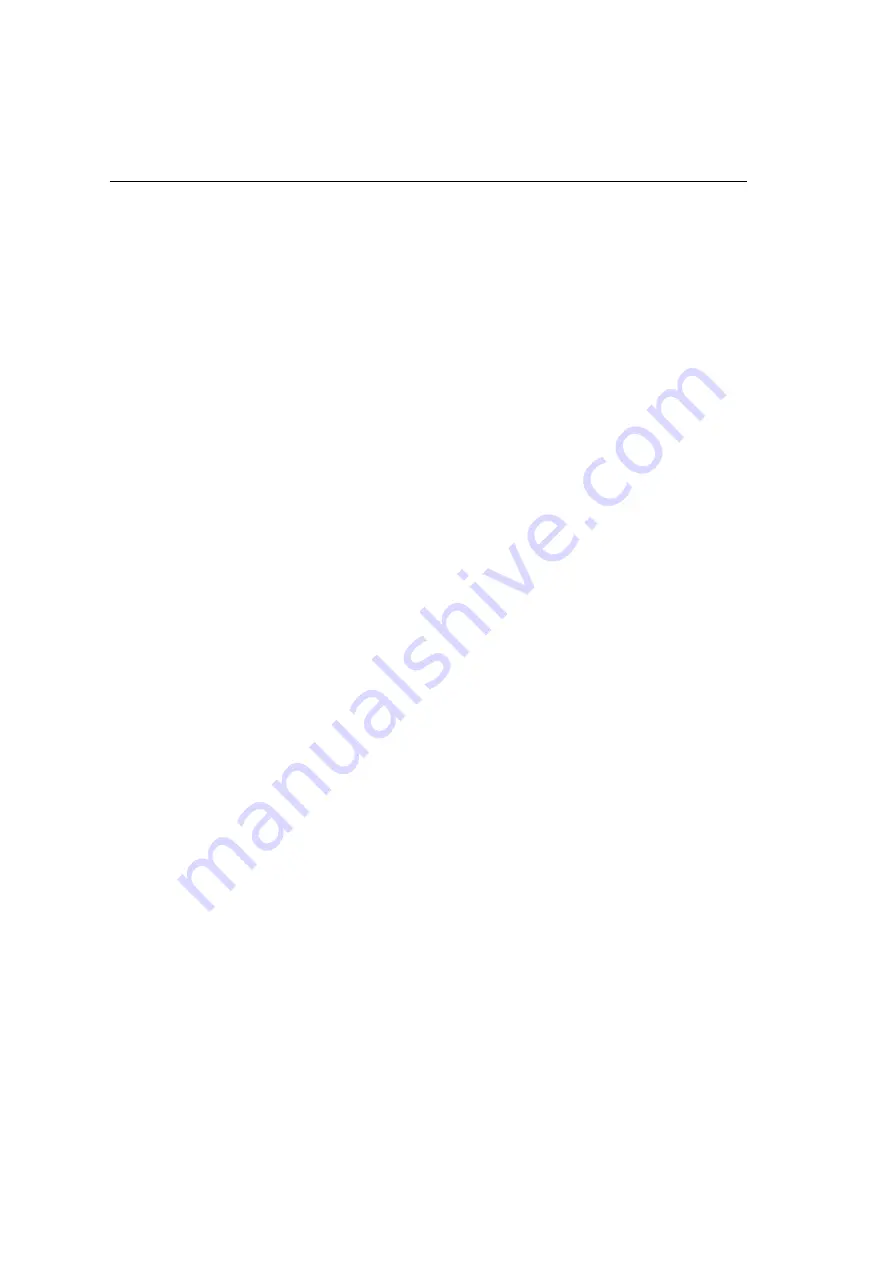
- 51 -
10
REPAIRS ON A4, A5, A9, A10, A11, A12, A13, A14
We advise you to renew the heat sink module.
If an individual repair is urgently required, take into account the information given below:
Only components of identical type may be connected in parallel on any of the switches.
Due to changes made by component manufacturers and the resulting tolerances, your unit may
be equipped with power transistors (SGS-Thomson identification: ISOTOP Module) which are no
longer available.
In this case, all the transistors or diodes which are connected in parallel in a switch must be re-
newed when a defect occurs.
The screws fitted to the electrical connecting lugs should be tightened to a torque of about 15 Nm.
The screws fitted to retain the component on the heat sink should be tightened to a torque of ap-
prox. 20 Nm.
Make sure there is a good heat transfer from the component to the heat sink; the contact area of
the power conductors must be clean and smooth.
•
Apply a thin film of heat-conducting paste.
•
Check the gate series resistors.
•
Check contacts between board and ISOTOP modules as well as the connections to the
cable harness.
•
Check the RC elements and the blocking capacitors.
•
Check the power boards (strip conductors, etc.).
11
POTENTIOMETER ON CONTROL PANEL A2-2 DEFECTIVE
Features or functions indicating a defective potentiometer:
•
Missing pins
•
Allow potentiometer or switch to rotate through the full range
•
No end stop
•
Interruptions occur during welding (loose contact).
To check during the welding process, turn and shake the potentiometer.
When renewing, note the following instructions:
•
The coding disc on switches must be properly fitted.
•
Take care not to damage components when cutting pins to length. Always clamp the pins.
•
Re-insert spacers correctly.
•
Use only plastic potentiometers (to ensure insulation).
•
Check that the potentiometer has the specified ohmage. Remember there is a difference
between linear and logarithmic.
•
When dismantling, match-mark ribbon cables and related components to prevent mixing
them up when re-connecting. There are several 20-way ribbon cables connected.
Summary of Contents for Aristotig 405 AC/DC
Page 1: ...0458 165 002 9910 DTG 405 Aristotig 405 AC DC Welding rectifier Service manual...
Page 9: ...9 NOTES...
Page 10: ...10 CONNECTION DIAGRAM DTG 405...
Page 11: ...11...
Page 15: ...15 NOTES...
Page 16: ...16 BLOCK DIAGRAM DTG 405 405a pcx...
Page 17: ...17 Warning Some parts of this circuit are connected to mains voltage potential 405b pcx...
Page 27: ...27 A2 COMPONENT POSITIONS a2 1b pcx a2 2b pcx...
Page 40: ...40 A9 A13 COMPONENT POSITIONS A10 A14 COMPONENT POSITIONS...
Page 62: ...62 8 WAVEFORM AC2 SMOOTH WAVE ac2 pcx...
Page 81: ...81 NOTES...
Page 91: ...page...