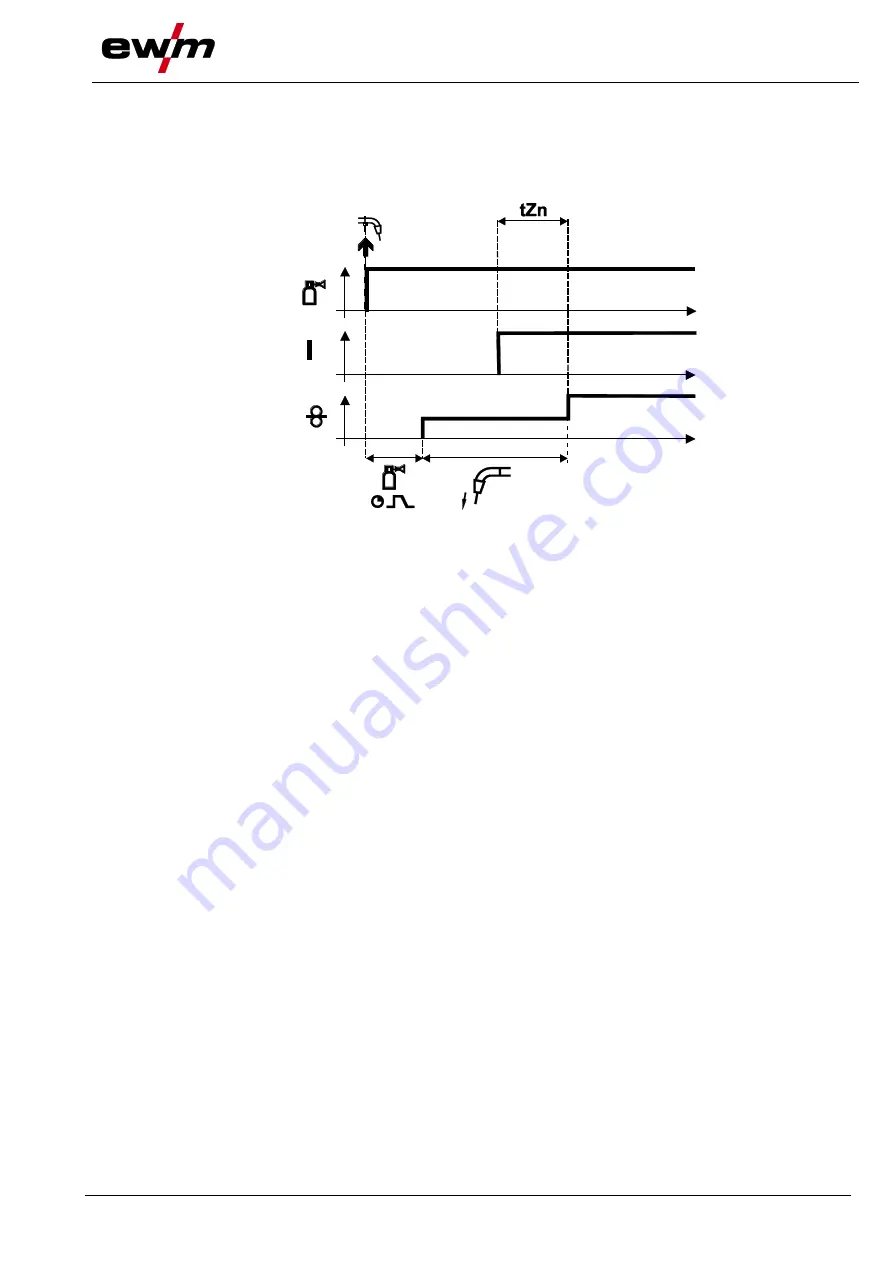
Machine description – quick overview
Machine control – Operating elements
099-004968-EW501
13.09.2021
29
4.3.3.7 Welding parameter ignition time "tZn" diagram
The arc striking is positively affected by the adjustable ignition time. After the arc striking, the wire feeder
continues operating in wire creep speed for the set ignition time. This behaviour occurs whenever the
pause time between the welding operations is at least 1.5 seconds. The ignition time can be set in the
Expert menu using parameter tZn.
Figure 4-9