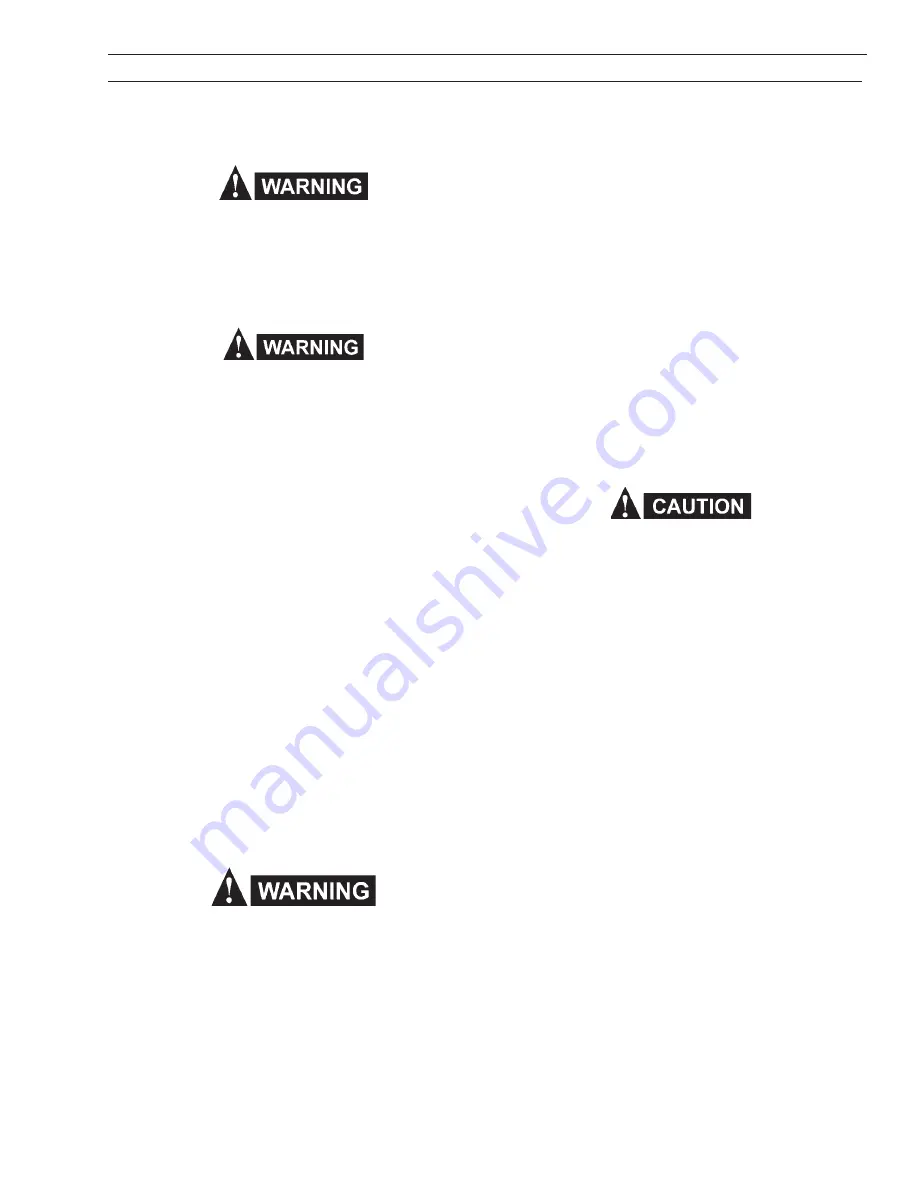
21
SECTION 5
MAINTENANCE
5.0 MAINTENANCE
5.1 MAINTENANCE AND SERVICE
Be sure that the branch circuit or main disconnect
switch and Multimaster power switch are off or elec-
trical input fuses are removed before attempting any
inspection or work inside the power source. Placing
the power switch on the power source in the off po-
sition does not remove all power from inside the
equipment.
Inspection, troubleshooting and repair of this equip-
ment may ordinarily be undertaken by a competent
individual having at least general experience in the
maintenance and repair of semi-conductor electronic
equipment. Maintenance or repair should not be un-
dertaken by anyone not having such qualifications.
