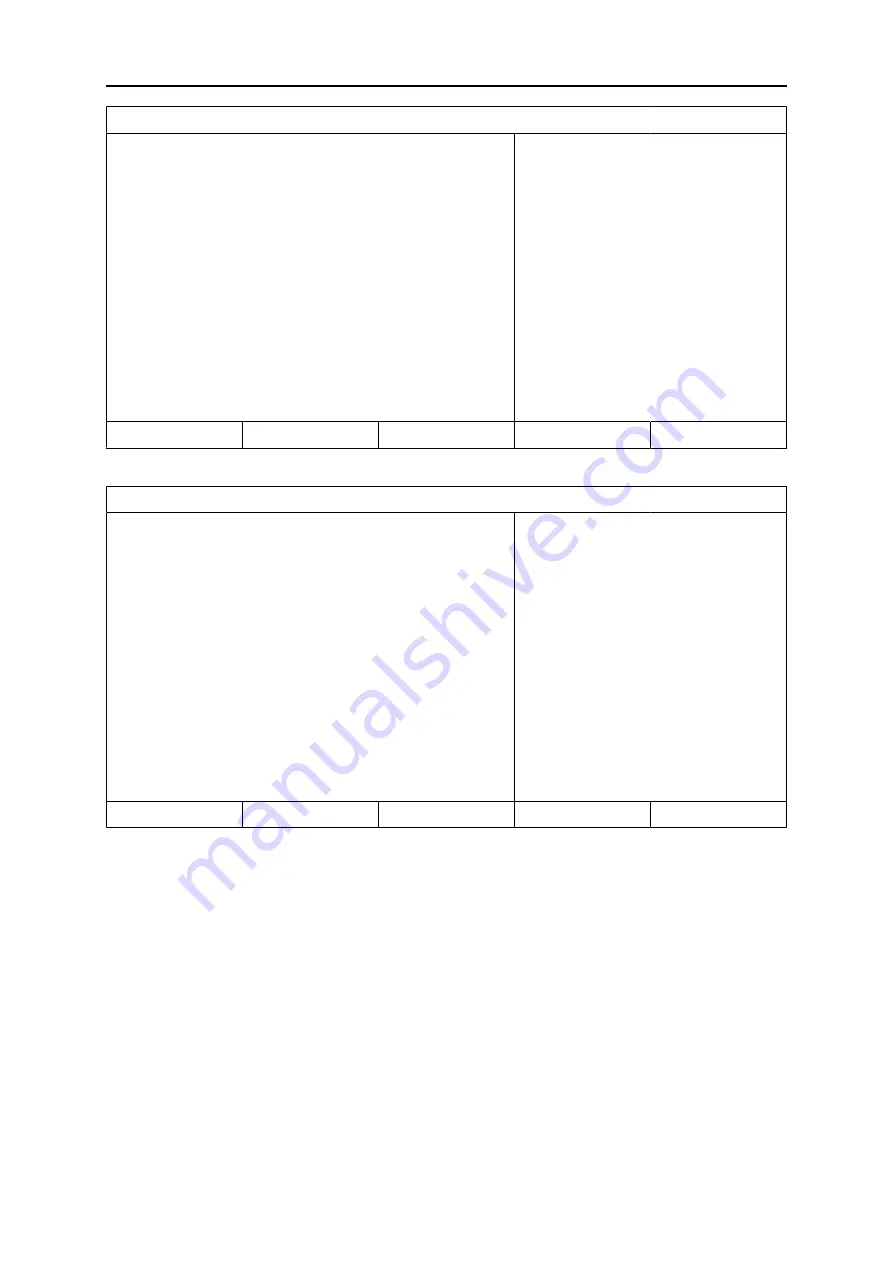
2 MENUS
0460 949 474
- 13 -
© ESAB AB 2021
SAW WELD DATA SETTING
VOLTAGE
CURRENT
TRAVEL SPEED
DIRECTION
START DATA►
STOP DATA►
REGULATION PAR.►
SETTING LIMITS►
MEASURE LIMITS►
POLARITY
20.5 V
395 A
0 cm/min
■
AUTO
DC+
QUIT
Another example of the menu with Aristo® 1000:
SAW WELD DATA SETTING
VOLTAGE
CURRENT
TRAVEL SPEED
DIRECTION
AC FREQUENCY
AC BALANCE
AC OFFSET
START DATA►
STOP DATA►
REGULATION PAR.►
24.0 V
3200 A
30 cm/min
■
50 HZ
50%
0 V
QUIT
Example of the menu with LAF/ TAF power source