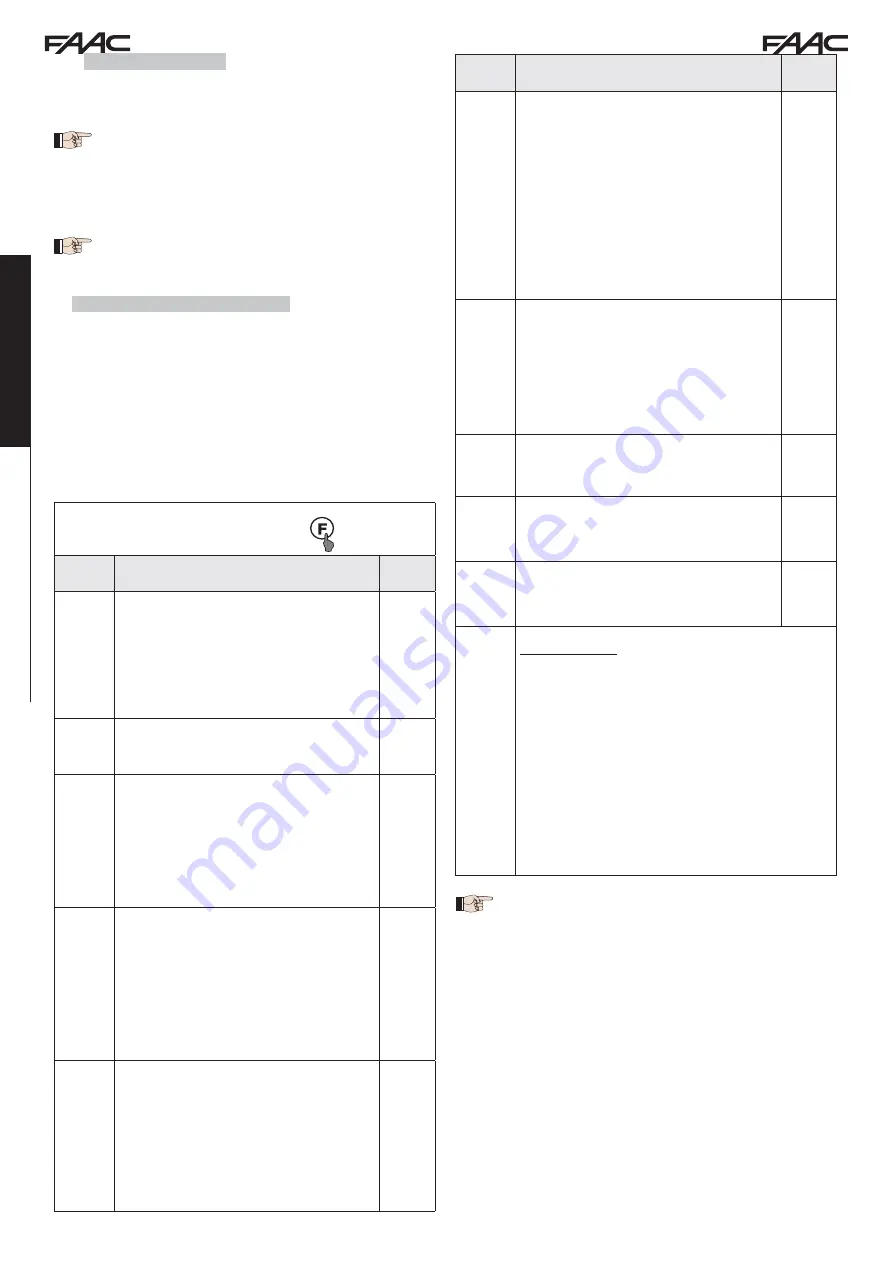
C850
20
532015 - Rev.B
ENGLISH
T
ranslation of the original instructions
11.5 PROGRAMMING
To program automated system operation, you must access “
PROGRAMMING
”
mode.
Programming is divided into three levels:
BASIC, ADVANCED and EXPERT.
