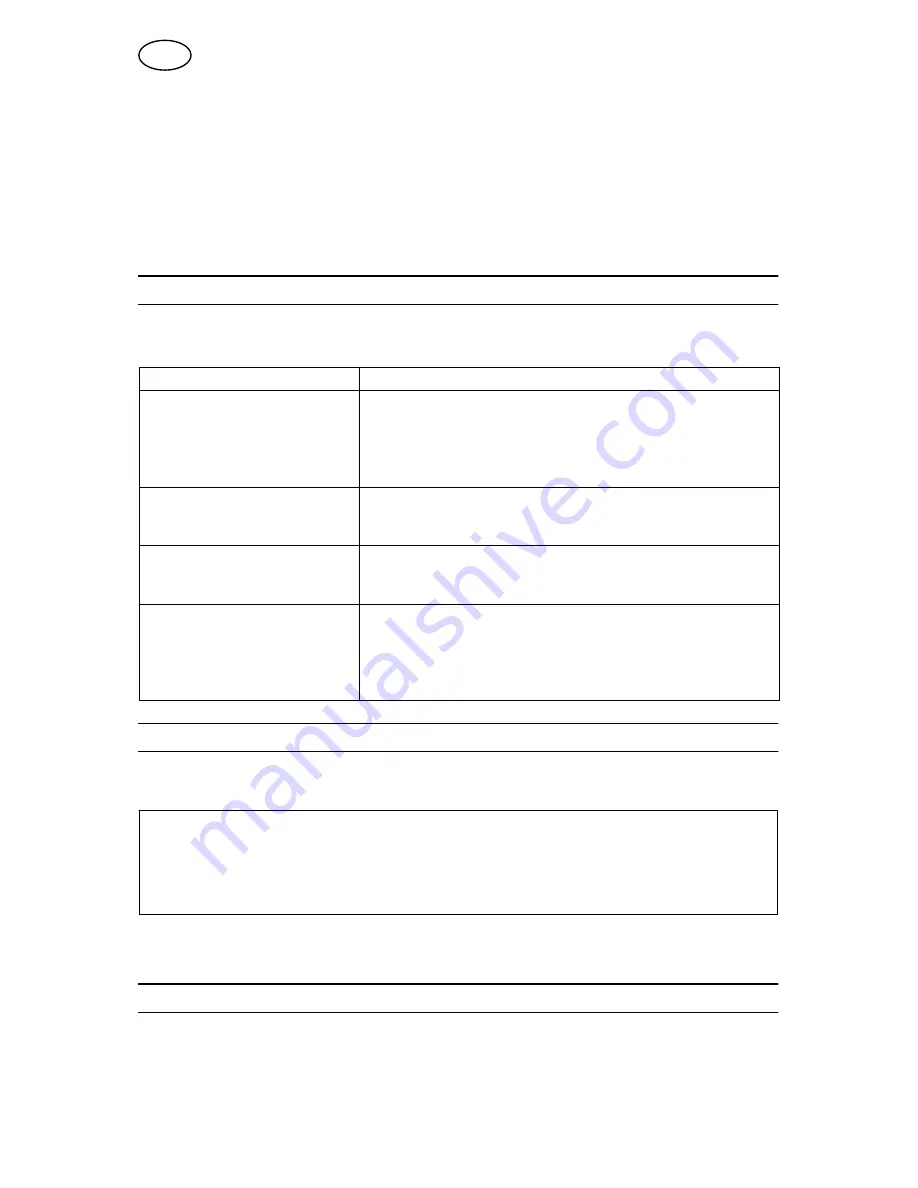
© ESAB AB2011
- 13 -
bh40d1e
It is normally sufficient to blow the power source with dry compressed air (reduced
pressure) once a year.
Clogged or blocked air inlets and outlets otherwise result in overheating.
6.2
Welding torch
Wear parts should be cleaned and replaced at regular intervals in order to achieve
trouble-free welding.
7
FAULT-TRACING
Try these recommended checks and inspections before sending for an authorized
service technician.
Type of fault
Corrective action
No arc.
Check that the mains power supply switch is turned on.
Check that the welding current supply and return cables are
correctly connected.
Check that the correct current value is set.
Check to see whether the MCB has tripped.
The welding current is
interrupted during welding.
Check whether the thermal cut-outs have tripped (indicated
by the orange lamp on the front panel).
Check the mains power supply fuses.
The thermal cut-out trips
frequently.
Check to see whether the dust filter is clogged.
Make sure that you are not exceeding the rated data for the
power source (i.e. that the unit is not being overloaded).
Poor welding performance.
Check that the welding current supply and return cables are
correctly connected.
Check that the correct current value is set.
Check that the correct electrodes are being used.
Check the gas flow.
8
ORDERING SPARE PARTS
Repair and electrical work should be performed by an authorised ESAB service
technician. Use only ESAB original spare and wear parts.
Arc 180, Arc 200 is designed and tested in accordance with the international and Euro
pean standards EN 60974-1 and EN 60974-10. It is the obligation of the service unit
which has carried out the service or repair work to make sure that the product still
conforms to the said standard.
Spare parts may be ordered through your nearest ESAB dealer, see the last page of
this publication.
9
DISMANTLING AND SCRAPPING
Welding equipment primarily consists of steel, plastic and non-ferrous metals, and
must be handled according to local environmental regulations.
Coolant must also be handled according to local environmental regulations.
GB
ARC WELDING SUPPLIES - 07 847 7870
Summary of Contents for Buddy Arc 180
Page 2: ...2 A R C W E L D I N G S U P P L I E S 0 7 8 4 7 7 8 7 0...
Page 14: ...Diagram 14 bh40e A R C W E L D I N G S U P P L I E S 0 7 8 4 7 7 8 7 0...
Page 15: ...15 bh40e A R C W E L D I N G S U P P L I E S 0 7 8 4 7 7 8 7 0...
Page 18: ...18 notes NOTES A R C W E L D I N G S U P P L I E S 0 7 8 4 7 7 8 7 0...
Page 19: ...19 notes NOTES A R C W E L D I N G S U P P L I E S 0 7 8 4 7 7 8 7 0...