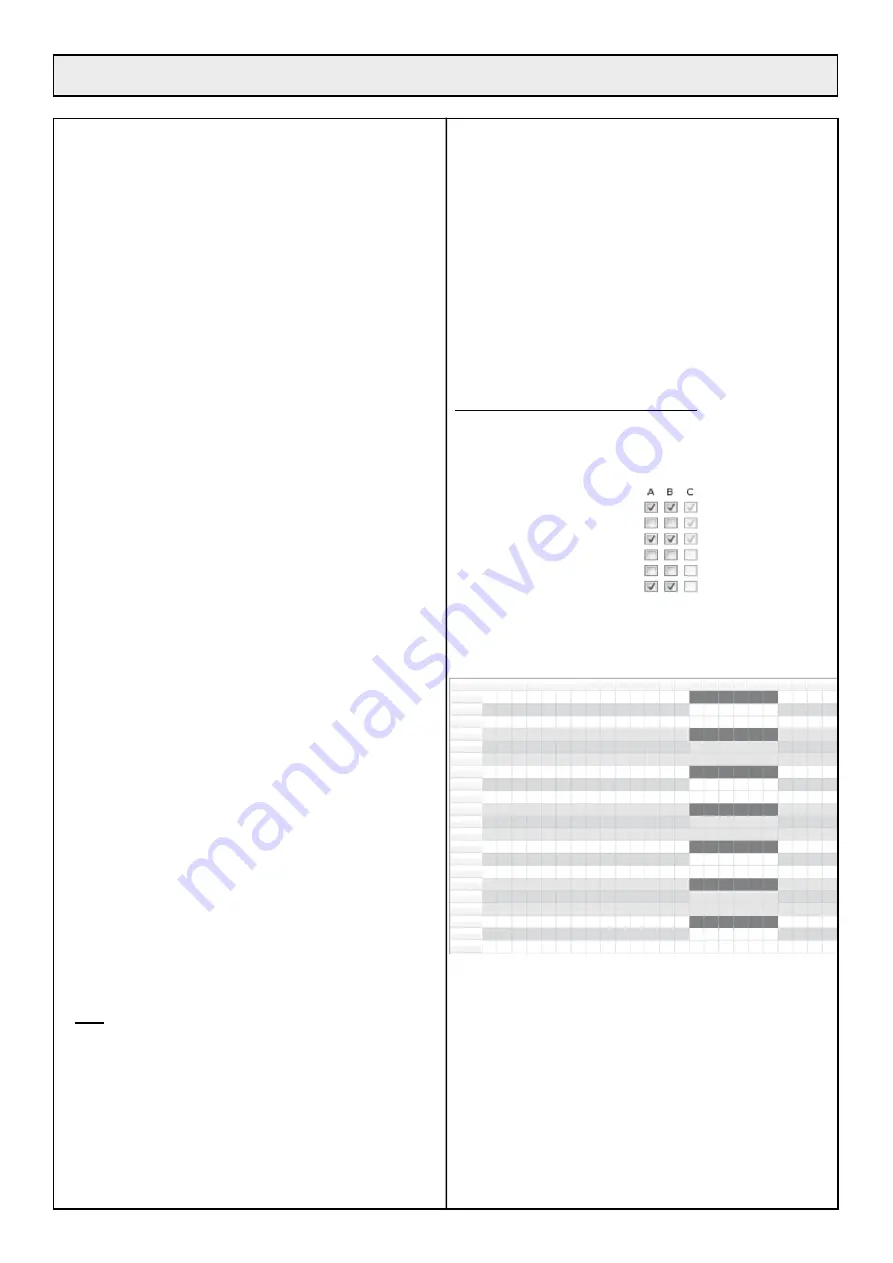
29
6•2•2 DESCRIPTION OF THE PARAMETERS /
OPTIONS
They allow the user to control the algorithm used by the robot to
define its work zone. The other parameters / options and the menu
navigation method are described in chapters 4•5, 6•4 and 6•5.
6•2•3 REST AT STATION FOR SEVERAL CYCLES
(BACKHOME OPTION 2, F2 BUTTON)
Station rest (backhome = on charge) has priority over all other
options and a robot for which option O2 has been enabled will rest at
the station permanently until a new order is received from the user.
So this option applies globally across all zones (A, B and C).
Sending a ‘Backhome’ SMS (Track&Trace manual) enables the O2
option and forces the robot to stay at the station. Sending a ‘Restart’
SMS disables the O2 option and allows the robot to work. It is the
other parameters / options described below which affect how the
multizone robot behaves.
6•2•4 “ACTIVE ZONE” OPTION (OPTION 17)
A machine never works in a zone if the zone has been disabled.
This option O17 is considered as a 2nd priority (after option O2
backhome) in the algorithm which decides which zones the robot will
work on.
If the machine is working in a zone and a user disables it, the
machine returns directly to the station. This amounts to a return to
station (step 1 of the figure 1).