Changes to the programming parameters become
immediately effective, while final storage occurs
only upon exiting programming and returning to the
automated system status display. If the equipment
is powered down before returning to the automated
system status display, all changes made will be lost.
It is possible to return to the status display at any point
during programming at any level by simultaneously
pressing “F” and “-”
11.5.1 BASIC PROGRAMMING LEVEL
BASIC PROGRAMMING LEVEL is accessed by pressing F:
•
when pressed (and held) the name of the first function is displayed.
•
releasing the key, the function value is displayed and can be modified
using the
+
and
-
keys.
• when
F
is pressed again (and held) the name of the following function
is displayed, and so on.
•
once the last function is reached, pressing
F
will exit programming
mode and the display will go back to showing the inputs status.
Display
Funzione
Default
L 2
LOOP 2:
When this function is enabled, the loop
connected to the Loop2 input will serve as a
SAFETY / CLOSE function, i.e. it will operate
as a SAFETY during closing and, once it
is uncovered, it will command the board to
CLOSE.
Y
= loop2 active
no
= loop2 not active
Warning:
if the function does not activate, the
state of Loop2 will in any case be available
on one of the duly set outputs (see advanced
programming level).
no
H 1
BOOST LOOP 1 FUNCTION:
Y
= Active
no
= Disabled
This function lets you increase the sensitivity
level at the time of detection. When the vehicle
moves away from the loop, the sensitivity will
return to the selected level. This system makes
it possible to maintain the detection contact
even in case of very tall vehicles or during the
transit of a tractor with trailer.
no
H 2
FUNZIONE BOOST LOOP 2:
Y
= Active
no
= Disabled
See BOOST LOOP1 function.
no
S 1
LOOP 1 SENSITIVITY
Regulates the sensitivity of the loop
01
= minimum
10
= maximum
05
S2
LOOP 2 SENSITIVITY
Regulates the sensitivity of the loop
01
= minimum
10
= maximum
05
St
AUTOMATED SYSTEM STATUS:
Exit programming,
store settings and return to automated system
status display.
00
Closed
01
Pre-
fl
ashing during opening
02
Opening
03
Open
04
Paused
05
Pre-
fl
ashing during closing
06
Closing
07
Stopped ready to close
08
Stopped ready to open
09
Stopped with closing safety devices and then opens
10
Opening safety devices tripped, then opens
Display of the automated system status
S t
is ex-
tremely important for the installation/maintenance
technician in order to distinguish the logical pro-
cesses that the board carries out during movement.
If, for example, the automated system status is
CLOSED, the display MUST read
00
. When the
OPEN command is received, the display will chan-
ge to
0 1
, if pre-flashing is enabled, or directly to
02
(the OPENING movement) to then display
03
once the OPEN gate position is reached.
PROGRAMMAZIONE LIVELLO BASE
Display
Function
Default
dF
PARAMETER LOADING:
00
Neutral
condition
01
FAAC 1 Default loaded
LEAVE ON
00
IF YOU DO NOT WISH TO
CHANGE PROGRAMMING.
For a description of the parameter
dF
refer to
section 11.5.2
.
00
bu
BUS ACCESSORIES MENU
no
= BUS devices entering request
section 11.5.3.
no
LO
OPERATING LOGICS:
A
Automatic
A1
Automatic
1
EP
Semi-Automatic
step-by-step
E
Semi-Automatic
PE
Photocell
automatic
C
Dead-man
CU
Custom
E
PA
PAUSE TIME:
Is effective only if an automatic logic has been
selected. Adjustable from
0
to
59
sec. in
one-second steps.
Next, visualisation changes to minutes and
tenths of a second (separated by a decimal
point) and time is adjusted in 10-second steps
up to the maximum value of
4.1
minutes.
e.g.
: if the display shows
2.5
, the pause time
corresponds to 2 min. and 50 sec.
20
L 1
LOOP 1:
When this function is enabled, the loop
connected to the Loop 1 input will serve as an
OPEN function.
Y
= loop1 active
no
= loop1 not active
Warning:
if the function does not activate, the
state of Loop1 will in any case be available
on one of the duly set outputs (see advanced
programming level).
no