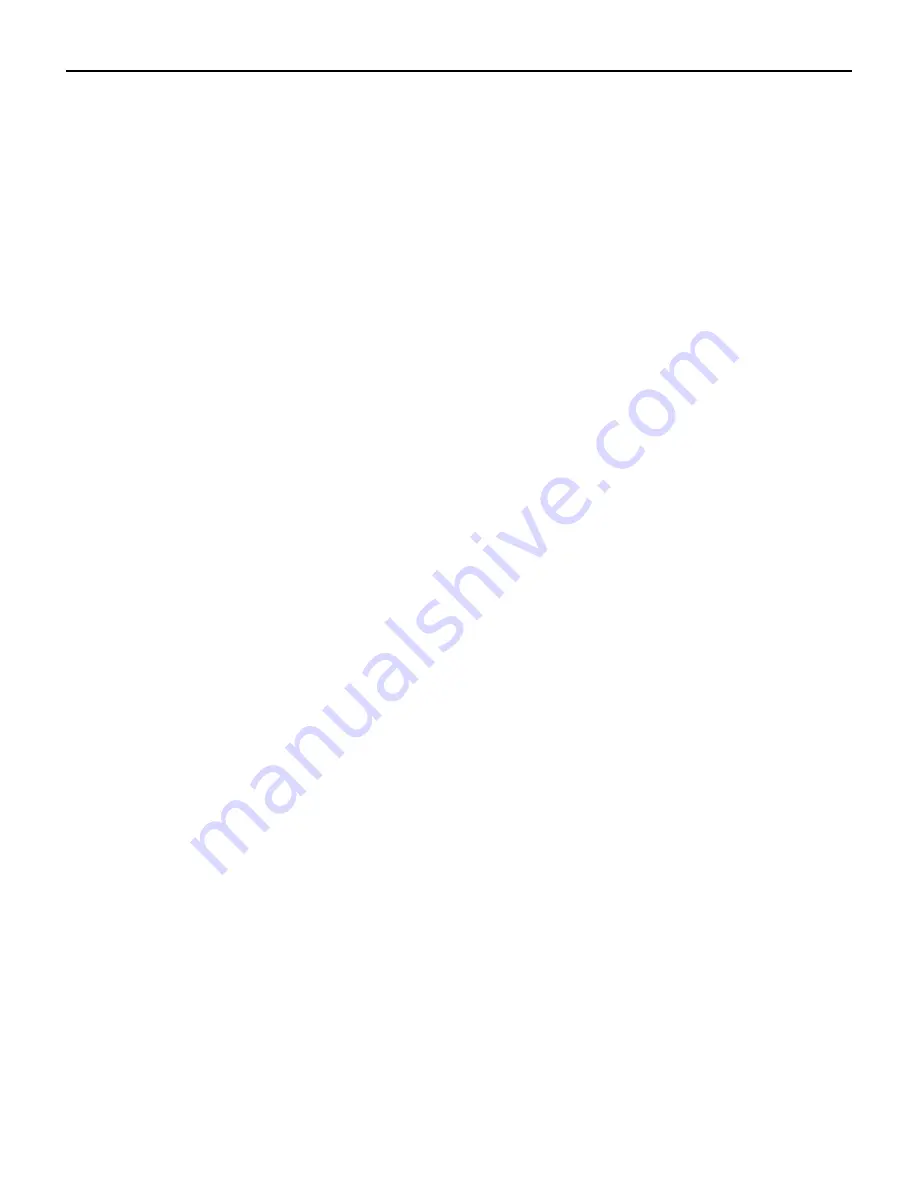
A
W-TRAC
IOM‐49
11 of 12
Mar 99 R4
Low Speed
Turn on DIP 5 to drive the output to minimum (0Vdc). Adjust the minimum speed pot on the KBVF
inverter drive until the heat wheel just begins to turn, usually between 0.5 and 2 rpm. Turn the power off,
and then restart the system to confirm the motor has enough starting torque to reliably start rotating the
heat wheel.
Return all DIP switches to their original position.
WHEEL
ROTATION
SPEED
Maximum wheel rotation speed will be factory set in the range of 30‐40 rpm, at 60 Hz, depending on the
size of the heat wheel.
Minimum wheel speed is dependent on the starting torque of the motor and heat wheel, usually between
0.5 and 2 rpm.
SENSOR
CALIBRATION
Discharge Temperature Calibration
Remove the supply air temperature sensor and measure both the sensor resistance and the temperature
at the sensing element. Compare these readings to the sensor table values. If the resistance is out by
more than 16 ohms, replace the sensor.
Measuring a sensor temperature between 60 – 70°F, slowly rotate the temperature setpoint dial
counter clockwise until the ‘Discharge Too Hot’ light just comes on.
Slowly increase the temperature setpoint dial until the light goes off.
The setpoint should match the sensed temperature measurement. If not, adjust the calibration pot
and repeat test.
Exhaust Temperature Calibration
Remove the exhaust air temperature sensor and measure both the sensor resistance and the temperature
at the sensing element. Compare these readings to the sensor table values. If the resistance is out by
more than 16 ohms, replace the sensor. The ‘bad sensor’ LED may turn on and off during this procedure.
Place a jumper wire across terminals A and C1.
Remove the exhaust temperature sensor and replace with a 909 Ω resistor.
Note the position of the BDRH pot, and then adjust to position 2.