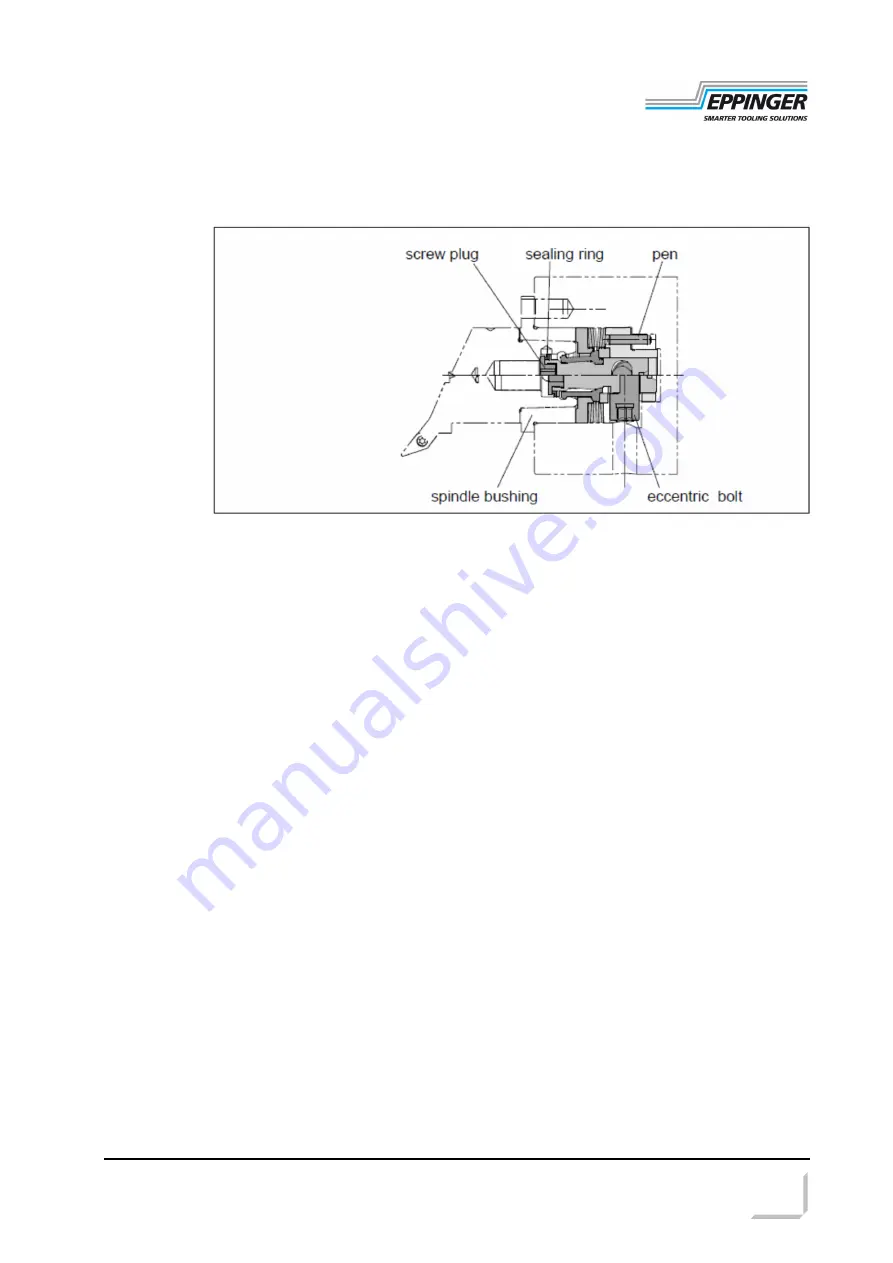
Product Information
PSC SVC
______________________________________________________________________________
Subject
to
modification
due
to
technical
advance!
95.700.007.D.E
/
2015
‐
04
6
3 Assembly
Check
Disassembly
clean and grease inside contour (KLÜBER Wolfracoat C)
slide in clamping unit;
ensure the correct position pen / hole
slide in the spindle bushing (interface fit);
ensure the correct position pen / hole
fix the spindle bushing
test pull-in force;
we recommend: use
Power-Check
unscrew the fixing screws of the spindle bushing
screw in the setscrews into the threads of the basic holder; let them protrude
screw in the screws into the draw-off threads and press out spindle bushing
uniformly
pull out clamping unit