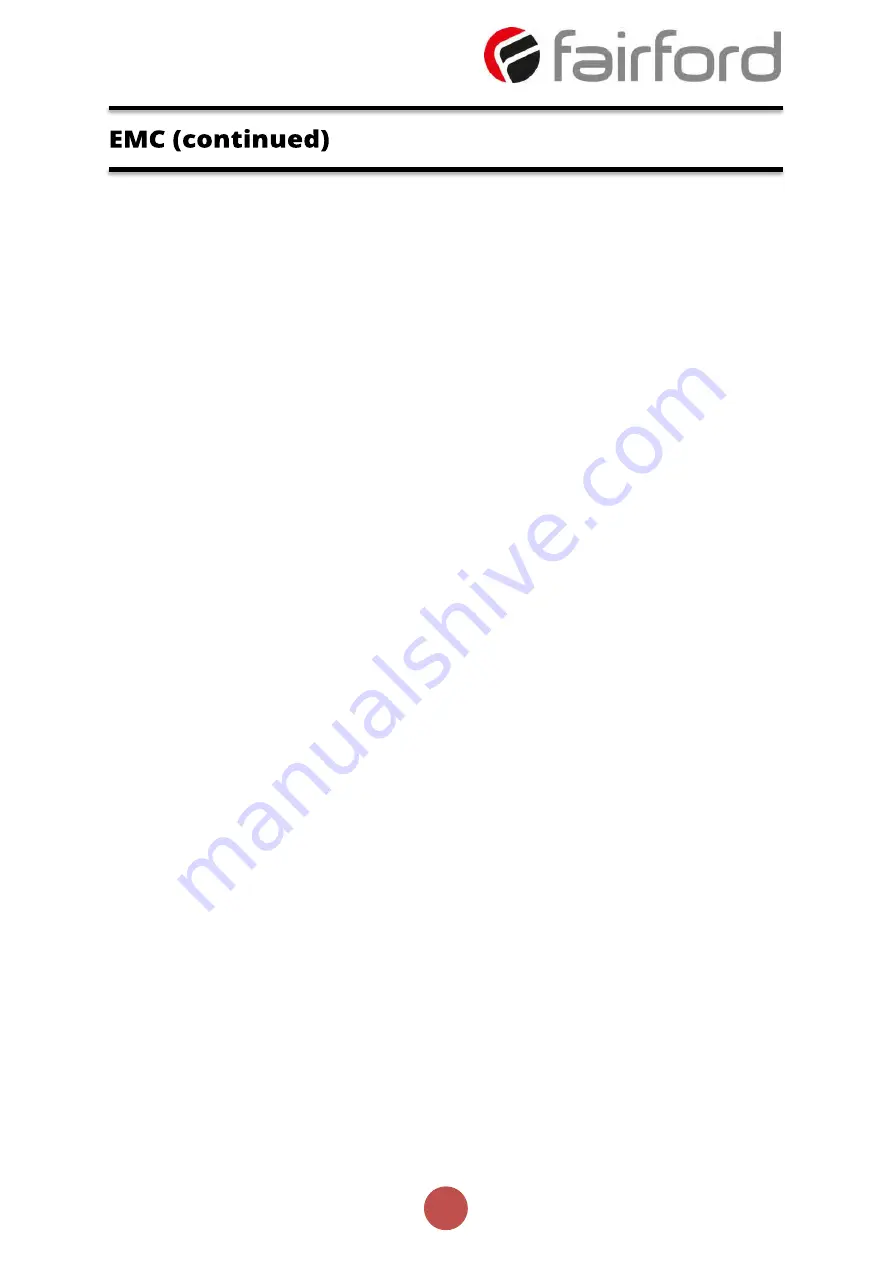
114
agility
TM
Series Soft Start User Manual
MAN-AGY-001. Version 04. 21/09/2018
In the case of an isolated or high impedance grounded system, seek advice from your supplier
before fitting a capacitive high frequency filter to a agility
TM
Soft Starter. It is essential that the
specifying authority, user, or installer has a clear knowledge of the type of network to which the
product is to be installed before making decisions as to which EMC strategy to adopt.
As supplied, all agility
TM
products comply with the conducted emissions requirements for
environment class A as defined by EN 60947-4-2:2012 Table 19. However, the length and type of
cable connecting the motor to the starter module materially affects the level of emissions
generated, and can amplify them greatly. The standard also allows different levels of emissions
depending on rated input power, which also affects the need to fit filters. The EN 60947-4-2:2012
standard only requires consideration of steady-state conditions for EMC emission purposes, and
expressly excludes varying conditions such as those during ramp-up and ramp-down.
Finally, statistics show that the number of disturbances arising from soft starters, operating in a
very wide variety of applications and networks throughout the world, is insignificant. Where
EMC disturbances occur, it is very unlikely that they can be genuinely attributed to a soft starter.
Strategies for Attaining and Maintaining EMC Compliance
Where possible, minimize the effect of electrical interference by using the strategies listed below.
•
Locate the agility
TM
Soft Starter unit as close as reasonably possible to the motor terminal
box in order to minimize cable length.
•
Ensure that, within any enclosure, the control wiring does not run parallel to the power
wiring. Where this is unavoidable, maintain a 100 mm [3.9 in] separation between
control cables and power cables.
•
Where possible, ensure that the control wiring crosses at right angles to the power
wiring. This practice reduces the cross-coupling between cables.
•
Shield any cables carrying sensitive signals. The digital control inputs to a
agility
TM
are
opto-isolated, and do not normally require buffering (e.g. through a small relay) or
shielding.
Where a special purpose system filter has been applied at the point of common coupling,
additional filtering of individual drives is not necessary and may introduce undesirable effects due
to resonance.
For the purposes of EMC, the connections between the agility
TM
controller and motor are
considered to be an extension of the enclosure, and preferably should be contained within
grounded metallic trunking or conduit. Armoured cable may be used providing it is correctly
terminated, although the EMC performance will be slightly inferior. Shielded cable is not
necessary.
All associated electrical and electronic equipment near to the controller complies with the
emission and immunity requirements of the EMC Directive.