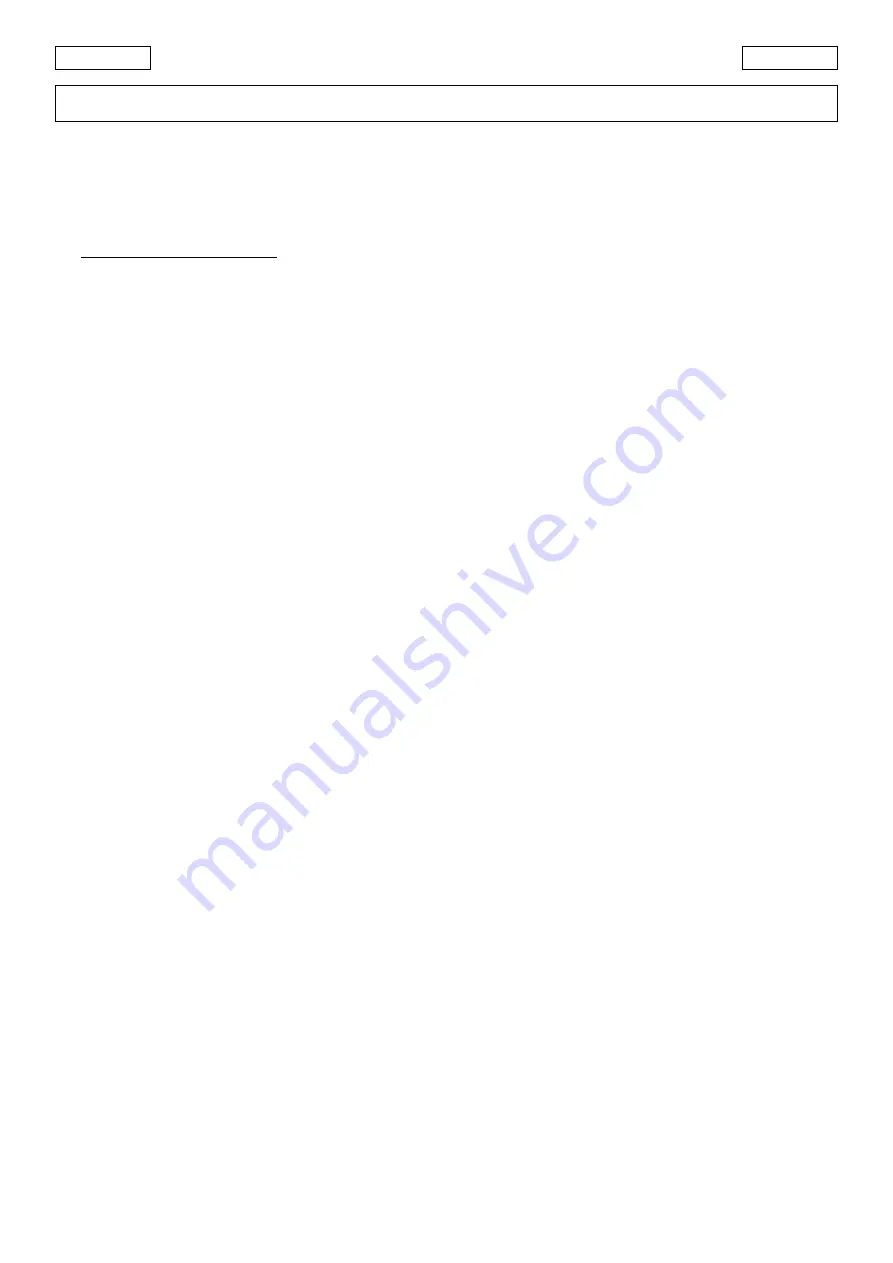
13
ENGLISH
ENGLISH
WARNING FOR THE INSTALLER
GENERAL SAFETY OBLIGATIONS
1) CAUTION! It is important for personal safety to follow all the instructions carefully. Incorrect installation or misuse of
the product may cause people serious harm.
2) Read the instructions carefully before starting to install the product.
3) Packaging material (plastic, polystyrene, etc.) must not be left within reach of children as it is a potential source of danger.
4) Keep the instructions in a safe place for future reference.
5) This product was designed and manufactured strictly for the use indicated in this documentation. Any other not expressly
indicated use may damage the product and/or be a source of danger.
6) FAAC accepts no responsibility due to improper use of the automation or use other than that intended.
7) Do not install the appliance in an area subject to explosion hazard: inflammable gasses or fumes are a serious safety
hazard.
8) Mechanical construction elements must meet the provisions of UNI8612, CEN pr EN 12604 and CEN pr EN 12605
Standards.
To obtain an adequate level of safety in non EU countries, the above mentioned Standards must be observed in addition
to national standards.
9) FAAC will not accept responsibility if the principles of Good Workmanship are disregarded in constructing the closing
elements to be motorised, and if any deformation occurs during use of the said elements.
10) Installation must meet the following Standards: UNI8612, CEN pr EN 12453 and CEN pr EN 12635.
The safety class for the automation must be C+D.
11) Before carrying out any work on the system, switch off the power supply.
12) The mains power supply of the automation must be fitted with a all-pole switch with contact opening distance of 3mm
or greater. Use of a 6A thermal breaker with all-pole circuit break is recommended.
13) Make sure there is a differential switch with 0.03A threshold upstream of the system.
14) Check that the earthing system is correctly made and connect the closure metal parts to it. Also connect the Yellow/
Green wire of the automation to the earthing system.
15) The automation includes an intrinsic anti-crushing device consisting of a torque control which, however, must be installed
together with other safety devices.
16) The safety devices [e.g.: photocells, sensitive edges, etc…] protect any dangerous areas against
Movement mechani-
cal risks
, such as, crushing, dragging, or shearing.
17) Use of at least one indicator-light is essential for each system (e.g.: FAAC LAMP MINILAMP, etc.) as well as a sign
adequately fixed to the frame structure, in addition to the devices mentioned at point “16”.
18) FAAC accepts no responsibility regarding safety and correct operation of the automation, should components made
by manufacturers other than FAAC be used in the system.
19) Use only FAAC original spare parts for maintenance.
20) Do not make any alterations to the components of the automation.
21) The installer must supply full information regarding manual operation of the system in case of an emergency and hand
to the user of the system the “User’s Guide” included with the product.
22) Do not allow children or other persons to stand near the product while in operation.
23) Keep remote controls or any other pulse generator well away from children, to prevent the automation from being
activated accidentally.
24) The user must refrain from attempting to repair or adjust the system personally and should contact qualified personnel
only.
25) Anything not expressly provided for in these instructions is not permitted.