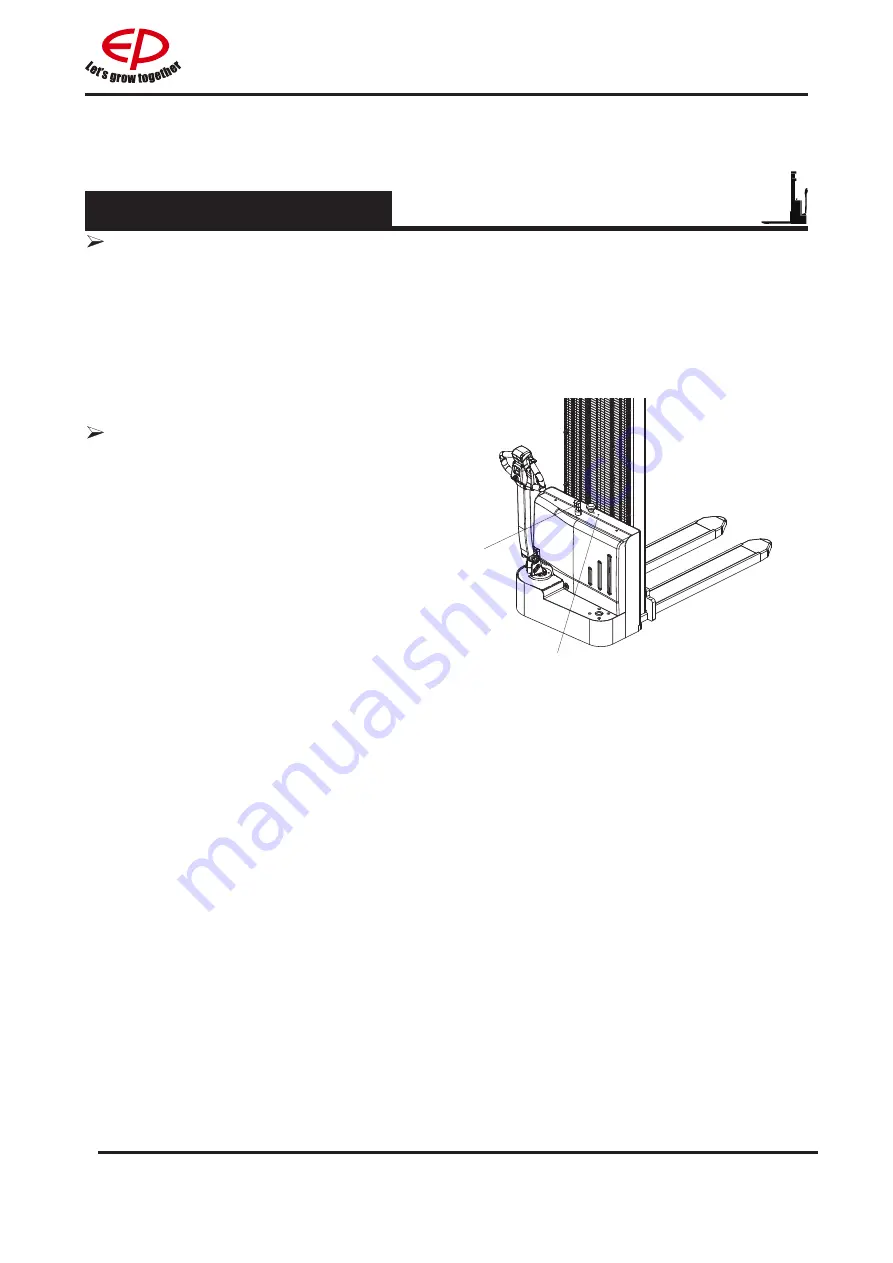
REV. 12/2020
3
C
Park the truck in the designated charging area.
Pull the charger cord (1) from the truck and
examine it for damage. If undamaged, plug
the charger into voltage range 100-240V,
50/60Hz wall outlet. As long as the built-in
charger is connected to the outlet ,the truck
should not be moved.
Charging the battery with internal charger
1
2
1.2.1 Battery charging
The vehicle must be parked in a wellventilated room.
There must be no metal parts on the surface of the battery.
Before charging, check all cables and plug connections for visible damage.
Before and after charging, make sure power is turned OFF.
It is essential to follow the safety regulations of the battery charging provided by their
manufacturers.
Precautions
1.2 Handling the battery