Shut OFF shielding gas supply at source.
5.2 INSPECTION AND SERVICE
Keep equipment in clean and safe operating condition
free of oil, grease, and (in electrical part) liquid and me-
tallic particles which can cause short circuits.
Regularly check cylinder valves, regulators, hoses, and
gas connections for leaks with soap solution or leak test
solution (P/N 998771).
Check for and tighten loose hardware including electrical
connections. Loose power connections overheat during
welding.
Immediately replace all worn or damaged power cables
and connectors. Check for frayed and cracked insulation,
particularly in areas where conductors enter equipment.
The electrode wire and all metal parts in contact with it
are electrically energized while welding. Inspect these
parts periodically for defective insulation and other elec-
trical hazards.
If uninsulated cable and parts are not replaced, an
arc caused by a bare cable or part touching a
grounded surface may damage unprotected eyes or
start a fire. Body contact with a bare cable, connec-
tor, or uncovered conductor can cause a fatal shock.
Keep power cables dry, free of oil and grease, and pro-
tected at all times from damage by hot metal and sparks.
Clean dirt and metal particles from drive roll groove
weekly; replace roll if badly worn.
5.2.1 POWER SOURCE
5.2.1.1 RECTIFIERS AND TRANSISTORS
It is recommended that the internal components be
cleaned occasionally by blowing them out with low pres-
sure compressed air. This cleaning operation is neces-
sary so that maximum cooling will be accomplished by
the air stream. This should be done periodically, depend-
ing upon the location of the unit and the amount of dust
and dirt in the atmosphere.
The hermetically sealed diodes and transistors are spe-
cially designed for welding machine use and will not age
or deteriorate with use. The rectifiers are mounted on heat
sinks. A periodic cleaning of dust and dirt from these is
necessary to insure cooling of the rectifiers. Should any
rectifier need replacement, it can be quickly removed from
the heat sink.
5.2.1.2 FAN MOTOR
All models are equipped with an exhaust fan and rely on
forced draft for adequate cooling for high duty cycles and
overloads.
Do not use filters on this unit as they would restrict
the volume of intake air. Output ratings on this unit
are based on an unobstructed supply of cooling air
drawn over its internal components. Warranty is void
if any type of filtering device is used.
5.2.1.3 TRANSFORMER
Occasional blowing out of the dust and dirt from around
the transformer is recommended. This should be done
periodically depending upon the location of the unit and
the amount of dust and dirt in the atmosphere. The Power
Source case cover should be removed and a clean, dry
low pressure air stream should be used for this cleaning
operation.
5.2.1.4 OVER-TEMPERATURE PROTECTION
The Power Source is protected from high internal tem-
peratures by thermal switches. When the Power Source
is operated under high current applications for long peri-
ods, the thermal switches may reach a high temperature
causing it to de-energize the contactor. These thermal
switches will reset automatically after the heat sink or
transformer windings have cooled to a safe level. While
de-energized, the contactor can not be operated. But, if
the gun trigger is depressed, the unit will still feed wire
and the solenoid will operate.
5.2.2 WIRE FEEDER
As soft wire is fed, the drive rolls may pick up metal from
the wire surface. Accumulation on the rolls may score the
wire with resulting unwanted friction and improper feed-
ing.
Inspect the rolls regularly and clean them with a fine-wire
power brush. Avoid roughening, or removing the hard-
ness of groove surfaces in grooved rolls. Any roughening
may score the wire, just as the accumulation being re-
moved may do.
Summary of Contents for MultiMaster 160
Page 1: ...MultiMaster 160 Mig Tig Stick Welding Package F15 678 D 07 2005 Instruction Manual...
Page 4: ...4 Table of Contents...
Page 24: ...24 12 11 10 14 6 5 16 3 7 4 15 8 13 18 17 19 20 Feed Motor SECTION 6 REPLACEMENT PARTS...
Page 26: ...26 Multimaster 160 Bottom Plate 61 62 63 68 64 67 66 65 SECTION 6 REPLACEMENT PARTS...
Page 28: ...28 Notes...
Page 29: ...29 Notes...
Page 30: ...30 Notes...