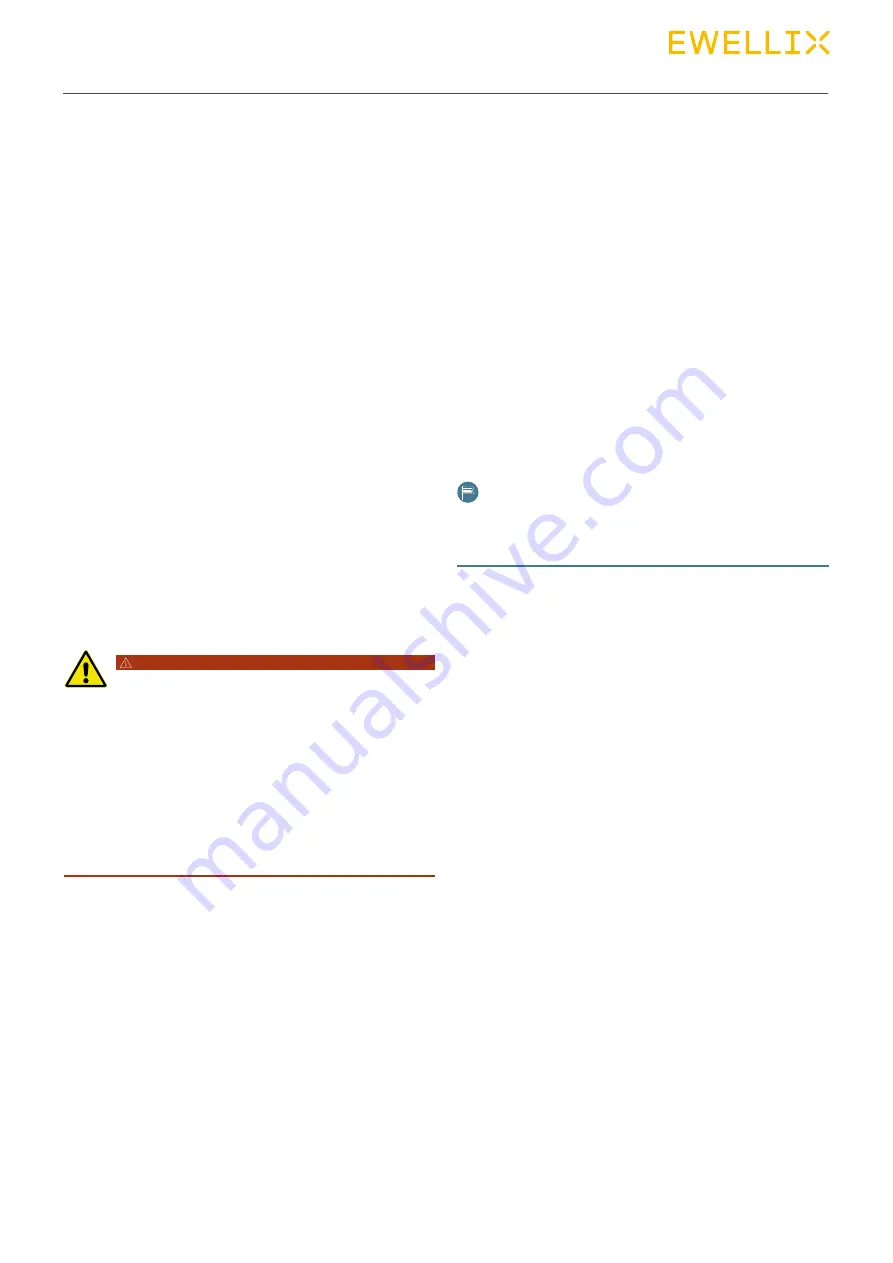
25
9.0 M alfun ction s
9.0 Malfunctions
The following chapter describes potential causes for disrup-
tions and the work that is necessary to restore operation.
In the event of more frequent malfunctions, shorten the
maintenance intervals.
Contact the manufacturer concerning malfunctions which
are not solved by the repair suggestions in the table below;
see service address on the back cover.
Personnel
• Unless indicated otherwise, the work described herein to
solve malfunctions may be performed by the operator.
• Some work may only be carried out by qualified personnel,
which is specifically indicated in the description of the in-
dividual malfunction.
• Work on the electric system may only be performed by ro-
fessional electricians.
DANGER
Risk of injury and material damage due to incorrect
repair of malfunction
The CASM linear actuator is not designed to be repaired by the
customer in most situations. Incorrect repair of a malfunction
may lead to personal injury or material damage.
Therefore:
• Never loosen the screws on the linear actuator or try to open the
linear actuator.
• In the event of a malfunction that cannot be fixed by adhering to
the suggestions in the table below, dismantle the device and send
it to the manufacturer for repair. (⮑ 5 Delivery, packaging and
storage, page 11).
Actions during malfunctions
1. In the event of a malfunction that may present an imme-
diate danger to persons or assets, turn off the actuator.
2. Determine cause of malfunction.
3. Depending on the type of a malfunction, have it repaired
by qualified personnel.
4. Inform responsible party on-site concerning malfunction.
NOTE
The following malfunction table provides information as
to who is authorized to perform the repair and how it is to be
performed.
Summary of Contents for CASM-32
Page 2: ......