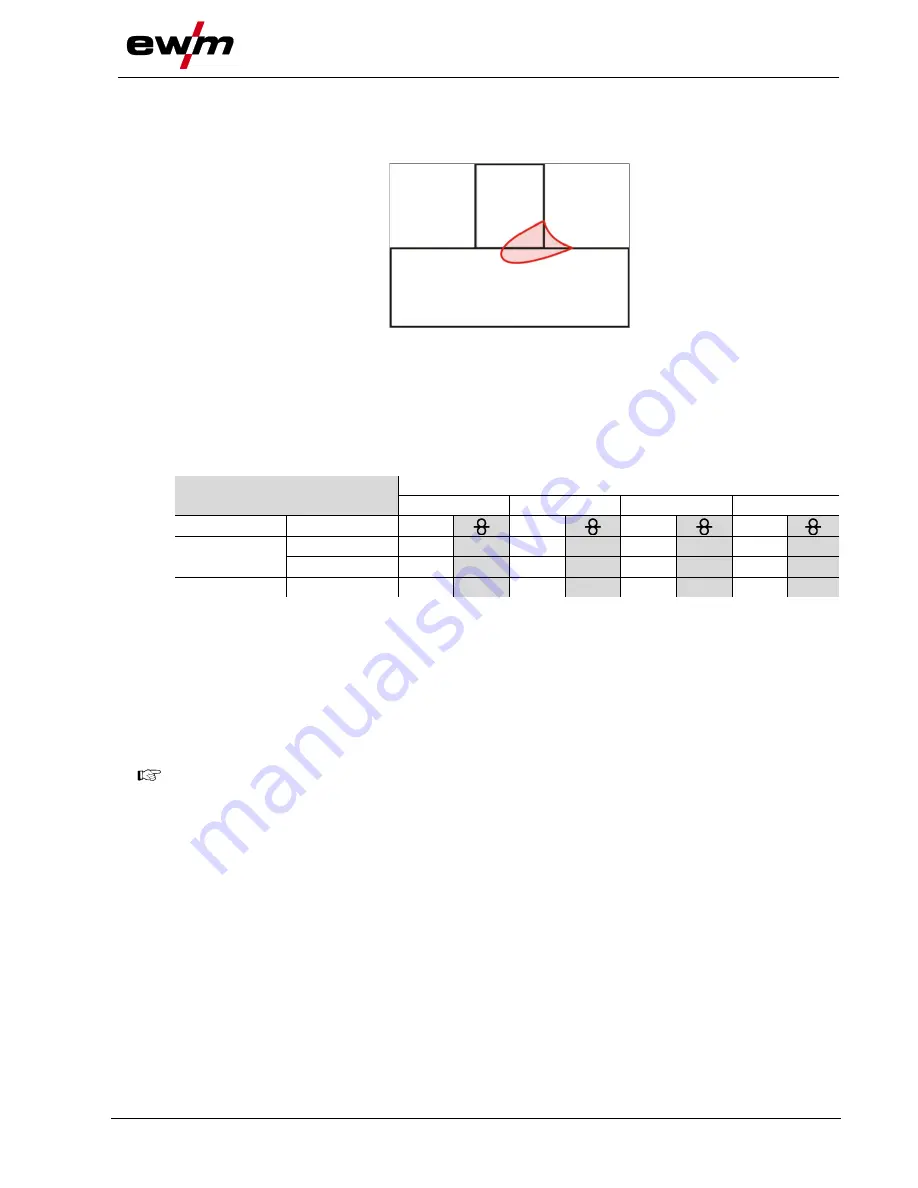
Design and function
MIG/MAG welding
099-005403-EW501
18.08.2016
49
5.3.7
forceArc / forceArc puls
Low-heat, directionally stable and powerful high-performance arc with deep fusion penetration for the
upper power range Unalloyed, low-alloy and high-alloy steels as well as high-tensile fine-grained steels.
Figure 5-26
• Smaller included angle due to deep penetration and directionally stable arc
• Excellent root and sidewall fusion
• Secure welding also with very long stick-outs
• Reduced undercuts
• Un-, low- and high-alloyed steels as well as high-tensile fine-grained building steels
• Manual and automated applications
forceArc welding from:
Wire Ø (mm)
0.8
1
1.2
1.6
Material
Gas
JOB
JOB
JOB
JOB
Steel
Ar 91
–99%
190
17.0
254
12.0
255
9.5
256
7.0
Ar 80
–90%
189
17.0
179
12.0
180
9.5
181
6.0
CrNi
Ar 91
–99%
-
-
251
12.0
252
12.0
253
6.0
You can make use of these properties after selecting the forceArc process.
As with pulse arc welding, it is important to make sure of a good welding current connection.
• Keep welding current cables as short as possible and ensure that cable cross-sections are adequate!
• Fully unroll welding current cables, torche hose packages and, if applicable, intermediate hose
packages. Avoid loops!
• Use welding torches, preferably water-cooled, that are suitable for the higher power range.
• Use welding wire with adequate copper coating when welding steel. The wire spool should have layer
spooling.
Unstable arc!
Welding current cables that are not fully unrolled can cause faults in the arc (flickering).
• Fully unroll welding current cables, torch hose packages and, if applicable, intermediate hose
packages. Avoid loops!