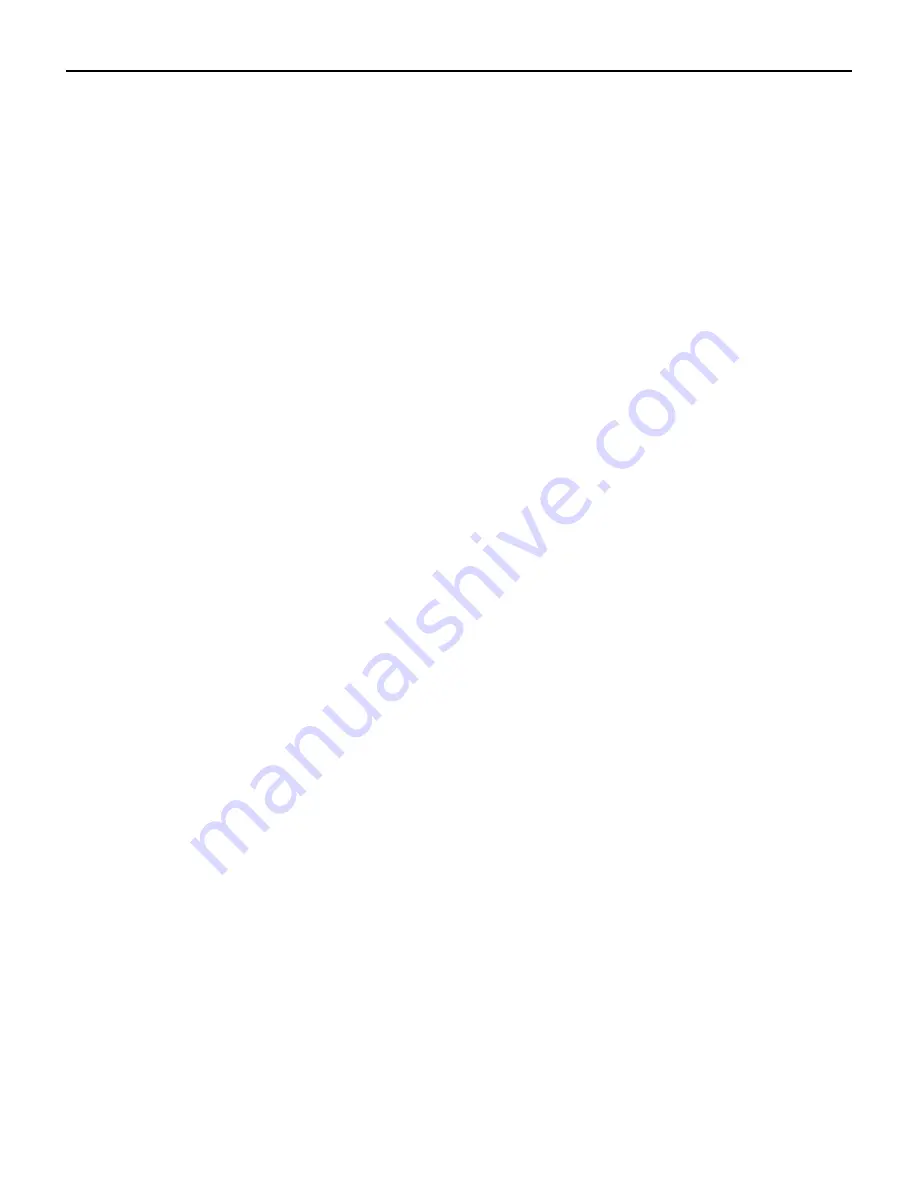
A
W-TRAC
IOM‐49
10 of 12
Mar 99 R4
(over 50 ft. eq. length), the use of a minimum 20 gauge‐shielded wire is recommended. The shield should
be grounded at the controller end only, with the other end taped.
It is important to ensure correct polarity when wiring into the system.
NOTE: Field analog control inputs require signal isolation to prevent ground loop
signal corruption and/or damage to the controller(s).
SERVICE
NOTES
ROTATION
Most heat wheels have a purge section to purge exhaust air trapped in the wheel flutes before they rotate
to the supply air side. The correct wheel rotation direction is noted on the face of the heat wheel. Drive
motor rotation may be changed at the motor wire connections or on the inverter drive feeding the motor
(if used).
MOTOR
SPEED
CONTROL
The modulating 0‐10Vdc motor speed output may be connected to a variety of controllers and/or
inverters. Refer to the equipment wiring diagram for connection details. The following setup parameters
are typical. Always refer to the equipment function sheet for any changes. To ensure proper setup
operation, do not have DIP 4 and DIP 5 on at the same time.
KBVF / SIVF(R)
The KBVF inverter drive and SIVF signal isolator are manufactured by KB Electronics Inc. The inverter and
isolator installation and operation manuals are included in the information package, originally located in
the main equipment electrical panel. The 0‐10Vdc W‐TRAC control output feeds into the SIVF signal
isolator which, in turn, feeds an isolated 0‐5Vdc signal to the KBVF inverter drive.
High Speed
Turn on W‐TRAC DIP 4 to force the W‐TRAC to maximum output (near 10Vdc). Note that if the
W‐TRAC is operating in frost mode DIP 4 will not allow the drive to go to full speed. Measure the motor
amps and confirm the readings are less than the maximum motor ampacity. If possible, measure and
confirm the output frequency is 60Hz.
The KBVF is factory set to 100% of rated frequency (60Hz) and should not be adjusted.