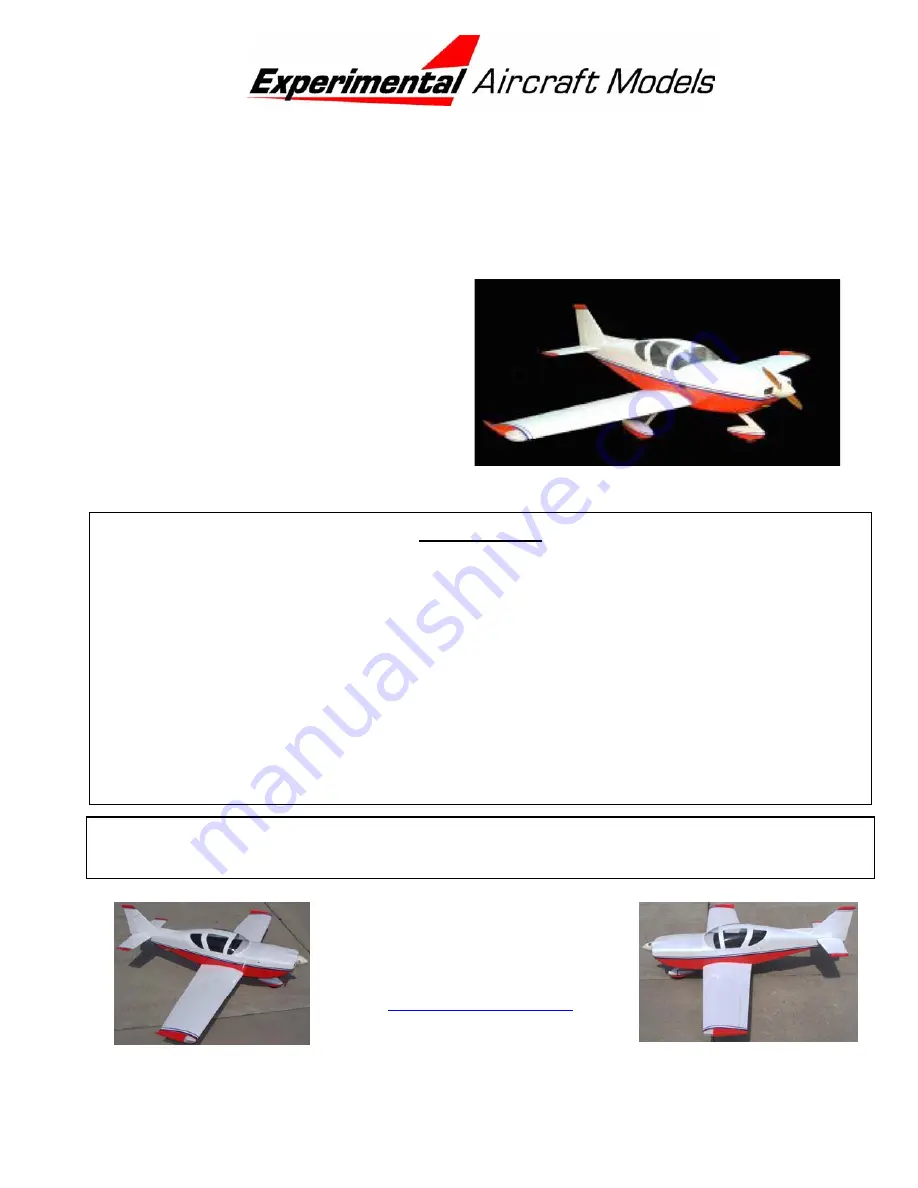
“Enhancing the Homebuilt Experience”
Radio Control Scale Model
Glasair SII / Glasair III
Scale: 1= 3.5 (28% Full Size)
Wingspan: 80” (2032 mm)
Wing Area: 1024 in
2
(66.1 dm
2
)
Flying Weight: 12 lbs (5.04 kg)
Wing Loading: 27 oz/ft
2
Length: 70” (1778 mm)
Radio: 5 Channels with 7 servos
Engines: 1.08 – 1.2 cu in 2 Cycle
1.20 – 1.4 cu in 4 Cycle
Please read this manual thoroughly before starting assembly. It includes critical assembly
instructions and warnings in regards to the safe and enjoyable use of this scale aircraft model.
WARRANTY
Experimental Aircraft Models, LLC (EAM) guarantees this kit to be free from defects in material
and workmanship. The warranty does not cover individual parts damaged by modification or
abuse. In no case will EAM’s responsibility or liability exceed the original purchase price of the
kit. EAM reserves the right to change or modify this warranty at any time.
EAM assumes or accepts no liability for the manner in which this model aircraft is used by the
user, in any condition of assembly. By the act of purchasing this kit, the purchaser and any
subsequent user accepts full responsibility and all resulting liability.
If the purchaser is not willing to accept the above liability associated with the use of this
model aircraft, the purchaser is advised to return this kit immediately to the source from
where it was obtained.
Experimental Aircraft Models LLC
1224 Amber Dr.
Thunder Bay, Ontario
Canada, P7B 6H7
www.rchomebuilts.com