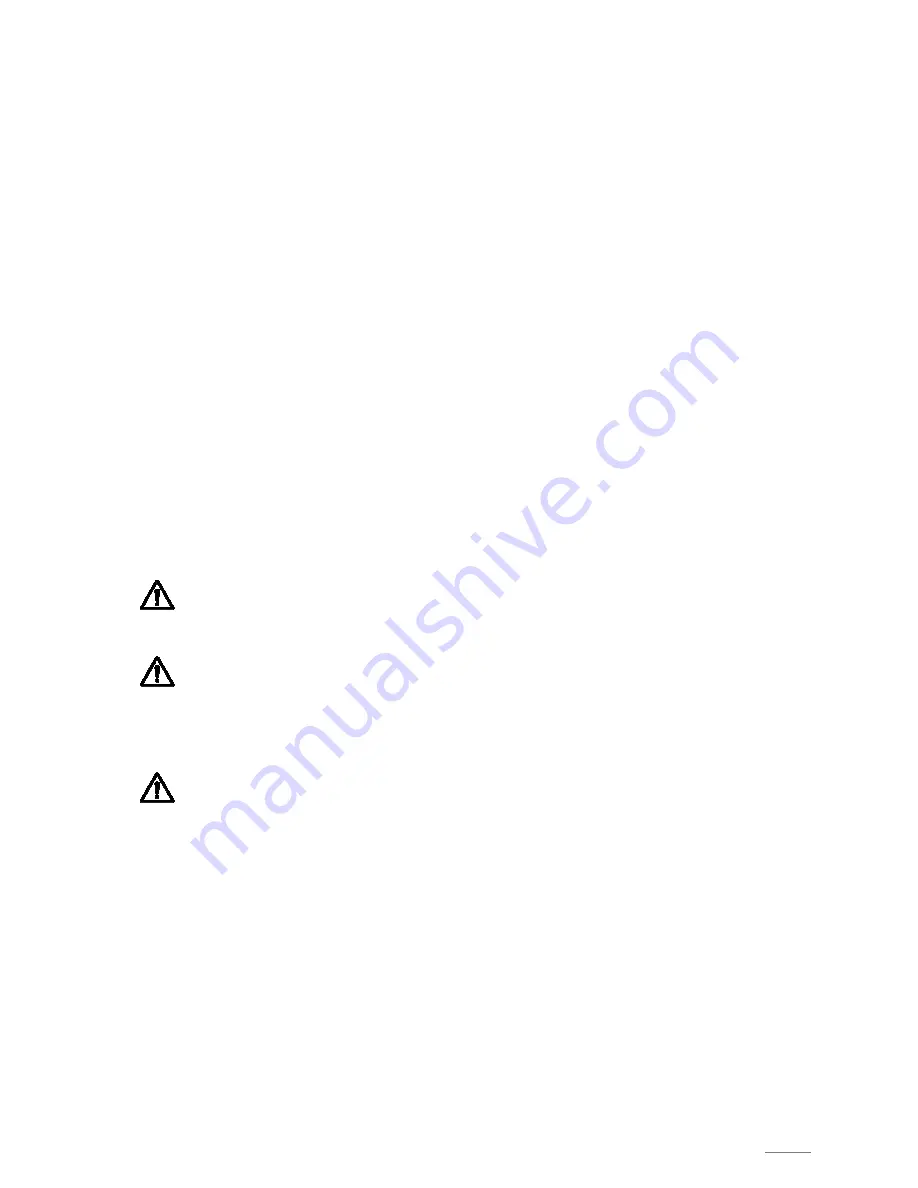
ISSUE 1/Original version/OCT 2013
15
Some materials of low hardness contain abrasive substances leading to rapid cutting edge wear at
high speeds. Feed rates are governed by rigidity of set-up, volume of material to be removed, surface
finish and available machine power.
LUBRICATION
IN HORIZONTAL APPLICATIONS
•
Adjust the fluid flow as required using the flow regulator;
•
Add more cutting fluid if the shavings (metal chips) become blue.
VERTICAL AND OVERHEAD APPLICATIONS
Dip the cutter in cutting paste or apply an appropriate spray.
LUBRICATING THE FEED TRAVEL
The feed travel should be lubricated periodically with grease to ensure smooth operation.
•
Raise the motor unit to the highest position possible;
•
Lubricate the dove-tail guide way at both sides;
•
Lubricate the gear rack.
After repeated use, the gear rack may become loose. If necessary, adjust the 5 self-locking set
screws at the left side. Tighten screws in series until the gear rack moves freely in the dove-tail guide
but does not allow the motor to wobble.
Cleaning
WARNING:
Blow dirt and dust out of the main housing with dry air as often as dirt is seen
collecting in and around the air vents. Wear approved eye protection and approved dust mask
when performing this procedure.
WARNING:
Never use solvents or other harsh chemicals for cleaning the non-metallic parts of
the tool. These chemicals may weaken the materials used in these parts. Use a cloth
dampened only with water and mild soap. Never let any liquid get inside the tool; never
immerse any part of the tool into a liquid.
Optional Accessories
WARNING:
Since accessories, other than those offered by EUROBOOR, have not been tested
with this product, use of such accessories with this tool could be hazardous. To reduce the risk
of injury, only EUROBOOR recommended accessories should be used with this product.
Consult your dealer for further information on the appropriate accessories.