If the machine is in the station and decides to leave, it will never select
a zone which has been disabled by the user (step 5 of the figure 1).
The possible values for option 17 are:
Option 17 (Zone X) = 0: Zone X (X=A, B or C) is disabled.
The machine does not work in zone X. Even if a zone is disabled,
all the parameters, options and resting times relative to this zone
are stored in the robot’s memory. So when the zone is re-enabled
(Option 17 =1), there is no reprogramming to do.
Sending a ‘Disablezone X’ SMS (X = A, B or C) is equivalent to set-
ting option 17 to a value of 0.
Option 17 (Zone X) = 1: Zone X (X=A, B or C) is enabled.
Sending an ‘Enablezone X’ SMS (X = A, B or C) is equivalent to
setting option 17 to a value of 1.
6•2•5 REST TIME AND “NO RESTS” OPTION
(OPTION 15)
A machine never works in zone X (X= A, B or C) if:
The current time is part of a rest time programmed for zone X. It
should be noted that the rest times can be programmed for each
zone and verified via DTS (DTS5.x or DTS6.X) that the rest times
are those required for each of the zones.
AND
the rest times for zone X are enabled (Option 15 (ZoneX)=0).
The active periods of time are considered as a 3rd priority (after
option O2 backhome and option O17 zone active) in the algorithm
which decides which zones the robot will work on.
If the machine is working in a zone and an active period for this zone
is about to start, the machine returns to the station.
If the machine is due to leave the station and an active period for the
zone is under way (or due to start within 10 minutes), the machine
will not select this zone for the next mowing cycle.
The possible values for option 15 are:
Option 15 (Zone X) = 0: The rest times programmed for
zone Z are active, i.e. the robot takes them into consideration
and cannot work in zone X during these periods.
Sending a
‘TimerOn’ text is equivalent to setting option 15 to 0 for all the
zones (A, B and C). Sending a ‘TimerOn X’ SMS (X = A, B or C)
is equivalent to setting option 15 to 0 for Zone X alone.
Option 15 (Zone X) = 1: The rest times programmed for zone
X are disabled, i.e. the robot does not take into consideration
the rest times for zone X and can work in this area at any time.
Even if the periods are disabled, the programming is stored in the
robot’s memory and all that is required to reactivate them is to set
option 15 to 0. The periods do not need to be programmed again.
Sending a ‘TimerOff’ text is equivalent to setting option 15 to 1
for all the zones (A, B and C). Sending a ‘TimerOff X’ SMS (X =
A, B or C) is equivalent to setting option 15 to 1 for Zone X alone.
Example use of rest time in multizone mode:
Let’s consider a multizone installation with 2 zones: zone A and zone B.
Using the keyboard, the user has programmed options 15 and 17 as
follows (DTS6.X screen capture):
O10 - CCWSeek
O11 - Chge2Sides
O13 - Udocking
O14 - Back Along Wire
O15 - No Rests
O17 - Enable Zone
The two zones A and B are active (Option 17 = 1) and the rest times
for the two zones A and B are active (Option 15 = 0). The time
periods for the two zones in question have been programmed using
the keyboard based on the system below (DTS6.x screen capture):
Rest time
Rest time
Rest time
Rest time
Rest time
Rest time
Rest time
00h
Monday
Tuesday
Wednesday
Thursday
Friday
Saturday
Sunday
01h 02h 03h 04h 05h 06h 07h 08h 09h 10h 11h 12h 13h 14h 15h 16h 17h 18h 19h 20h 21h 22h 23h
Every day, between 14:00 and 20:00, a rest period has been defined
for zone A (black bars above). Given that the periods are activated
for this zone (Option 15 (zoneA)=0), the robot will not go into zone
A between 14:00 and 20:00. During this period, it will work conti-
nuously in zone B which does not have an active period between
14:00 and 20:00.
In the same way, between 20:00 and 14:00, the robot will only work
in zone A because it cannot work in zone B (rest time and option 15
(ZoneB) = 0).
In the example above, the time periods are mutually exclusive. So at
any time, the robot can only choose one of the two zones to work in
and applying P10 parameters (the value of P10 parameters) has no
influence on where the robot works.
6• MULTIZONE OPTION
Summary of Contents for ET MOWER ETM105
Page 1: ...ETM105 ET MOWER GB Original user manual Please read carefully before using your machine...
Page 5: ...5 1 KEY TO DIAGRAMS...
Page 14: ......
Page 16: ...11 17 17 7b 6b 6a 7a 8 9 7c 10 10a 10b 10c 10d 11a 16 2 PICTURES...
Page 17: ...12 13 19 17 15 16 14 18 17 2 PICTURES...
Page 18: ...28 27 26 25 24 23 22 20 21 30 29 31 18 67 cm 67 cm 2 PICTURES ETBA...
Page 39: ......
Page 55: ...ETESIA SERVICE GARANTIE 13 rue de l Industrie 67165 WISSEMBOURG CEDEX France Stamp here please...