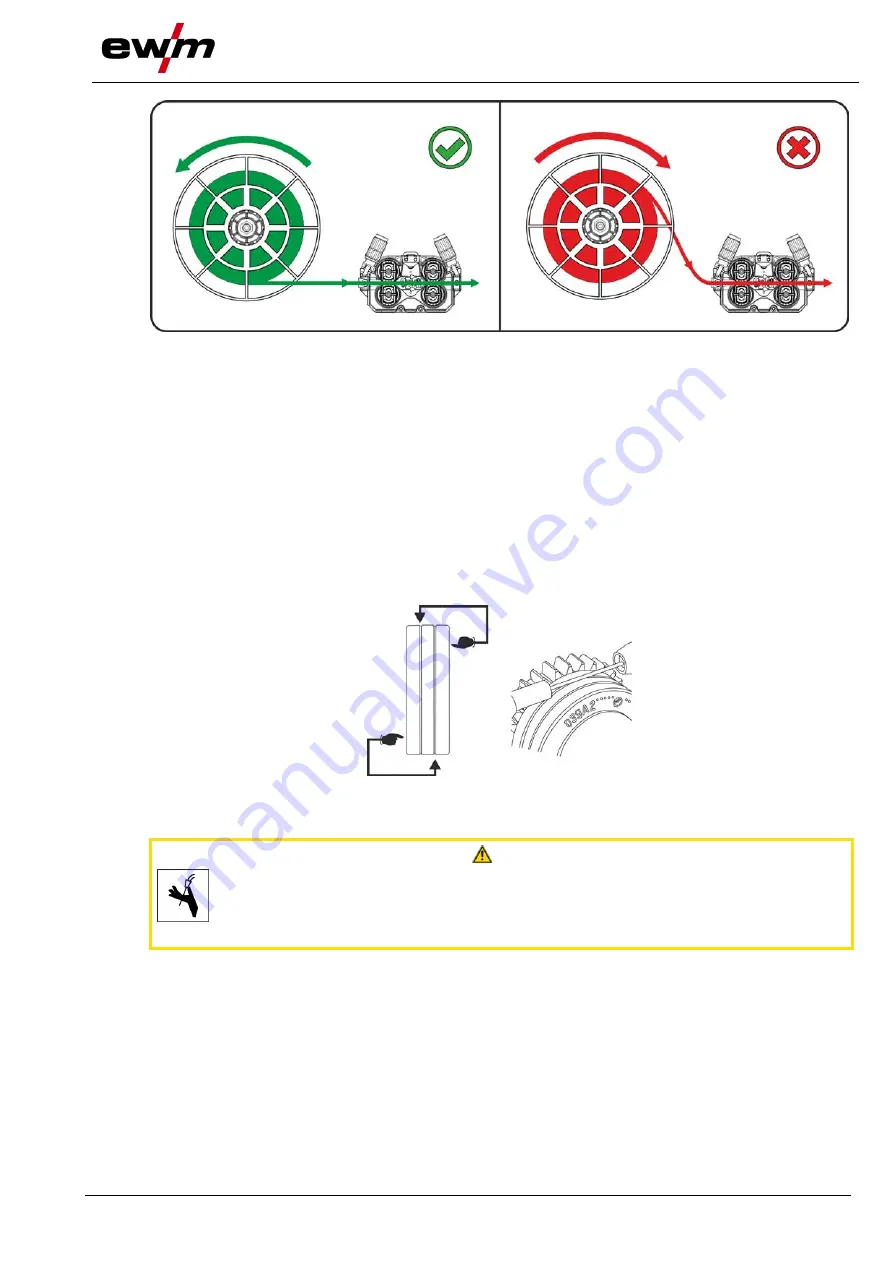
Design and function
Transport and installation
099-004968-EW501
13.09.2021
39
Figure 5-10
Observe the unwinding direction of the wire spool.
5.1.10.2 Changing the wire feed rollers
Poor welding results due to faulty wire feeding! Wire feed rolls must be suitable for the diameter of the
wire and the material.
• Check the label of the rolls whether they fit the wire diameter.
If necessary, turn or change!
• Use V-groove rolls for steel wires and other hard wires.
• Use driven rolls with U-groove for aluminium wires and other soft, alloyed wires.
• Use driven rolls with knurled U-groove for flux cored wires.
• Slide new drive rollers into place so that the diameter of the wire used is visible on the drive roller.
• Screw the drive rollers in place with knurled screws.
Figure 5-11
5.1.10.3 Inching the wire electrode
CAUTION
Risk of injury due to welding wire escaping from the welding torch!
The welding wire can escape from the welding torch at high speed and cause bodily in-
jury including injuries to the face and eyes!
• Never direct the welding torch towards your own body or towards other persons!