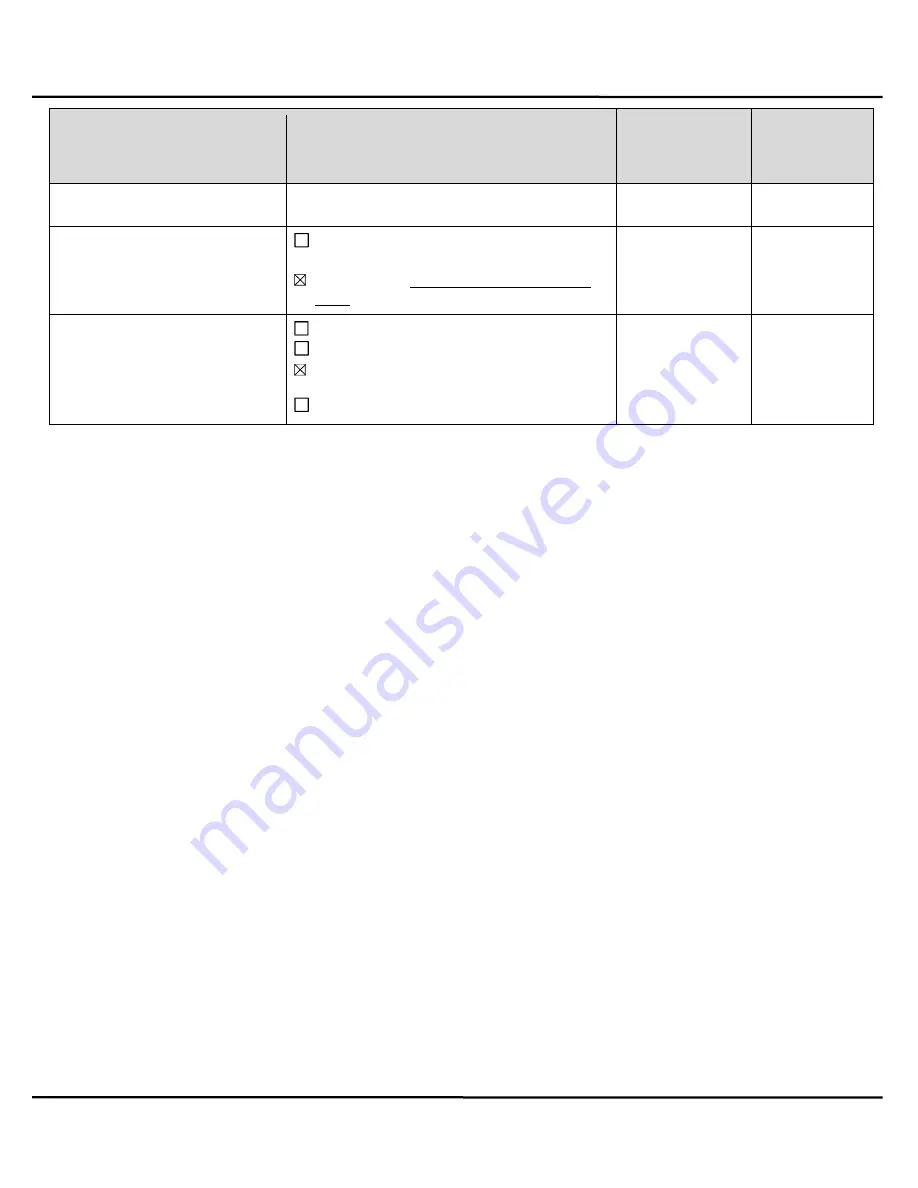
D05125R01.20
F-PRO 116 User Manual
Appendix G-5
1.2
SERIAL CONNECTIONS
Capabilities
Current Value
If configurable,
list methods
1.2.1
Port Name
CON 2
1.2.2
Serial Connection
Parameters:
Asynchronous -
8 Data Bits, 1 Start Bit,
1 Stop Bit, No Parity
Other, explain
–
Asynchronous with selectable
parity
Parity - None
F-PRO 1000
Offliner
1.2.3
Baud Rate:
Fixed at _______
Configurable, range _______ to _______
Configurable, selectable from 2400, 4800, 9600,
19200, 38400 and 57600
Configurable, other, describe_______________
9600
F-PRO 1000
Offliner
Summary of Contents for F-PRO 116
Page 2: ......
Page 12: ...1 2 F PRO 116 User Manual D05125R01 20 Figure 1 1 F PRO 116 Relay Function Line Diagram...
Page 16: ...1 6 F PRO 116 User Manual D05125R01 20 Figure 1 4 Ordering Template...
Page 20: ......
Page 30: ......
Page 84: ...7 12 F PRO 116 User Manual D05125R01 20 Figure 7 10 Point Map...
Page 94: ......
Page 96: ......
Page 124: ......
Page 148: ......
Page 149: ...D05125R01 20 F PRO 116 User Manual Appendix H 1 Appendix H Mechanical Drawings H 1 Front View...
Page 150: ...Appendix H 2 F PRO 116 User Manual D05125R01 20 H 2 Rear View...
Page 151: ...D05125R01 20 F PRO 116 User Manual Appendix I 1 Appendix I AC Schematic Drawing...
Page 152: ......
Page 153: ...D05125R01 20 F PRO 116 User Manual Appendix J 1 Appendix J DC Schematic Drawing...
Page 154: ......
Page 155: ...D05125R01 20 F PRO 116 User Manual Appendix K 1 Appendix K Connection Diagram...
Page 156: ......