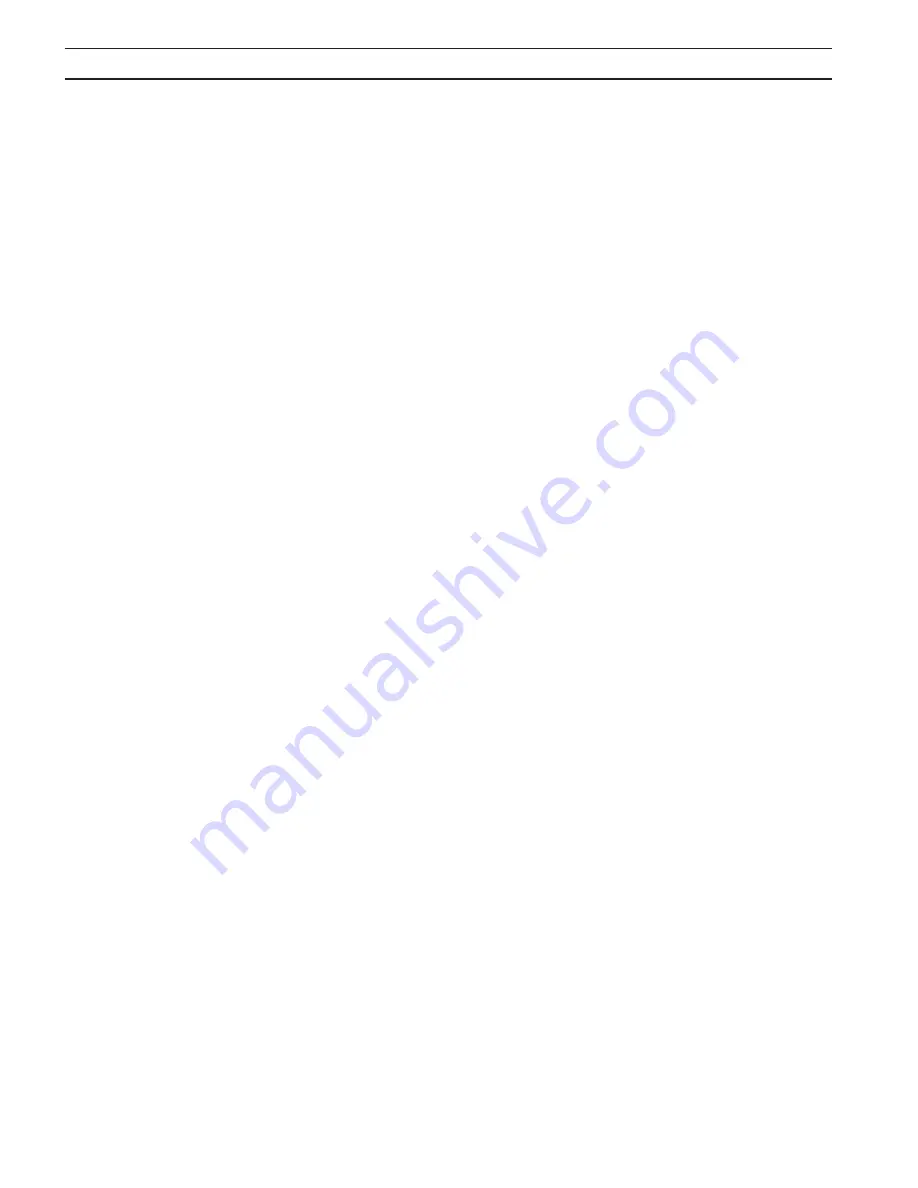
188
SECTION
TITLE
PAGE
PArAGrAPH
SECTION 4
MAINTENANCE ........................................................................................................... 363
4.0
General ....................................................................................................................................................... 355
4.1
Inspection and Cleaning ...................................................................................................................... 355
4.2
Common Cutting Problems ................................................................................................................ 356
4.3
IGBT Handling & Replacement........................................................................................................... 357
SECTION 5
TrOUBLESHOOTING .................................................................................................. 367
5.0
Troubleshooting ..................................................................................................................................... 359
5.1
Troubleshooting Guide ........................................................................................................................ 360
5.2
Reference Voltage Checks ................................................................................................................... 364
5.3
Sequence of Operation ........................................................................................................................ 365
SECTION 6
rEPLACEMENT PArTS ................................................................................................ 379
TABLE Of CONTENTS
Summary of Contents for POWERCUT-1250
Page 7: ...191 POWERCUT 1250 1500 MANUAL PLASMARC CUTTING PACKAGE ...
Page 8: ...192 ...
Page 14: ...198 section 1 description ...
Page 27: ...211 POWERCUT 1250 1500 MECHANIZED PLASMARC CUTTING PACKAGE ...
Page 28: ...212 ...
Page 40: ...224 section 2 installation ...