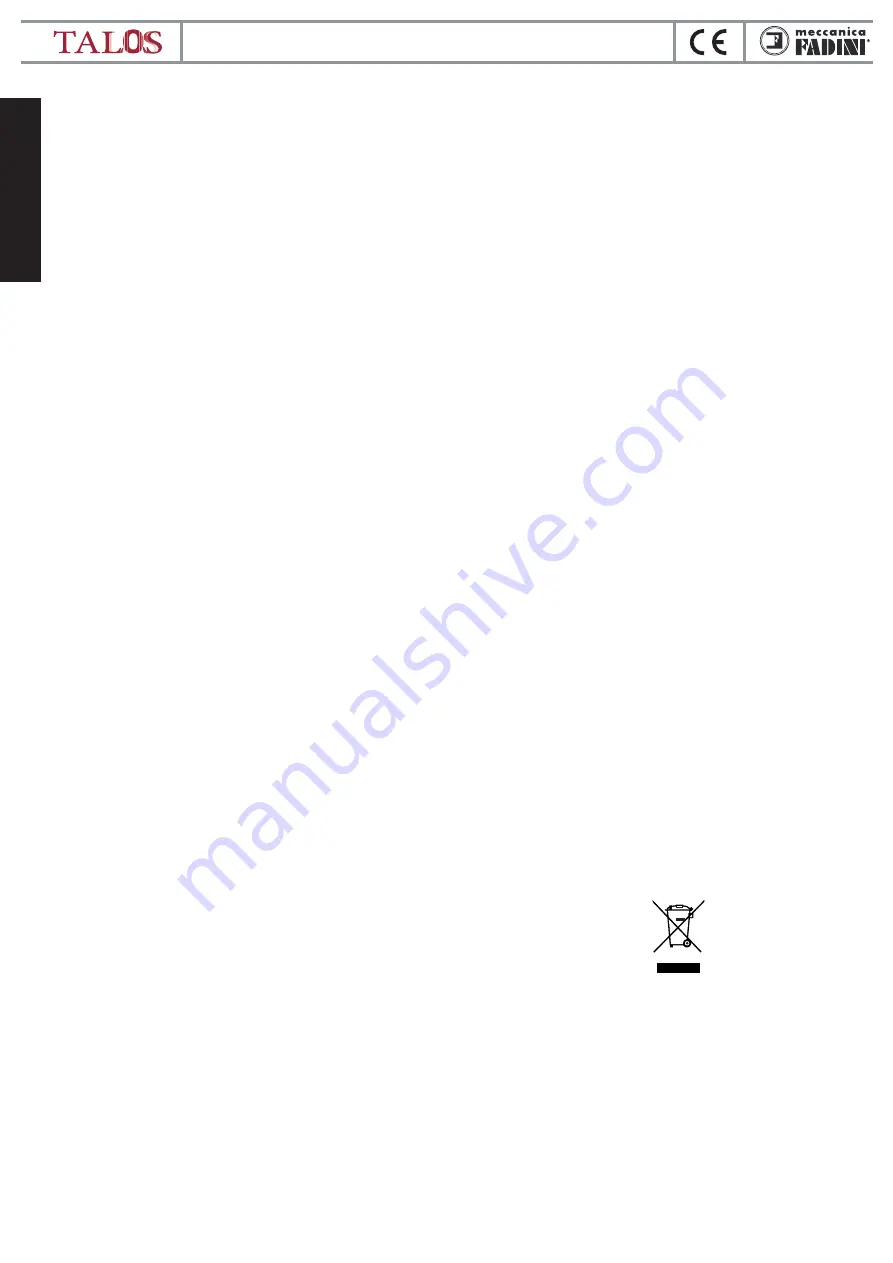
Retractable Oil-hydraulic Bollard
English
GENERAL WARNINGS FOR PEOPLE SAFETY
INTRODUCTION
This operator is designed for a specific scope of applications as
indicated in this manual, including safety, control and signaling
accessories as minimum required with
FADINI
equipment.
□
Any applications not explicitly included in this manual may
cause operation problems or damages to properties and
people.
