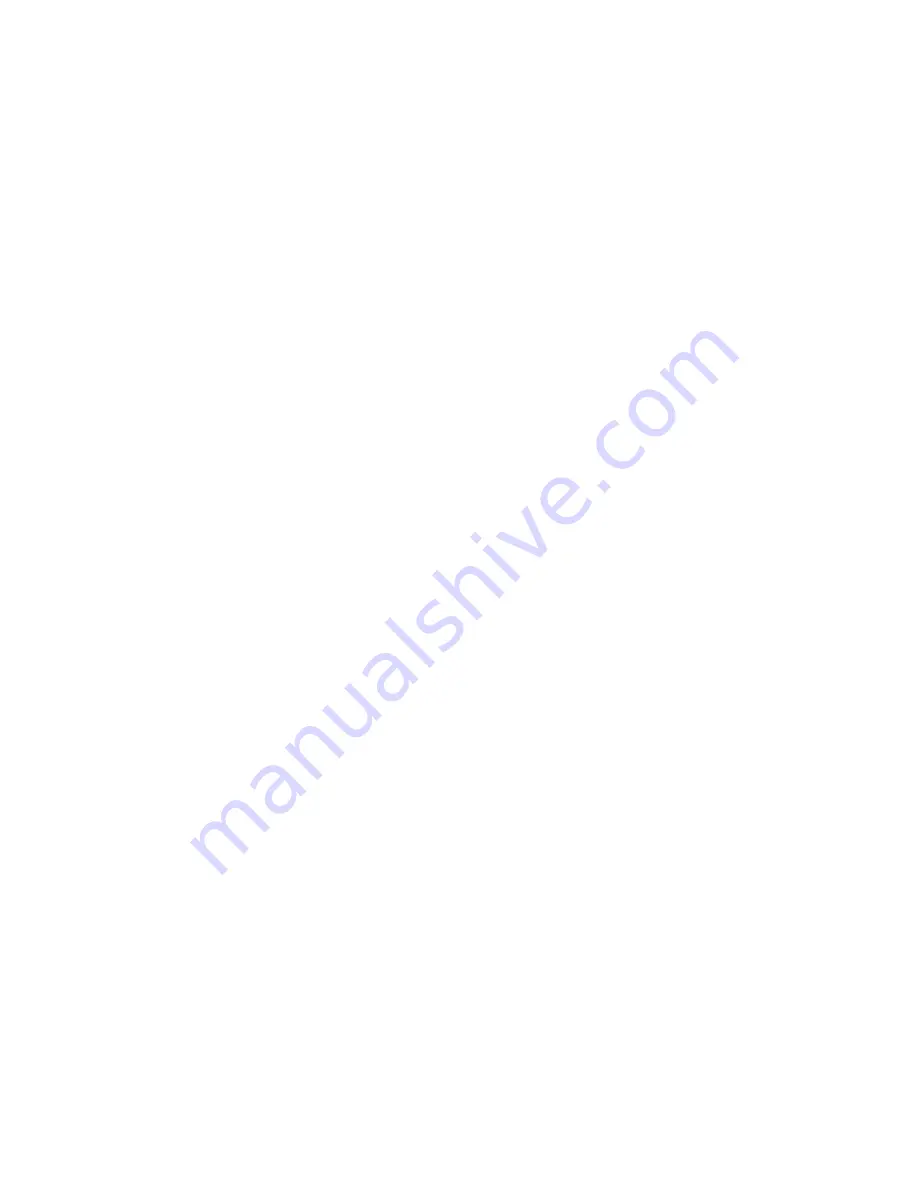
35
Overview test
Each block consist of at least two serviceable parts. The first step of control is taking overview and
checking if any parts are looking abnormal. Broken parts can have marks of thermal damage, change
of colors or shape. If after that checking nothing was find out next step is electrical testing.
Rectifier test
The first part for test is input rectifier consisted of diodes and two heatsinks (details no 15). One
heatsink is on positive potential and second on negative one. For checking diodes following steps can
be achieved:
1. Use measuring instrument with semiconductor conduction test possibility. Connect one
terminal to one phase AC input ( detail no 9) and second to front (opposite side to AC
terminals) heatsink (detail no. 15). If diode is conducting from AC to heatsink, replace
measuring terminals and check if diode is blocked. If so, diode is working properly in this
phase.
2. Next check second diode in this phase by opposite side conduction test. Diode can conduct
from heatsink to AC terminal. If so diode in this phase is working properly.
3. If diode is short circuited or non conducted in both sides it means diode is broken and its
replace is necessary. Diode is screwed into aluminum heatsink and has to be carefully
removed and new one screwed with torque 10Nm/90lb.in
4. Repeat that test in other phases.
Important note
- in case of damage any diode replace both in each broken switch.
For easy disassembly unscrew both rectifier heatsinks from capacitors side and plastic shelf with AC
terminals and disassembly two M6 screws into down heatsink on opposite side.
Important note
– all diode threads have to be covered by very thin layer by No. 2 Electro Joint
Compound before replacing. Also heatsink side which is connected to DC-link has to be covered by
No.2 EJC.
Checking of output stage.
Output stage is made of IGBT modules assembled on main heatsink. Each module is covered by PCB
with gate resistors and protection diodes. For detection of transistors go in following order:
1. Check transistors’ gate resistance and if is lower than 800
Ω
it means transistor’s gate is
broken. For this test use measuring instrument and measure resistance between red and
black cables in pairs into control plug. If at least one pair’s resistance is lower than limit both
transistors have to be replaced.
2. Modules are working in parallel but are electrically working as single switch one diode and one
transistor.
3. Check chopper diode – using diode conduction tester check if between output “minus”
terminal and output “plus” terminal diode is conducting. After passing this test check if diode is
blocked ( non conducting) in opposite direction. If test is positive diodes are working properly.
4. Checking chopper transistor.
a. First measure resistance between output minus and battery minus terminals. If it is
short circuited at least one transistor is broken. Both transistors should be replaced.
b. If transistor gates are properly working and no short circuit is detected use 15V DC
100mA supply source and connect positive potential to red control cable and negative
to black control cable. After supplying gate transistor switch should be detected as
conducting between output minus and battery minus outputs. Battery minus is
available on second heatsink and DC-capacitors link and as additional washer with
connector on capacitors. Side
Summary of Contents for Origo Arc 410c
Page 6: ...5...
Page 8: ...7 OrigoTM Arc 410c...
Page 9: ...8 OrigoTM Arc 650c...
Page 10: ...9 OrigoTM Arc 810c...
Page 15: ...14 LM11 Component positions...
Page 22: ...21 CH21 Component positions...
Page 23: ...22 K69 Suppression circuit board Circuit diagram Component positions...
Page 38: ...37 NOTES...
Page 39: ......