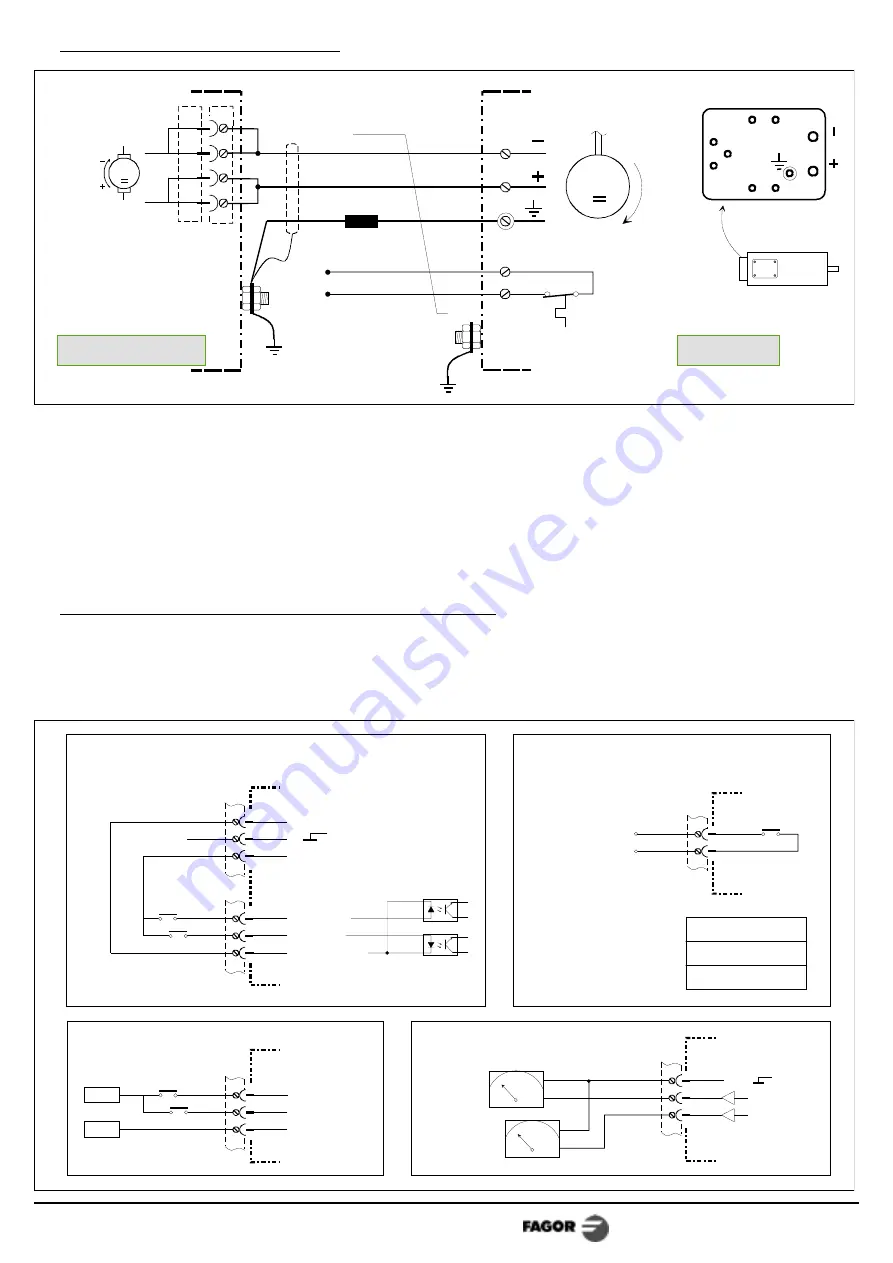
DC Servo Drive System Manual Ver: 0009
DC - 23/32
11
10
12
VELOCITY
CURRENT
Monitoring signals:
Enable signals:
Drive OK signal:
V
V
±10V
±10V
Speed
Cur
rent
14
13
15
SPEED
DRIVE
17
16
DR.OK
To the safety
chain.
COMMON
0 V
24 V
Drive OK: contact
0.6A - 125Vac
0.6A - 110Vdc
2A - 30Vdc
Enable signals using ±10V:
14
13
15
SPEED
DRIVE
COMMON
2
1
3
-10 V
+10 V
Connection of the monitoring and control signals.
Monitoring: The drive 10Vdc at its "velocity" output when, receiving the maximum
command of +10V, the motor turns at the speed which the RTV1 resistor has been calculated for
(usually the motor's maximum speed). The "current" output 10Vdc when the drive
provides its peaks current (table page 10).
Power connection: Drive-Motor.
DC Servodrive
MOTOR
OUTPUT
CONNECTOR
N.C.
Thermal switch
Thermal
M
DC Motor
To emergency
chain.
Clockwise Rotation
at Shaft End. CWR.
DC Motor
Top view.
MOTOR
OUTPUT
M
Ready Made Cable
MPC-4x1.5+(2x1) (DCS-08)
MPC-4x2.5+(2x1) (DCS-14)
Thermo
B
E
BE
(*)
(*)
The Fagor DCS drive has been designed to govern motors with a winding inductance greater
than 2.5 mHr. The FXM 42.30A and 43.30A motors need a coil installed in series.This coil
must never have an inductance value greater than 8 mHr. Fagor offers the coil DC-IND-2/28
(2mHr, 28A) appropriate for these motors.
Warning: A short-circuit between the E- and B+ terminals may cause great damage to the
Drive.