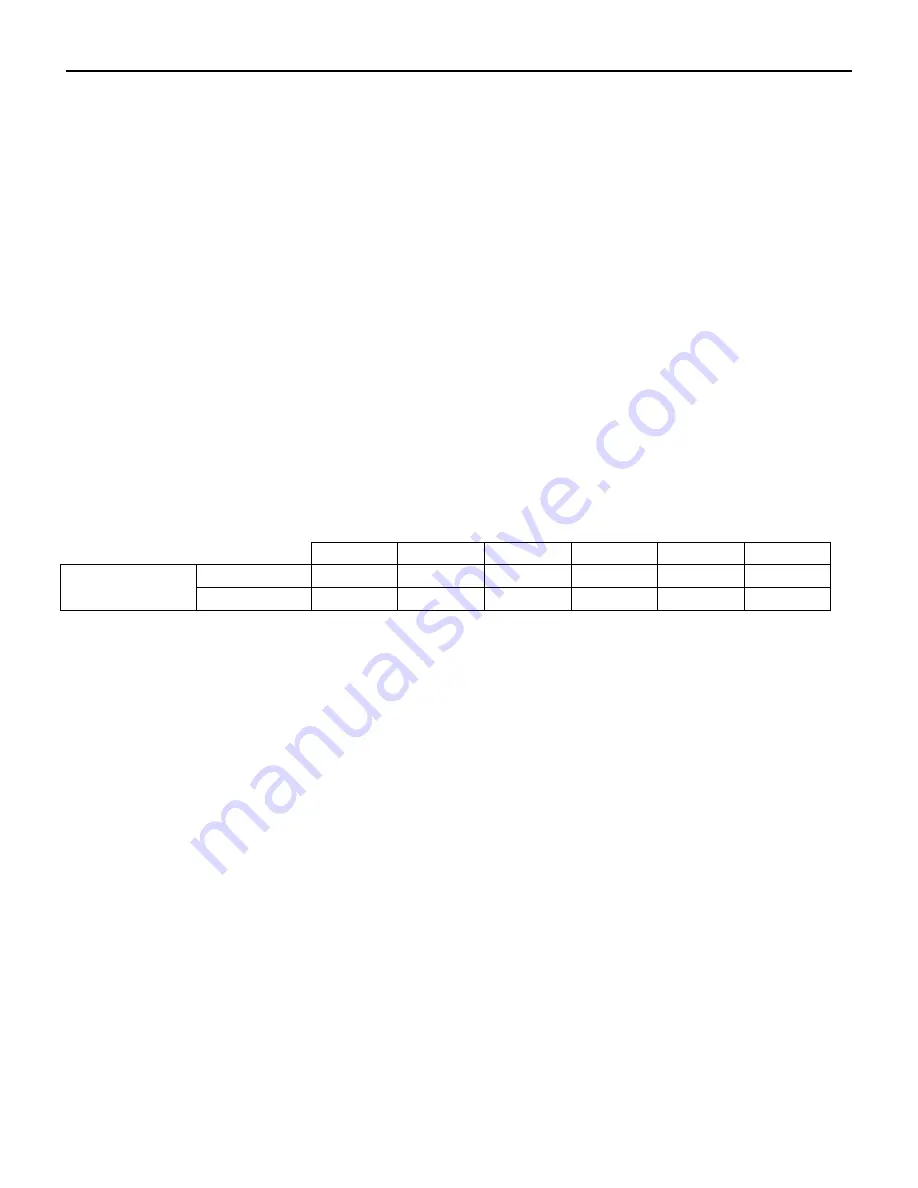
A
W-TRAC
IOM‐49
8 of 12
Mar 99 R4
If the outside air temperature is warmer than the exhaust air the W‐TRAC will enter ‘cool mode’ and
rotate the heat wheel to transfer heat from the outside air to the exhaust.
BASE
SETPOINT
The W‐TRAC is designed to be a discharge air temperature controller. The base discharge air temperature
is set from the setpoint control knob located on the face of the W‐TRAC.
SETPOINT
RESET
The base discharge air temperature is often modified from a remote signal to maintain the desired
temperature of the supplied space. This is called
reset
. The W‐TRAC discharge temperature can be reset
from a variety of sources using a 0‐10 VDC signal.
An offset to the BMS input range can be implemented by adding a 7.5k resistor in series with terminal S.
The following table describes the change of discharge setpoint from the input voltage (to terminals S + and
C1 ‐), with a setpoint fixed at 66°F. Refer to the equipment function page for the design reset range.
Input Voltage
0.0
2.0
4.0
6.0
8.0
10.0
Discharge
Setpoint (°F/°C)
No Resistor
30 / ‐1
40 / 4
45 / 7
52 / 11
60 / 15
66 / 19
7.5k Resistor
48 / 9
53 / 12
56 / 13
59 / 15
63 / 17
66 / 19
FROST
CONTROL
Frost should not be allowed to build up on the wheel. It is necessary to reduce the amount of heat
recovered when the outside temperature is below the freezing point (0°C / 32°F) and the exhaust leaving
temperature falls to a point that frost can begin to form. Frost may damage the wheel and reduce airflow.
Operating the heat wheel close to the frost threshold temperature will provide maximum energy recovery.
There are 3 different methods of providing frost control, all of which reduce the heat wheel rotation
speed.
EXHAUST
AIR
RH%
SENSOR
This method of control requires a humidity sensor connected across terminals EXH and C2. DIP 1 and 3
must be OFF, DIP 2 must be ON. The sensor is installed in the exhaust air section, just after the heat
wheel.