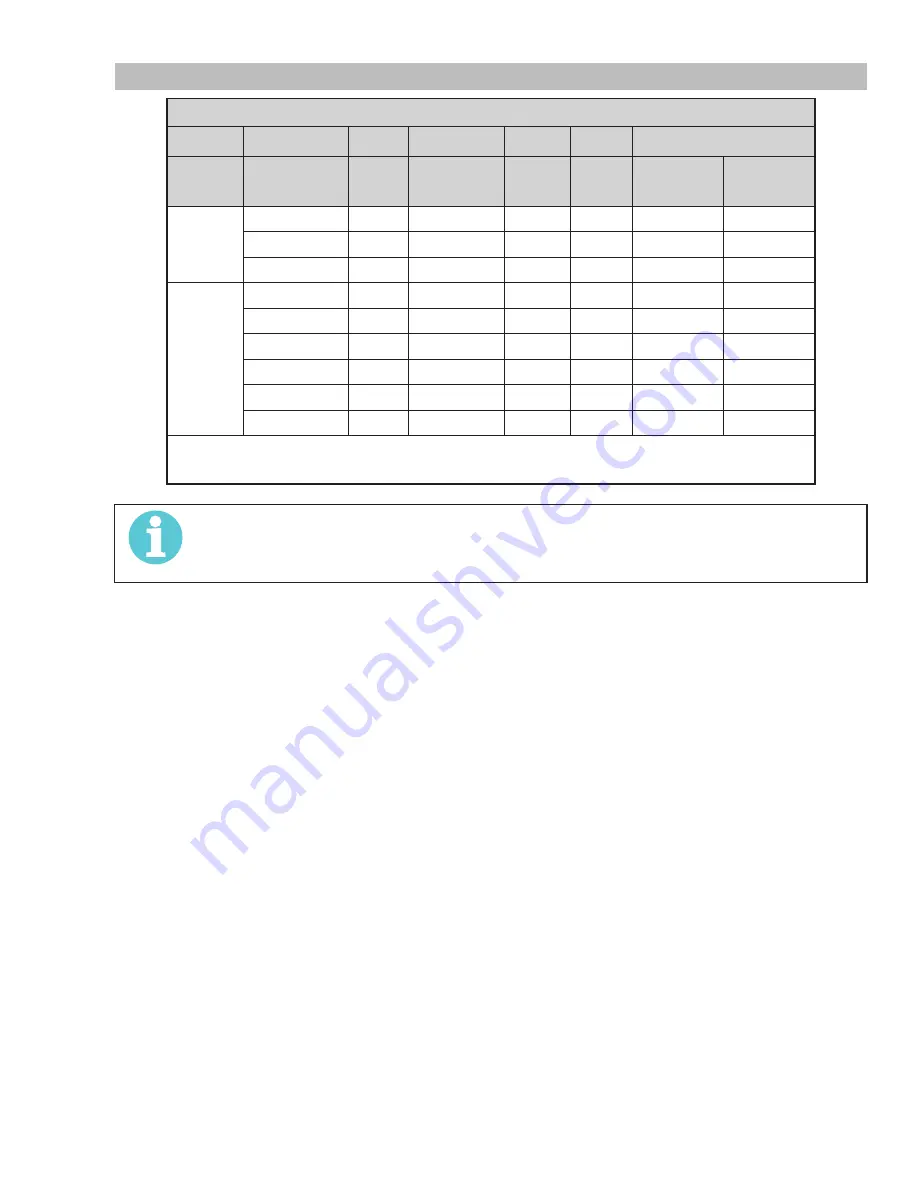
CUTMASTER A60
0-5428
INTRODUCTION
2-3
2.05 Input Wiring Specifications
Cutmaster A60 Power Supply Input Cable Wiring Requirements
Input voltage
Freq
Power Input
Suggested Sizes
Volts
Hz
kVA
I max
I eff
Fuse (amps)
Flexible Cord
(Min. AWG)
1 Phase
208
60
16
75
48
100
6
230
60
17
72
46
100
6
460
60
20
44
28
50
10
3 Phase
208
60
16
40
26
50
8
230
50/60
16
39
25
50
10
380
50/60
11.8
17
11
20
12
400
50/60
11.8
17
11
20
12
460
60
17
21
14
25
12
600
60
9.6
16
10
20
12
Line Voltages with Suggested Circuit Protection and Wire Sizes
Based on National Electric Code and Canadian Electric Code
NOTE!
Refer to Local and National Codes or local authority having jurisdiction for proper wiring require-
ments.
Cable size is de-rated based on the Duty Cycle of the equipment.
Summary of Contents for CUTMASTER A40
Page 5: ......
Page 8: ...This Page Intentionally Blank...
Page 18: ...CUTMASTER A60 INTRODUCTION 0 5428 2T 4 This Page Intentionally Blank...
Page 24: ...CUTMASTER A60 INSTALLATION 0 5428 3 6 This Page Intentionally Blank...
Page 32: ...CUTMASTER A60 OPERATION 0 5428 4 4 This Page Intentionally Blank...
Page 58: ...CUTMASTER A60 OPERATION 0 5428 4T 26 This page intentionally blank...
Page 59: ...CUTMASTER A60 0 5428 OPERATION 4T 27 This page intentionally blank...
Page 80: ...CUTMASTER A60 OPERATION 0 5428 4T 48 This Page Intentionally Blank...
Page 98: ...CUTMASTER A60 PARTS LIST 0 5428 6 8 This Page Intentionally Blank...
Page 111: ...This page intentionally blank...