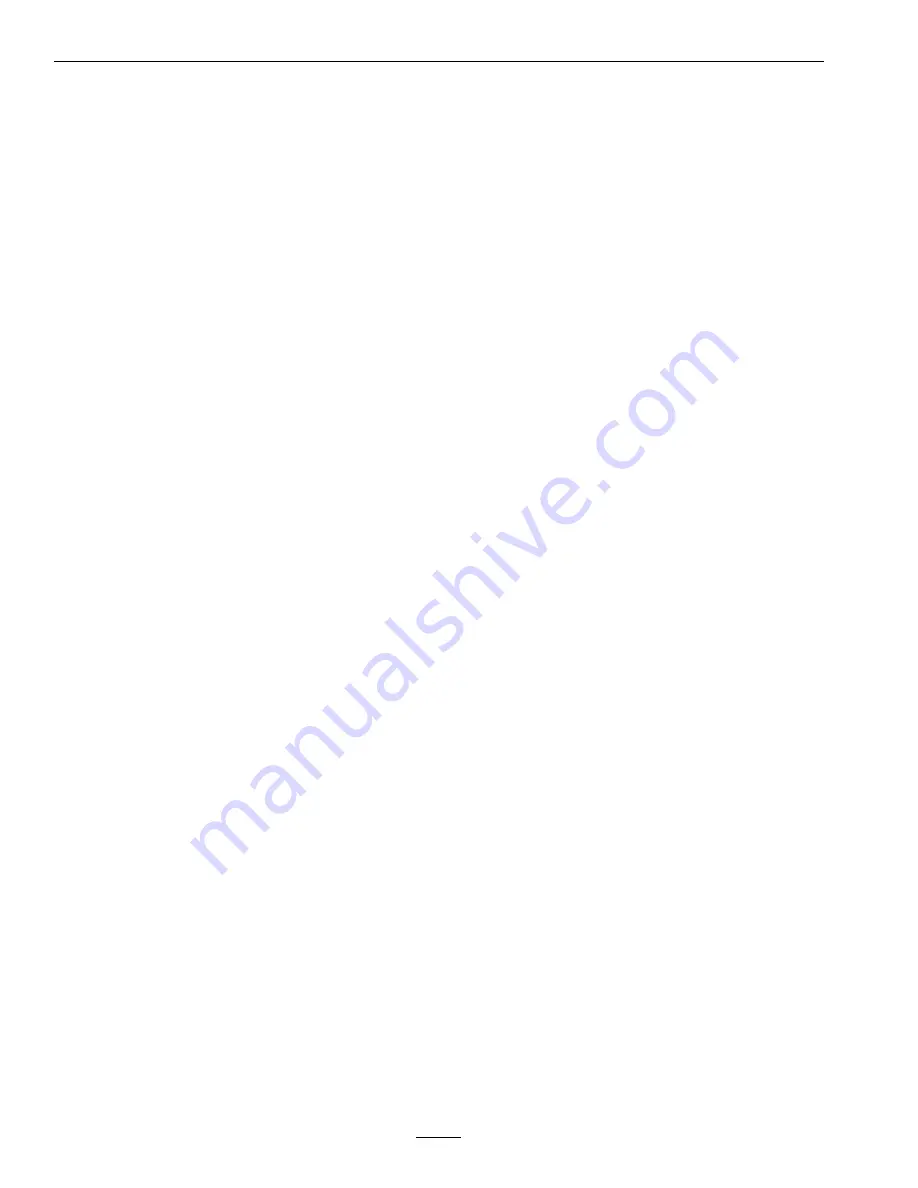
Specifications
Specifications
Systems
Spreader System
•
Maximum Hopper Capacity: 80 lb (36 kg)
•
Spreader Motor: 12VDC variable speed gear
motor
•
Spreader Width: Adjustable from 4ft (1.2 m) up
to 22 ft (6.7 m).
Dimensions
Overall Width:
27 inches (69 cm)
Overall Length:
32 inches (81 cm)
Overall Height:
28 inches (71 cm)
Weight:
70 lb (32 kg)
8