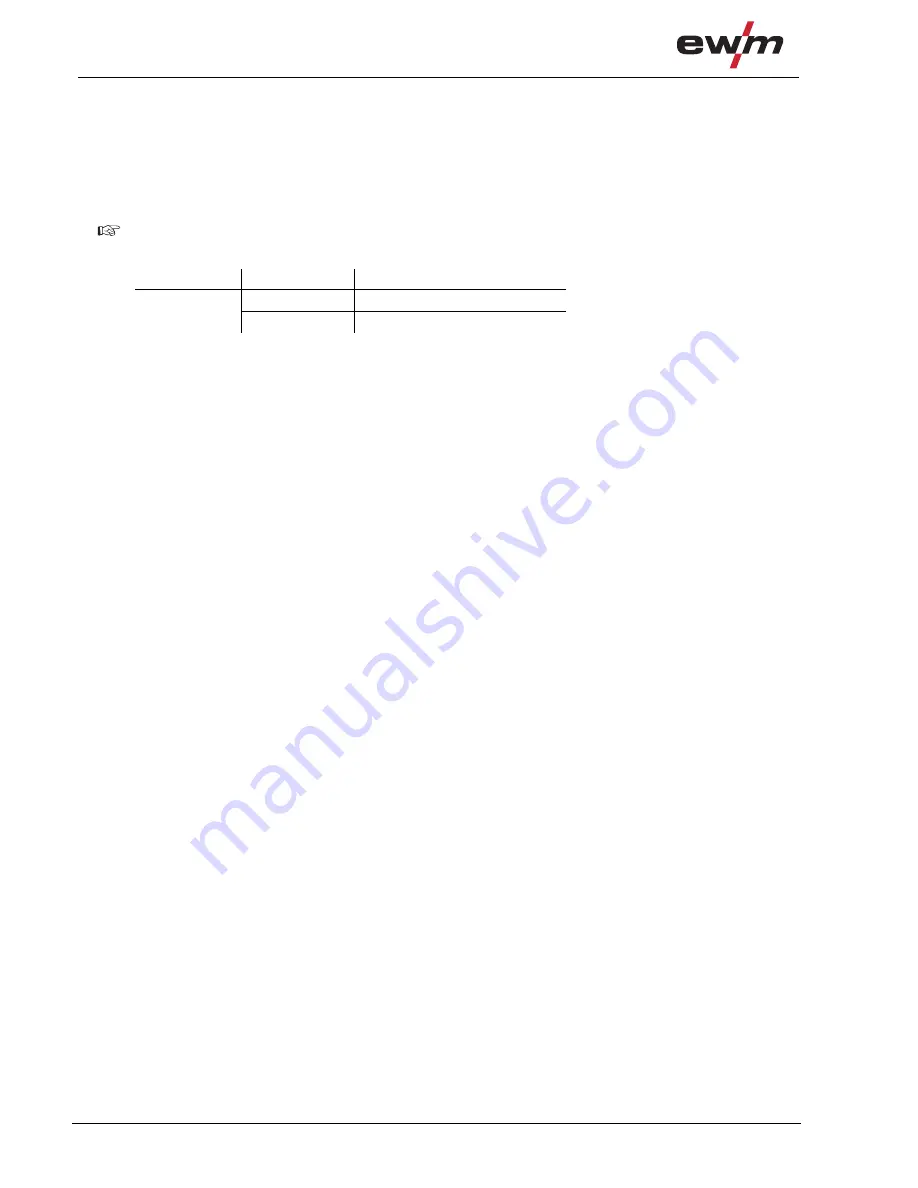
Rectifying faults
Checklist for rectifying faults
80
099-000141-EW501
12.01.2016
7 Rectifying
faults
All products are subject to rigorous production checks and final checks. If, despite this, something fails to
work at any time, please check the product using the following flowchart. If none of the fault rectification
procedures described leads to the correct functioning of the product, please inform your authorised
dealer.
7.1
Checklist for rectifying faults
The correct machine equipment for the material and process gas in use is a fundamental
requirement for perfect operation!
Legend Symbol Description
Fault/Cause
Remedy
Coolant error/no coolant flowing
Insufficient coolant flow
Check coolant level and refill if necessary
Eliminate kinks in conduit system (hose packages)
Reset automatic cutout of the coolant pump by activating
Air in the coolant circuit
Vent coolant circuit - See 7.7 Vent coolant circuit chapter
Functional errors
Machine control without displaying the signal lights after switching on
Phase failure > check mains connection (fuses)
No welding performance
Phase failure > check mains connection (fuses)
Various parameters cannot be set
Entry level is blocked, disable access lock - See 5.18 Protecting welding parameters from
unauthorised access chapter
Connection problems
Make control lead connections and check that they are fitted correctly.
Welding torch overheated
Loose welding current connections
Tighten power connections on the torch and/or on the workpiece
Tighten contact tip correctly
Overload
Check and correct welding current setting
Use a more powerful welding torch
Unstable arc
Material inclusions in the tungsten electrode due to contact with filler material or workpiece
Regrind or replace the tungsten electrode
Incompatible parameter settings
Check settings and correct if necessary