□
Meccanica Fadini snc is not liable for damages
caused by the incorrect use of the equipment, or for
applications not included in this manual or for malfunctioning
resulting from the use of materials or accessories not
recommended by the manufacturer.
□
The manufacturer
reserves the right to make changes to its products without
prior notice.
□
All that is not explicitly indicated in this manual
is to be considered not allowed.
BEFORE INSTALLATION
Before commencing operator installation assess the suitability
of the access, its general condition and the structure.
□
To check that the ground is stable, to avoid subsequent settling
or deformation in the traffic control post installation area.
□
Make sure that there is no risk of impact, crushing, shearing,
conveying, cutting, entangling and lifting situations, which
may prejudice people safety.
□
Do not install near any source of
heat and avoid contacts with flammable substances.
□
Keep all
the accessories able to turn on the operator (transmitters,
proximity readers, key-switches, etc) out of the reach of the
children.
□
Transit through the access only with stationary
operator.
□
Do not allow children and/or people to stand in the
proximity of a working operator.
□
To ensure safety in the
whole movement area of a bollard it is advisable to install
photocells, sensitive edges, magnetic loops and detectors.
□
Use yellow-black strips or proper signals to identify dangerous
spots.
□
Before cleaning and maintenance operations,
disconnect the appliance from the mains by switching off the
master switch.
□
If removing the actuator, do not cut the
electric wires, but disconnect them from the terminal box by
loosening the screws inside the junction box.
INSTALLATION
All installation operations must be performed by a qualified
technician, in observance of the Machinery Directive
2006/42/CE and safety regulations EN 12453 - EN 12445.
□
Verify the presence of a thermal-magnetic circuit breaker
0,03 A - 230 V - 50 Hz upstream the installation.
□
Use
appropriate objects to test the correct functionality of the
safety accessories, such as photocells, sensitive edges, etc.
□
Carry out a risk analysis by means of appropriate instruments
measuring the crushing and impact force of the main opening
and closing edge in compliance with EN 12445.
□
Identify the
appropriate solution necessary to eliminate and reduce such
risks.
□
In case where the gate to automate is equipped with a
pedestrian entrance, it is appropriate to prepare the system in
such a way to prohibit the operation of the engine when the
pedestrian entrance is used.
□
Apply safety nameplates with CE
marking on the gate warning about the presence of an
automated installation.
□
The installer must inform and instruct the end user about the
proper use of the system by releasing him a technical dossier,
including: layout and components of the installation, risk
analysis, verification of safety accessories, verification of
impact forces and reporting of residual risks.
INFORMATION FOR END-USERS
The end-user is required to read carefully and to receive
information concerning only the operation of the installation
so that he becomes himself responsible for the correct use of it.
□
The end-user shall establish a written maintenance contract
with the installer/maintenance technician (on -call).
□
Any
maintenance operation must be done by qualified technicians.
□
Keep these instructions carefully.
WARNINGS FOR THE CORRECT OPERATION OF THE
INSTALLATION
For optimum performance of system over time according to
safety regulations, it is necessary to perform proper
maintenance and monitoring of the entire installation: the
automation, the electronic equipment and the cables
connected to these.
□
The entire installation must be carried
out by qualified technical personnel, filling in the Maintenance
Manual indicated in the Safety Regulation Book (to be
requested or downloaded from the site
www.fadini.net/supporto/downloads).
□
Operator: maintenance inspection at least every 6 months,
while for the electronic equipment and safety systems an
inspection at least once every month is required.
□
The
manufacturer, Meccanica Fadini snc, is not responsible for
non-observance of good installation practice and incorrect
maintenance of the installation.
DISPOSAL OF MATERIALS
Dispose properly of the packaging materials such as
cardboard, nylon, polystyrene etc. through specializing
companies (after verification of the regulations in force at the
place of installation in the field of waste disposal). Disposal of
electrical and electronic materials: to remove and dispose
through specializing companies, as per Directive 2012/19/UE.
Disposal of substances hazardous for the environment is
prohibited
.
2