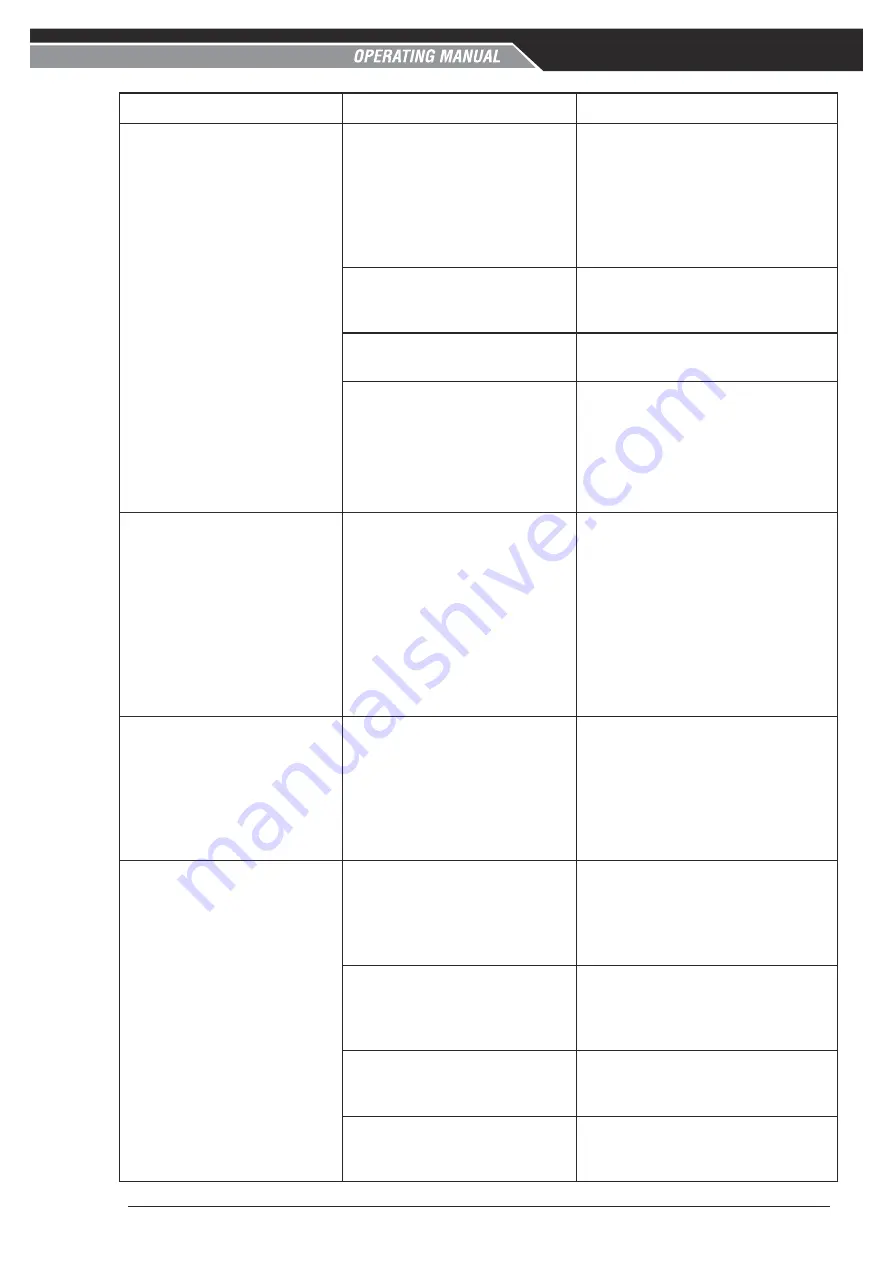
EasyWeld / HandyWeld 160
0-5617 7-3 SERVICE
PROBLEM
CAUSE
REMEDY
3
When welding at
maximum output (WFS
and Volts) the machine
stops welding.
A
When output amperage
exceeds the rated maximum
output of the machine by
15%, the welding machine
will sense this and initiates a
safety circuit which stops the
output current.
A
Reduce output amperage (WFS
and Volts).
B
Contact Tip of the MIG gun is
too close to the work piece.
B
Increase distance between the
Contact Tip of the MIG gun and
the work piece.
C
The Pre-set voltage is too
high.
C
Decrease the Pre-set voltage.
D The MIG Welding Wire in use
is not consistent with the
selected MIG wire diameter,
e.g. 0.8mm wire is selected
but 0.9mm wire is used.
D
Ensure that the correct MIG
Welding Wire Diameter is selected
for MIG Wire being used.
(In the case of Aluminium MIG
Wire Welding see Note in Section
5.10 page 5-12)
4
Mains Supply Voltage is
On, the On/Off switch in
the rear panel is in the On
position but the Power
On indicator on the front
panel is Not illuminated
and the digital displays on
the front panel are also not
illuminated and the power
source will not weld.
This may occur due to the
activation of an in-built
protective device if the Power
Source is repeatedly switched
On then Off rapidly or the
supply to the Power Source is
switched On then Off rapidly.
If this occurs leave the Power
Source On/Off switch in the Off
position for several minutes to
allow the protective device to
reset.
5
Over Temp Indicator is
illuminated in addition to
(E01) showing on Digital
Display) and the unit will
not commence welding
when the gun trigger
switch is depressed.
Duty cycle of power source
has been exceeded.
Leave the power source switched
ON and allow it to cool. Note
that Over Temp indicator must
be extinguished and (E01 Error
Code is cleared from the Digital
Display) prior to commencement
of welding.
6
Unit will not feed wire in
MIG mode.
A
Incorrect Feed Roll fitted for
wire type being used.
A
Fit the correct feed roll for MIG
wire type being used. Refer to
section 2.11 for optional feed rolls
available and Section 5.07 for feed
roll fitting details.
B
Pressure Roller Arm is not
secured in the correct position
or not correctly adjusted.
B
Secure Pressure Roller in the
correct position and ensure that
it is correctly adjusted. Refer to
Section 5.05 and 5.06.
C
Electrode wire stuck in
conduit liner or contact tip
(burn-back jam).
C
Check for clogged / kinked MIG
Gun conduit liner or worn contact
tip. Replace faulty components.
D Internal fault in power source
D
Have an Accredited CIGWELD
Service Provider investigate the
fault.
Summary of Contents for Cigweld EasyWeld 160
Page 8: ...This Page Intentionally Blank ...
Page 14: ...EasyWeld HandyWeld 160 GENERAL INFORMATION 1 6 0 5617 This Page Intentionally Blank ...
Page 26: ...EasyWeld HandyWeld 160 INSTALLATION 3 4 0 5617 This Page Intentionally Blank ...
Page 32: ...EasyWeld HandyWeld 160 OPERATION 4 6 0 5617 This Page Intentionally Blank ...
Page 56: ...MIG GMAW WELDING 5 24 Manual 0 5617 EasyWeld HandyWeld 160 This Page Intentionally Blank ...
Page 70: ...EasyWeld HandyWeld 160 STICK MMAW Welding 6 14 0 5617 This Page Intentionally Blank ...
Page 78: ...KEY SPARE PARTS 8 4 0 5617 EasyWeld HandyWeld 160 This Page Intentionally Blank ...
Page 80: ...EasyWeld HandyWeld 160 APPENDIX A 2 0 5617 This Page Intentionally Blank ...
Page 83: ...EasyWeld HandyWeld 160 This Page Intentionally Blank ...