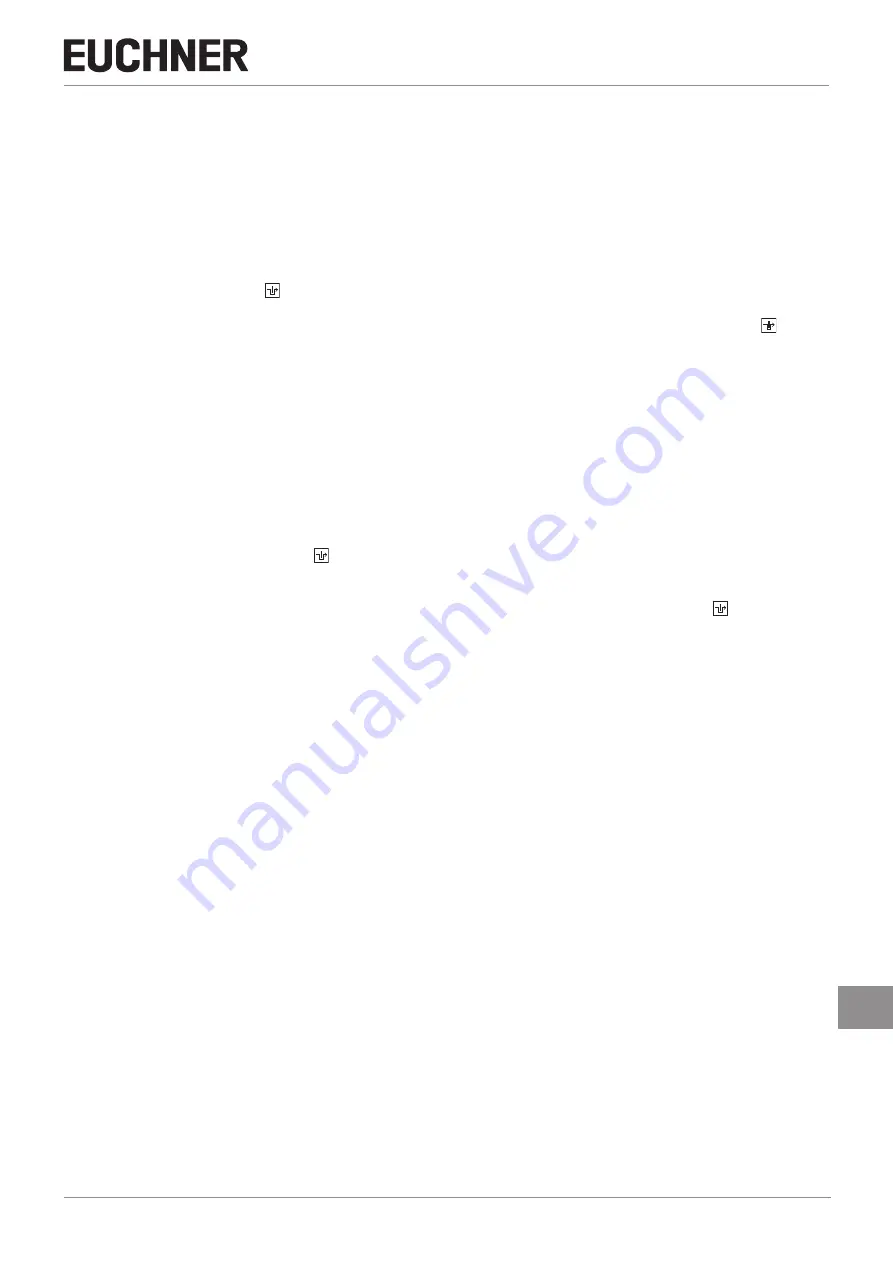
43
2110788-13-03/20 (Translation of the original operating instructions)
Operating Instructions
Transponder-Coded Safety Switch CET.-AR-…
EN
13.1.1. Typical system times
Please refer to the technical data for the exact values.
Ready delay
: After switch-on, the device carries out a self-test. The system is ready for operation only after this time.
Turn-on time of safety outputs
: The max. reaction time t
on
is the time from the moment when the guard is locked to the
moment when the safety outputs switch on.
Simultaneity monitoring of safety inputs IA/IB
: If the safety inputs have different switching states for longer than a
certain time, the safety outputs (OA and OB) will be switched off. The device switches to the fault state.
Risk time according to EN 60947-5-3
: If an actuator moves outside the actuating range, the safety outputs (OA and
OB) are deactivated at the latest after the risk time.
If several devices are operated in a series connection, the risk time of the overall device chain will increase with each device
added. Use the following calculation formula:
t
r
= t
r, e
+ (n x t
l
)
t
r
= Total risk time
t
r, e
= Risk time of single device (see chapter
t
l
= Runtime extension per device (see chapter
)
n = Number of additional devices (total number -1)
Discrepancy time
: The safety outputs
(OA and OB) switch with a slight time offset. They have the same signal state no
later than after the discrepancy time.
Test pulses at the safety outputs
: The device generates its own test pulses on the safety outputs (OA and OB). A
downstream control system must tolerate these test pulses.
This can usually be set up in the control systems by parameter assignment. If parameter assignment is not possible for your
control system or if shorter test pulses are required, please contact our support organization.
The test pulses are also output when the safety outputs are switched off.