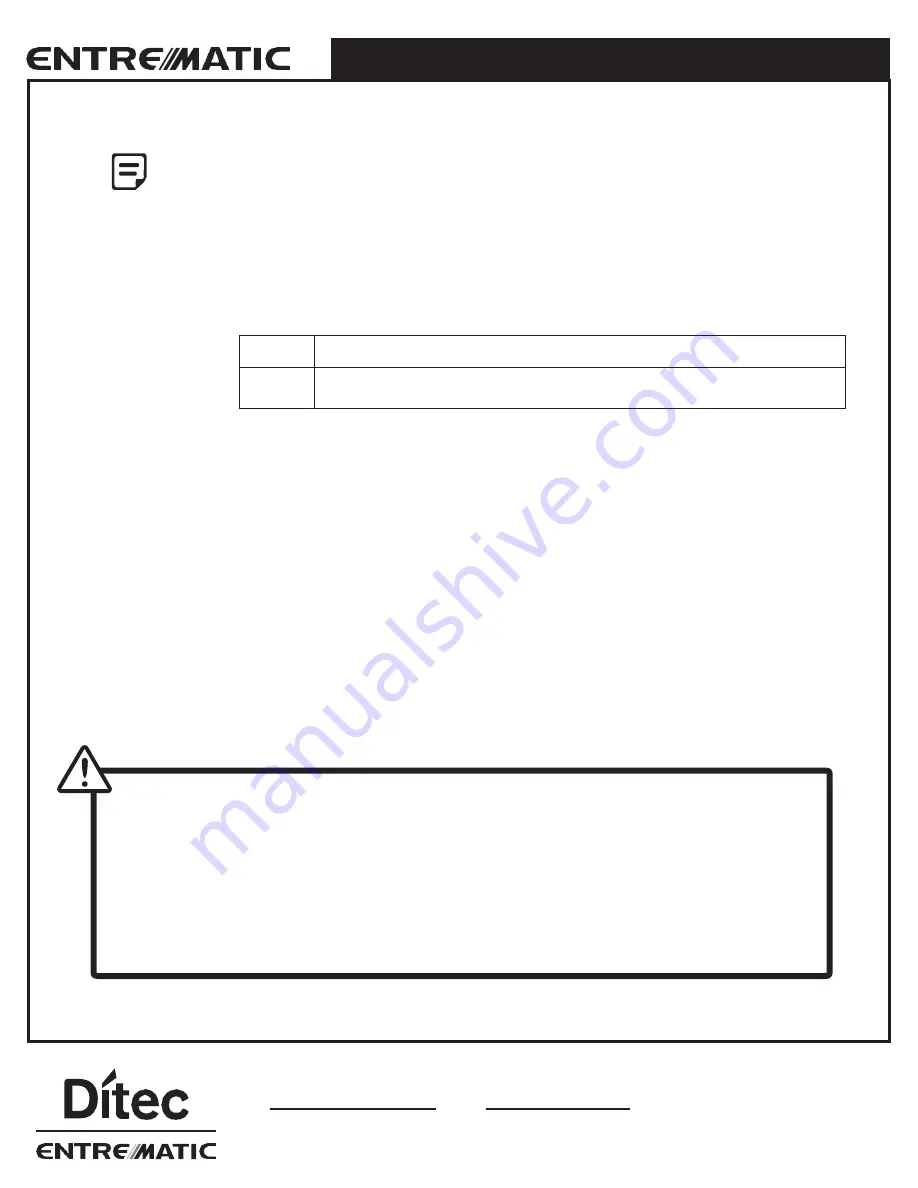
Entrematic Canada Inc.
Toll Free: 1-877-348-6837
[email protected]
www.ditecentrematic.ca
Entrematic USA Inc.
Toll Free: 1-866-901-4284
[email protected]
www.ditecentrematic.us
Pg. 42
HA8-LP Manual V. 4.0
8.1
Programming Specification (Digital Board)
• To make changes to the program setting, set 3-position switch to Automatic (I).
• Product will not operate when Slide Switch is set to Program mode.
There are two 7 SEGMENT LED DISPLAYS used for programming:
Function LED
= Programmed Function
Setting LED
= Value of the Function indicate on First digit
There are 3 switches that relate to programming:
Slide switch
PASS push button
To select the next function
SET push button
To change the present function value (when the Slide switch is in PROGRAM mode).
Adjusting Settings
– Slide Program/Run Switch to:
1 PROGRAM MODE- Functions can be modified.
2 RUN MODE- Function settings can be viewed but not modified.
Programming:
1 Move PROG/RUN Switch to
‘PROGRAM’
2 Press PASS Button to scroll through Functions
3 Press SET Button to change present function value
4
Move PROG/RUN Switch to ‘RUN’ when adjustment is complete
5 Press Activation to test.
OVERLOAD (Opening Torque Adjustment)
Overload is the Torque Adjustment setting for the amount of pressure with which the door pushes
against an obstruction, before cutting OFF for safety.
Overload POT - Basic Setting Position for a Standard Door.
1 Turn Overload pot fully counter-clockwise
– followed by ¼ turn clockwise.
2
Red Overload LED should not go ‘on’ when opening.
3 Test with obstruction
– door will cut power after about 2 sec and close by spring pressure.
8.0 CONTROL BOARD PROGRAMMING
RUN
Function settings can be viewed but Not modified.
PROG
(Program)
Function settings can be modified. As a safety feature,
THE DOOR WILL NOT OPEN WHEN THE SLIDE SWITCH IS SET TO PROG.